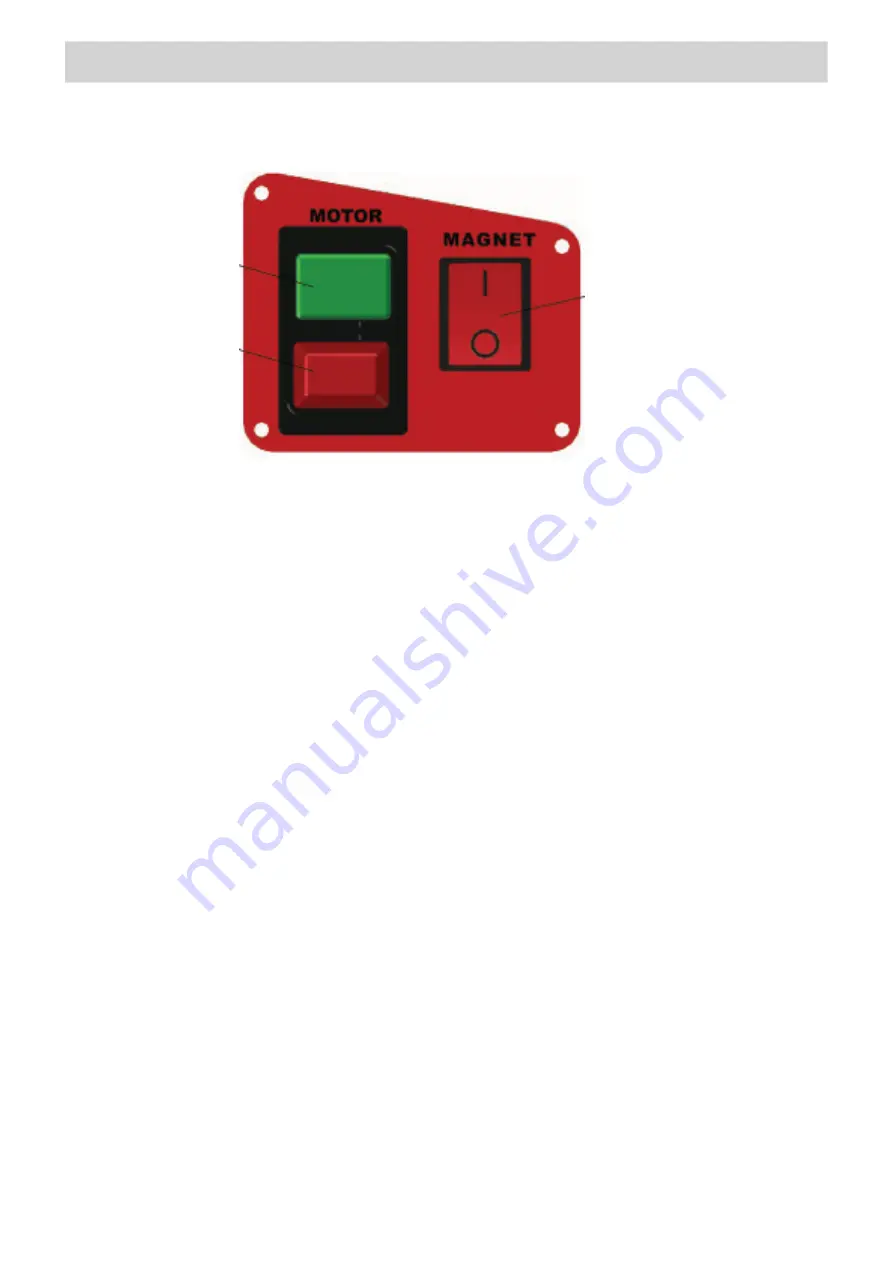
6
GENERAL INFORMATION
The PRO 35 AUTO is supplied in a metal box with complete standard equipment.
The included equipment consists of:
• 1x Drilling machine
• 1x Metal box
• 2x Spoke handle
• 1x Cooling system bottle
• 1x Chip guard
• 1x Safety strap
• 1x 4mm hex wrench
• 1x Operator’s manual
Figure 2.
Control panel design
1.4. Equipemnt included
Motor START button
Motor STOP button
Electromagnetic
base ON/OFF switch
2. Safety instructions
1. Before beginning, read this Operator’s Manual and complete proper occupational health
and safety training.
2. The machine must be used only in applications specified in this Operator’s Manual.
3. The machine must be complete and all parts must be genuine and fully operational.
4. The electrical supply specifications must conform to those specified on the rating plate.
5. The machine must be plugged into a properly grounded (earthed) socket-outlet. The
electrical supply must be protected with a 16 A fuse for 230 V. When used on building
sites, supply the machine through an isolation transformer made with class II protection
only.
6. Never carry the machine by the cord or pull it to disconnect the plug from the power
outlet as this may damage the power cord and result in electric shock.
7. Transport and position the machine using the carrying handle, with the magnet switch
set to position ‘O’ (off).
Summary of Contents for Pro 35 Auto
Page 15: ...15 NOTES...