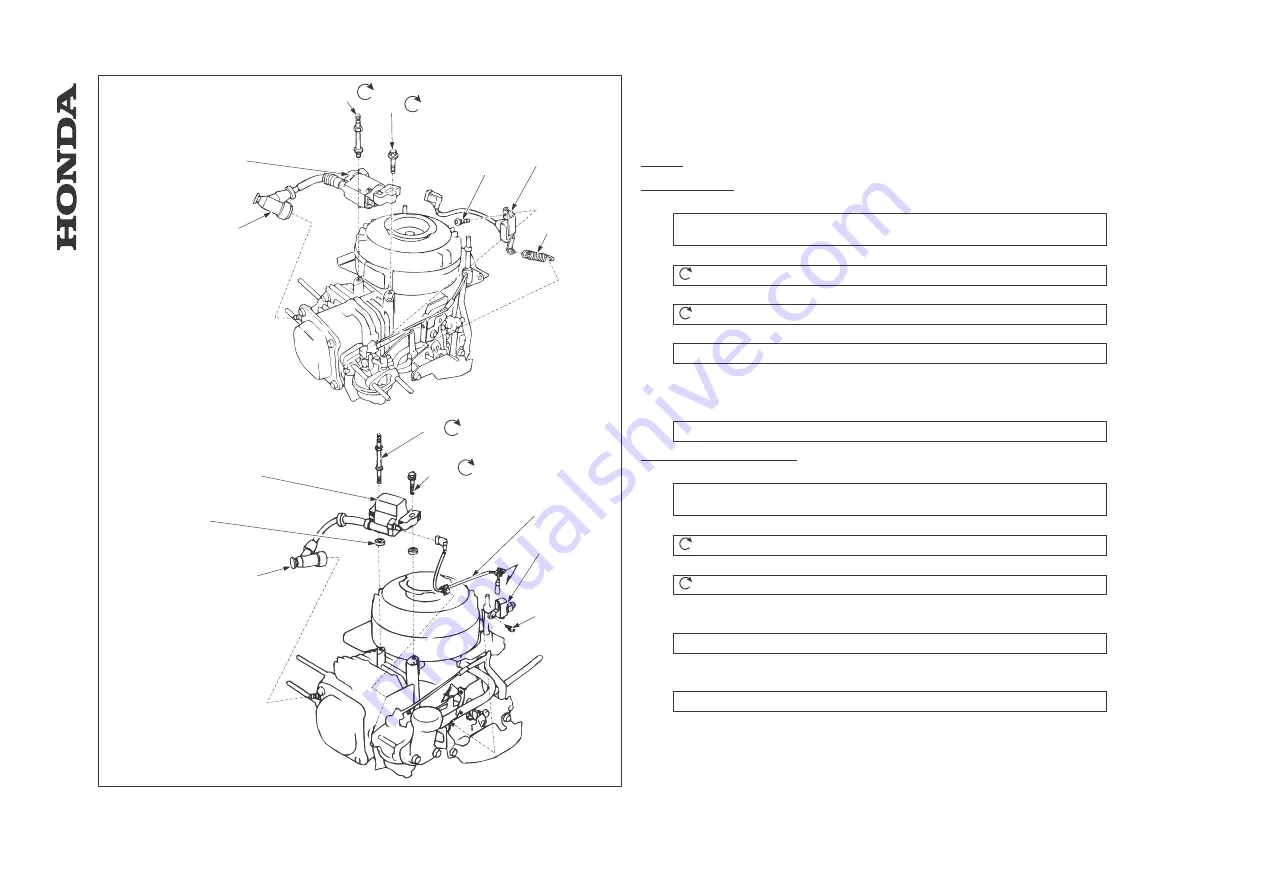
8.
IGNITION COIL / CONTROL ARM / CARBURETOR
8.1 Ignition coil / Engine stop switch
a.
Removal / Installation
NOTE:
It is not necessary to remove the engine.
HRD535/K1/K2
[1]
IGNITION COIL
INSPECTION:
ch. 8.1b
ADJUSTMENT:
ch. 8.1c
[2]
FUEL TANK STUD BOLT
TIGHTNING TORQUE:
10 N.m
[3]
SCREW, 6 x 25 mm
TIGHTNING TORQUE:
10 N.m
[4]
ENGINE STOP SWITCH (without starter motor model only)
INSPECTION:
ch. 8.1b
[5]
PAN SCREW, 4 x 8 mm
[6]
SWITCH SPRING
[7]
SPARK PLUG CAP
INSPECTION:
ch. 8.1b
HRA536 - HRD536/K1/K2
[8]
IGNITION COIL
INSPECTION:
ch. 8.1b
ADJUSTMENT:
ch. 8.1c
[9]
FUEL TANK STUD BOLT
TIGHTNING TORQUE:
10 N.m
[10]
SCREW, 6 x 28 mm
TIGHTNING TORQUE:
10 N.m
[11]
ENGINE STOP SWITCH WIRE (without starter motor model only)
[12]
ENGINE STOP SWITCH (without starter motor model only)
INSPECTION:
ch. 8.1b
[13]
PAN SCREW, 4 x 8 mm
[14]
SPARK PLUG CAP
INSPECTION:
ch. 8.1b
[15]
SPACER (2)
- 52 -
HRA536 - HRD535 - HRD536
[1]
[2]
[3]
[4]
[5]
[6]
[7]
[8]
[9]
[10]
[11]
[12]
[13]
[14]
[15]
HRD535/K1/K2
HRA536
HRD536/K1/K2
10
10
10
10
- IGNITION COIL / CONTROL ARM / CARBURETOR