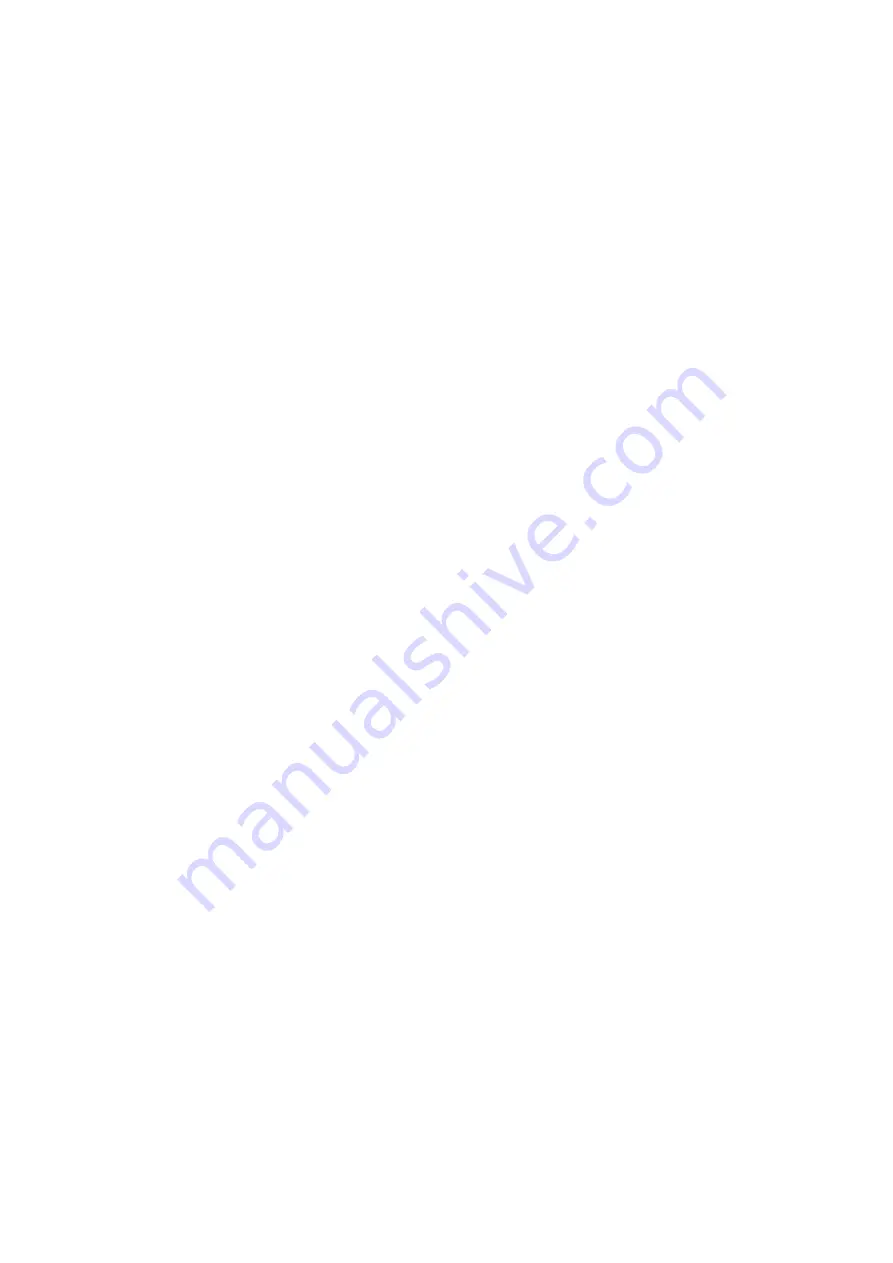
38 | EngliSH
Oils and lubricants must not be mixed. Use only the
manufacturer‘s original parts.
A trial run or functional test of the machine may only
take place in accordance with the general operating
conditions!
Type of oil:
Biodegradable HOMA ATOX. Used oil is to be
disposed of correctly.
When white oil is used, the following is to be heeded:
Only media from
•
the same manufacturer may be used for refilling and/
or filling from new.
•
Before being operated with white oil, machines that
have previously been operated with other media
must first be thoroughly cleaned.
6.2. Maintenance intervals
Before commissioning or after lengthy storage:
•
Testing insulation resistance
•
Level checks on sealing space/chamber
•
Slide ring seal is to be checked for damage.
Monthly:
•
Checking current consumption and voltage
•
Checking the switchgear used for temperature sen-
sor, sealing chamber control etc.
Semi-annually:
•
visual check on the power supply cable
•
visual check on the cable support and the cable-ten-
sioning system.
•
visual check on accessories,
•
e.g. suspension arrangement, hoists etc.
1,000 operating hours or after every six months, whi-
chever is earlier:
•
Monitoring the current consumption and voltage
•
Checking the used relays for posistors, sealing room
monitor, etc.
•
Visual inspection of the power supply cable
•
Visual inspection of the cable holder and the cable
bracing
•
Visual inspection of accessories, e.g. the suspension
device and hoisting gears
3,000 hours of operation:
•
Visual check on pumps with oil barrier chamber
•
Visual check on pumps without oil barrier chamber
8,000 hours of operation or after two years at the latest:
•
Testing insulation resistance
•
Exchanging operating service fluids sealing space/
chamber
•
Checking and if appropriate, repairing the coating
•
Functional test on all safety- and monitoring systems.
15,000 hours of operation or after two years at the
latest:
•
General overhaul at the works
When used in seriously abrasive and/or aggressive media,
the maintenance intervals are shortened.
6.3. Maintenance tasks
Checking current consumption and voltage
Current consumption and voltage on all 3 phases are to
be checked regularly. In normal operation, these remain
constant. Slight fluctuations depend on the nature of the
conveyed medium. Observing current consumption en-
ables damage and/or malfunctions of blade wheel/propel-
ler, bearings and/or motor to be detected and eliminated
at an early stage.
This can largely prevent greater consequential damage
and reduce the risk of a total failure.
Checking the switchgear used for temperature sensor,
sealing chamber control etc.
Check the switchgear used for faultless function.
Defective equipment must be exchanged immediate-
ly, for it does not guarantee protection for the machine
. Information about testing procedure is to be strictly obeyed
(operating instructions for the respective switchgear).
Testing insulation resistance
The power supply cable must be disconnected for the
insulation resistance to be checked. The resistance can
then be measured with an insulation tester (the measure-
ment voltage is 1000 volts DC).
The following values must be achieved:
On first being taken into use, the insulation resistance
must be at least 20 M
Ω
. In further measurements, the
value must be greater than 2 M
Ω
. Insulation resistance
too low: Moisture may have penetrated the cable and/or
motor.
Do not connect machine again but consult the manu-
facturer!
Visual check on the power supply cable
The power supply cable must be investigated for bubbles,
cracks, scratches, chafe marks and/or pinching points. If
damage is discovered, the damaged power supply cable
must be exchanged immediately.
Only the manufacturer or an authorized or certified
service workshop may exchange cables. The machine
may not be put into operation again until the damage
has been correctly eliminated!
Visual check on the cable support (snap hook) and ca-
ble-tensioning system)
When the machine is used in basins or shafts, the hoisting
slings / cable support (snap hook) and the cable-tensioning
system are exposed to constant wear. Regular tests are
necessary in order to prevent hoisting slings / cable sup-
port (snap hook) and/or cable-tensioning system wearing
out totally and the power cable being damaged.
The hoisting slings / cable support (snap hook) and the
cable-tensioning system are to be exchanged immedi-
ately if they display minor indications of wear!
Visual check on accessories
Accessories such as suspension arrangements, hoists
etc. are to be checked for correct seating. Loose and/or
defective accessories are to be repaired or exchanged im-
mediately.