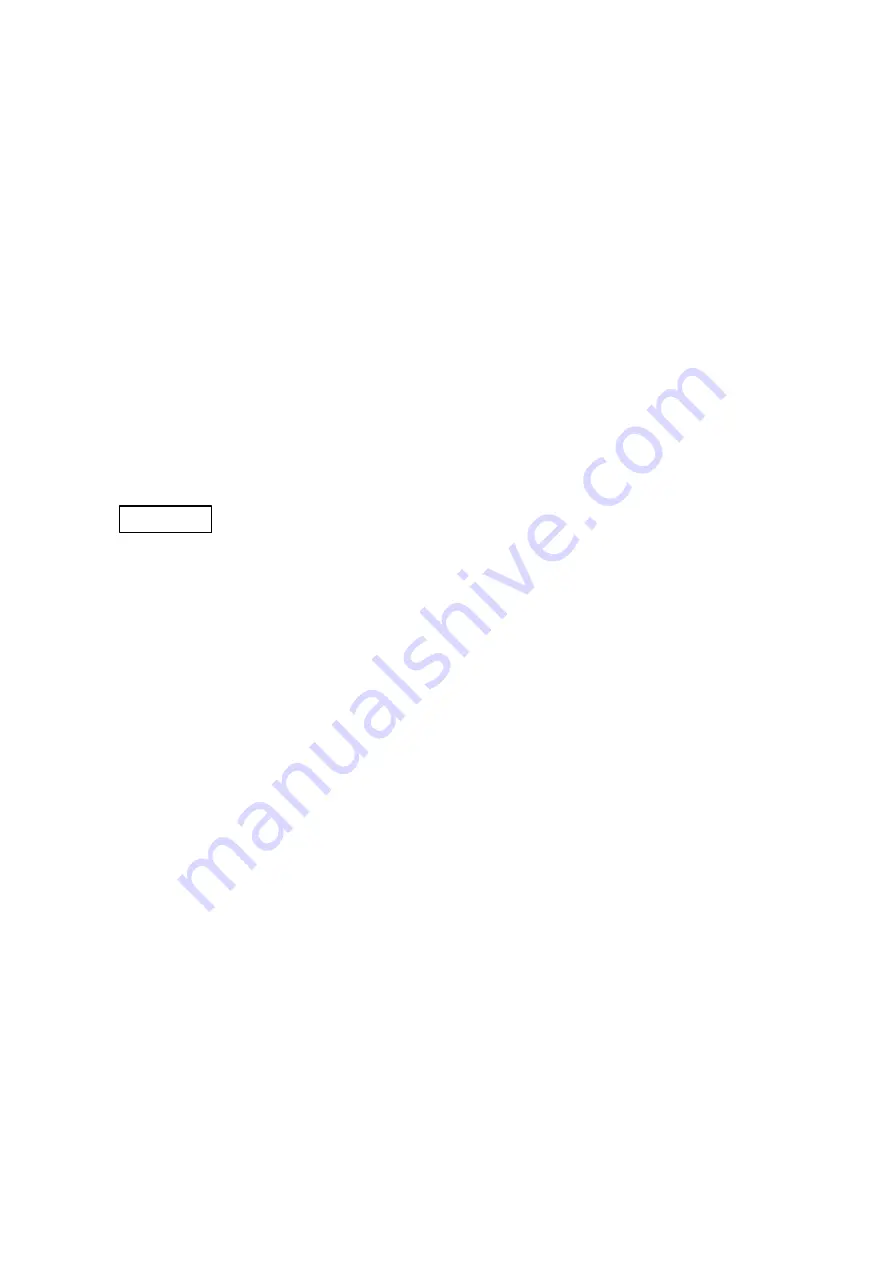
5.7 Mounting the drive unit
With moderate pressure on the pin (105), push the venturi insert (101) into the vertically positioned mixer body (130)
up to the mechanical stop. Then place the threaded rod (111) on the end of the pin up to the mechanical stop.
In the process, it must be ensured that the threaded rod is positioned over its hole in the fixing washer of the cylinder
pin (134). By tightening the threaded pin (110), the pin is fixed in the hold. Secure the threaded pin with a low-strength
thread locker (e.g. LOCTITE 221).
Place the stepper motor (113) on the threaded pin and screw it on by rotating the stepper motor spindle up to
the mechanical stop on the flange of the induction elbow (133). Fasten the stepper motor on the induction elbow
with four cylinder screws (112); in the process, observe the tightening torque for the screws (Table 4).
Place the receptacle (115) on the stepper motor spindle and align it to the desired side with the sensor fastening
thread (alignment in the direction of the output flange of the induction elbow is not possible due to the spatial
constraints), and install the cylinder screws (116).
Slide the washer (119) on as shown under
6.1
until the mechanical stop of the threaded rod is reached and fasten
with an M6 hexagon nut (120). Observe the tightening torque (Table 4, page 8).
Then fit the cap (121) and screw in the inspection glass (109) with seal in the induction elbow.
5.8 Adjusting the proximity sensors (limit switches)
Connect the stepper motor (113) of the mixer to the stepper motor control.
Adjust a mixing gap of 0.5 + 0.1 mm by moving the stepper motor. An adjustment of 0.5 mm takes place with
a control frequency of 20 Hz in full step operation in 5 seconds.
With a change to the control frequency by a factor K, the adjusting time changes by the
factor 1/K.
With a change to the step precision by a factor 1/F, the adjusting time changes by the factor F.
With an adjustment of both parameters, factors F and 1/K are multiplied.
Adjust the switching point of the “lean” position by screwing in the proximity sensor (117). Screw in the proximity
sensor until the LED on the sensor goes out. Then lock the proximity sensor in its position by tightening the
counter nut. Observe the tightening torque according to section
6.1 Spare parts drawing.
If the device is equipped with two sensors, the switching point for the “rich” position is adjusted first (max. mixing
gap width). For this purpose, increase the mixing gap an additional 4.5 mm from the “lean” switching point by
moving the stepper motor (total gap width 5 + 0.1 mm). In full step operation the additional adjustment at
a 60 Hz step frequency takes place in 15 seconds. Observe the notice above.
The adjustment of the screw-in position of the proximity sensor, “rich” switching point, takes place analogously to the
adjustment of the “lean” switching point. Then lock the sensor in place here as well by tightening the counter nut.
Note
985.29-2 p.11