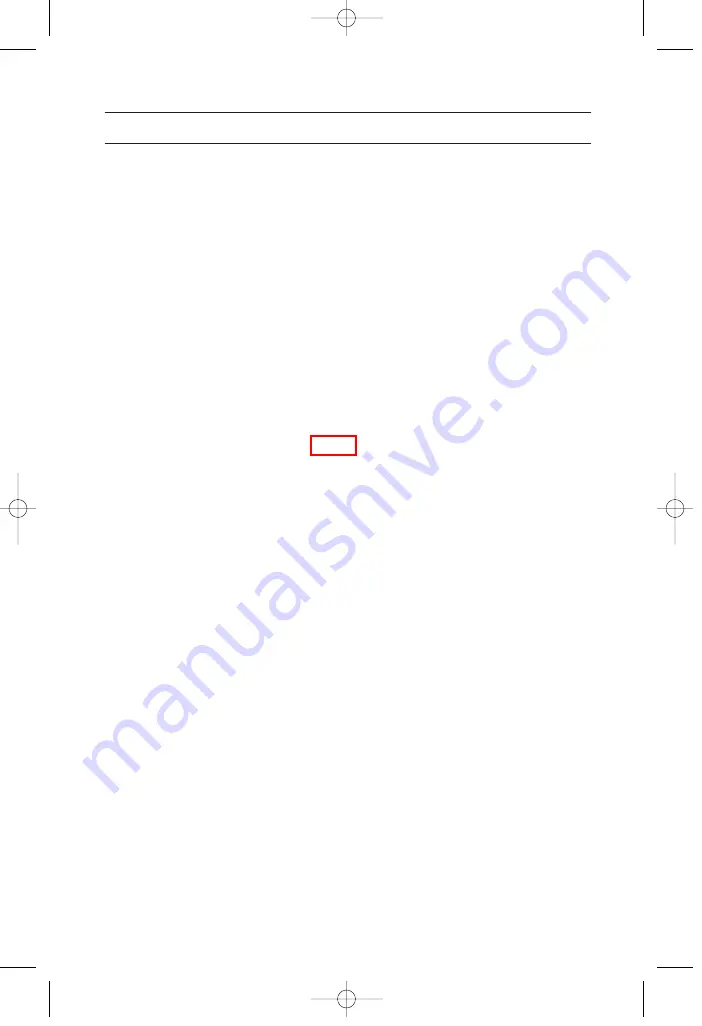
4
safety reasons. You should never touch a sump pump or discharge piping while the
pump is connected to electrical power and water is present. The pump should be
disconnected from the electrical source before handling in all cases.
Discharge Piping Installation
To assure the maximum performance from your sump pump, the discharge pipe size
and piping fittings should not be smaller than the discharge port of the pump. Smaller
pipe will add to friction losses and reduce the capacity of the pump. Normally accepted
materials are galvanized pipe, rigid plastic pipe or acceptable flexible pipe or hose. A piece
of flexible hose between the pump discharge and the discharge piping will provide for ease
in alignment, reduce vibration and noise, and will act as a union when it is necessary to
remove the pump. Where the discharge pipe is long, a check valve is often employed to
prevent the water from flowing back into the sump when the pump turns off. If the discharge
is directed into a sanitary sewer, a suitable anti-siphon device or a free flow check valve
should be inserted in the line to prevent backflow into the pit. Sump pumps are not
designed to handle
raw
sewage (see page 9, Septic Tank Installation). Do not attempt
to adapt one for this type of application. A sewage ejector pump especially designed to
handle solids must be used.
Pump Installation
When the sump, electrical and discharge plumbing installation is complete and ready
for the pump, clean all solid debris from the pit. Complete the plumbing connection to
the pump and then plug the pump into the electrical outlet. A few extra minutes to test
the sump pump installation are now in order. Fill the sump with water, note the turn on
and turn off level of the pump, and the pumping cycle. This will allow you to calculate
the approximate discharge flow of the pump system. If everything is operating properly,
install the sump cover.
Pump Selection
The pump should be of sufficient capacity and head to satisfy anticipated use require-
ments.
Basement perimeter water intrusion varies by area and region. Typically a 1/3 HP or 1/2
HP DRAINAGE PUMP WILL EVACUATE MOST HOME SUMP PITS.
Commercial and industrial drainage applications require that calculations of pumping
volume and pumping head be performed to determine the proper size pump is applied.
NOTE:
Pumping volume may vary seasonally due to rainfall and area run-off.
General Application Information
(cont.)
0204 HONDA WSP manual.qxd 3/24/2004 2:14 PM Page 6