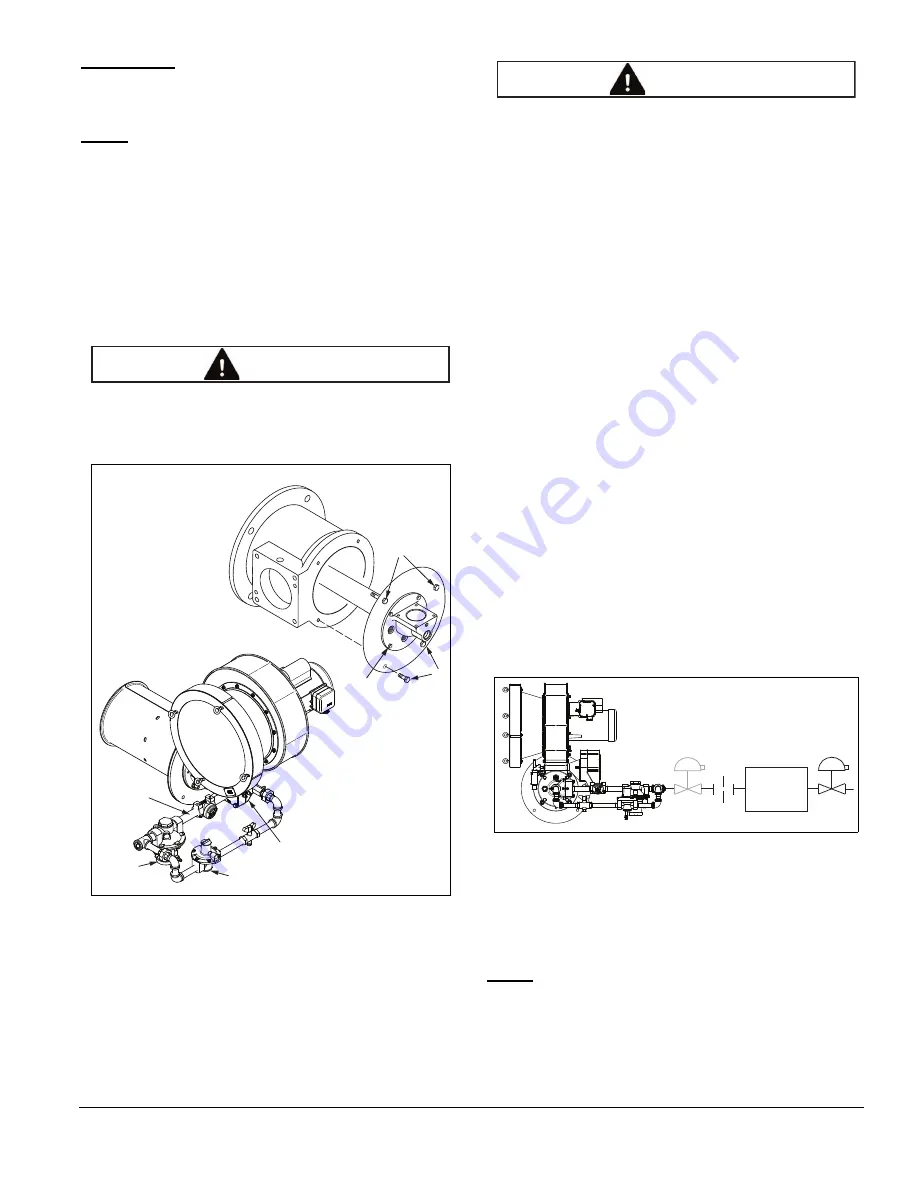
9
32-00057—01
Gas Piping
Burner Piping
The burner is factory assembled and shipped as ordered.
NOTE:
If it is necessary to redirect piping, remove
the
outer four bolts only
. Rotate the rear cover and
replace bolts. When reassembling, be sure that:
• ratio regulator spring column
is pointing down
• the bypass regulator spring column is pointing up
• arrow on the ratio regulator points in the direction of
gas flow
• integral fuel orifice and o-rings
are reinstalled
• the same straight run of pipe
remains between
the ratio regulator and the burner.
■
Do not attempt to redirect piping by removing the
inner circle bolts
. Internal burner parts will be
damaged.
Figure 3.6. Burner Piping
■
Do not alter the bypass regulator. The NFPA
requires that the bypass regulator
be
appropriately vented and protected.
■
For applications in which the Winnox is operating
indoors, a vent limiting device is installed in the
bypass regulator.
■
For applications in which the Winnox is operating
outdoors, an insect/rain protector is installed in
the bypass regulator.
Supply Piping
Inlet pressure to the ratio regulator must stay within
specified limits. Refer to the appropriate Winnox
datasheet, series 111.
• Locate the valve train close to the burner. The gas
must reach the burner during the fixed trial for
ignition period.
• Sufficiently size the shut off valve in the valve train.
• Make sure piping is large enough to accommodate
flow required to meet burner input.
• Minimize piping elbows.
• Install fuel flow measurement device
upstream
from the burner inlet.
• If necessary to maintain inlet pressures to the
burner (see datasheet for your burner), install a gas
pressure regulator
upstream of the burner inlet
and downstream of the valve train and fuel
measurement device
.
Figure 3.7. Supply Piping
Pipe Connections
Installation of a pipe union in the gas line is recommended
to simplify burner removal.
Use of flexible pipe is optional.
NOTE:
Flexible pipe causes higher pressure drops than
standard pipe. Consider this when sizing your gas lines.
CAUTION
CAUTION
Main gas
shut-off
valve train