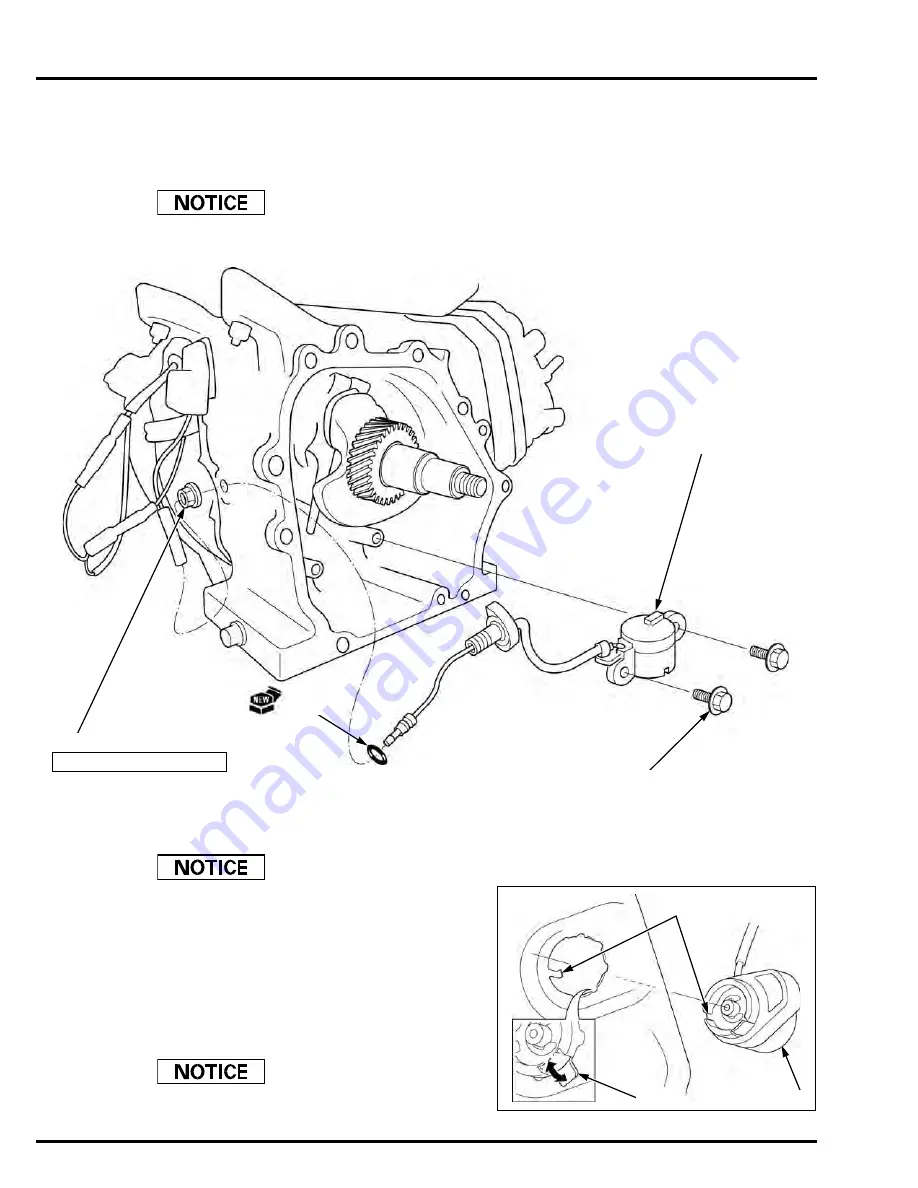
8-6
dummyhead
dummyhead
IGNITION SYSTEM
WB20XT2•WB30XT2
OIL LEVEL SWITCH
REMOVAL/INSTALLATION
Disconnect the
Oil Alert
unit connector.
Remove the camshaft (page 13-4).
Take care not to drop the valve lifter.
ENGINE STOP SWITCH
REMOVAL/INSTALLATION
Remove the engine stop switch only if necessary for
engine stop switch or fan cover replacement.
Remove the fan cover (page 5-2).
Straighten the tab (1) of the engine stop switch (2) and
remove the engine stop switch.
Install the engine stop switch to the fan cover, aligning
its groove with the boss of the fan cover.
Bend the tab until it is fully seated on the fan cover so
the engine stop switch is held.
The tab is used for ground terminal.
Install the fan cover (page 5-2).
OIL LEVEL SWITCH
BOLT (6 x 12 mm) (2)
O-RING
NUT (10 mm)
10 N·m (1.0 kgf·m, 7 lbf·ft)
(2)
(1)
Align
Summary of Contents for WB20XT2
Page 15: ...MEMO dummyhead dummyhead...
Page 47: ...MEMO dummyhead dummyhead...
Page 48: ...5 1 5 dummytext 5 COVER FAN COVER REMOVAL INSTALLATION 5 2...
Page 95: ...MEMO dummyhead dummyhead...
Page 96: ...11 1 11 dummytext 11 ENGINE REMOVAL INSTALLATION ENGINE REMOVAL INSTALLATION 11 2...
Page 99: ...MEMO dummyhead dummyhead...
Page 111: ...MEMO dummyhead dummyhead...
Page 129: ...MEMO dummyhead dummyhead...
Page 130: ...15 1 15 dummytext 15 WIRING DIAGRAM WIRING DIAGRAM 15 2...