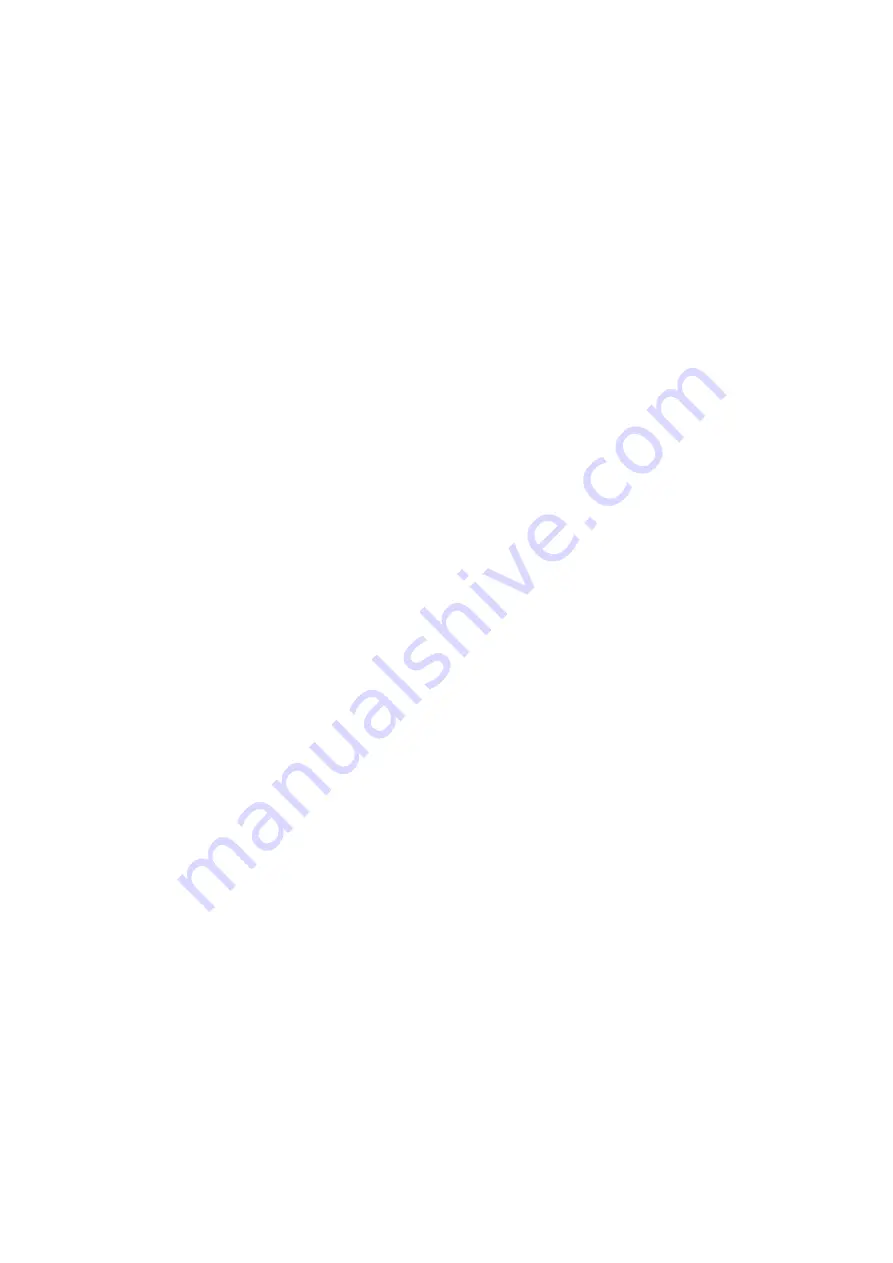
18 | ENGLISH
Checking the used relays for posistors, oil chamber
monitors, etc.
Check the relays used are functioning fault-free. Defective
devices must be immediately replaced, because these
cannot ensure safe operation of the machine. The test pro-
cedure details should be followed closely (in the operating
instructions for each relay).
Checking the insulation resistance
To check the insulation resistance, the power supply ca-
ble must be disconnected. The resistance can then be
measured with an insulation tester (measuring voltage =
1000V DC).
The following values may not be exceeded:
• The insulation resistance may not be below 20 MΩ
during initial operation. For all further measurements
the value must be greater than 2 MΩ.
• Insulation resistance too low: Moisture may have
penetrated the cable and/or the motor.
Do not connect the machine, consult manufacturer!
Visual inspection of power supply cables
The power supply line must be examined for bubbles,
cracks, scratches, chafed areas and/or crushed sections.
If damage is found, the power cable must be exchanged
immediately.
The cables may only be changed by the manufactur-
er or an authorized/certified service workshop. The
machine may not be used again until the damage has
been adequately rectified.
Visual examination of the cable holders (carabiners)
and the cable bracing
When the machine is used in basins or pits, the lifting
cables/cable holders (carabiners) and the cable bracing
are subject to constant wear. Regular inspections are nec-
essary in order to prevent the lifting cables/cable holders
(carabiners) and/or cable bracing from wearing out and to
prevent the electricity cable from being damaged.
The lifting cables/cable holders (carabiners) and the
cable bracing are to be immediately replaced if any
signs of wear appear
.
Visual inspection of accessories
Inspect accessories such as suspension units and hoist-
ing gear to check whether they are secured in a stable
manner. Loose and/or defective accessories should be re-
paired immediately or replaced.
Oi
l Level check in Seal Chamber
Visual Inspection of Oil Chamber:
Oil Level
Please take the precise filling quantity from the spare
parts list or contact the manufacturer with the pump serial
number.
Oil Condition
The condition of the mechanical seals can be visually in-
spected as follows: Put the pump in horizontal position, so
that the oil chamber drain plug is on top. Remove the drain
plug and take out a small quantity of oil. The oil becomes
greyish white like milk if it contains water. This may be the
result of defective shaft seals. In this case the condition
of the shaft seals should be checked by a HOMA Service
shop. Oil type: Mineral Oil
Used oil has to be disposed according to the existing envi-
ronmental rules and regulations.
Functional inspection of safety and control devices
Monitoring devices are temperature sensors in the motor,
oil chamber monitors, motor protection relays, overvolt-
age relays, etc. Motor protection and overvoltage relays
and other trip elements can generally be triggered manu-
ally for test purposes. To inspect the oil chamber monitor
or the temperature sensor, the machine must be cooled
to ambient temperature and the electrical supply cable of
the monitoring device in the switch cabinet must be dis-
connected. The monitoring device is then tested with an
ohmmeter.
The following values should be measured:
Bi-metal sensor:
Value = “0” - throughput
PTC sensor:
A PTC sensor has a cold resistance of be-
tween 20 and 100 Ω. For 3 sensors in series this would
result in a value of between 60 and 300 Ω.
PT 100 sensor:
PT 100 sensors have a value of 100ohms
at 0°C. Between 32°F and 212°F this value increases by
0.214 Ω per 1°F. PT 20 sensors have a value of 107.7 Ω at
68°C.
Moisture sensor:
This value must approach infinity. If
there is a low value, there may be water in the oil.
Also observe the instructions of the optionally available
evaluation relay.
In the case of larger deviations, please
consult the manufacturer.
Please consult the appropri-
ate operating manual for details on inspecting the safety
and monitoring devices on the auxiliary lifting gear.
General overhaul
During this the bearings, shaft seals, O rings and power
supply cables are inspected and replaced as required in
addition to normal maintenance work. This work may only
be conducted by the manufacturer or an authorized ser-
vice workshop.
Changing the oil
The drained oil must be checked for dirt and water con-
tent. If the oil is very dirty and shows water intrusion, it
must be changed again after four weeks. If there is again
water in the oil then, it seems likely that a seal is defec-
tive. In this case, please consult the manufacturer. If an oil
chamber or leakage monitoring system is being used, the
display will light up again within
four weeks
of changing
the oil if a seal is defective.
The general procedure for changing oil is as follows:
Switch off the machine, let it cool down, disconnect it
from the power supply (have this done by an electri-
cian), lock out tag out the control panel, clean it and
place it vertically on a solid base. Warm or hot oil may
be pressurized. The leaking oil may cause burns. For
that reason, let the machine cool down to ambient
temperature before you touch it.