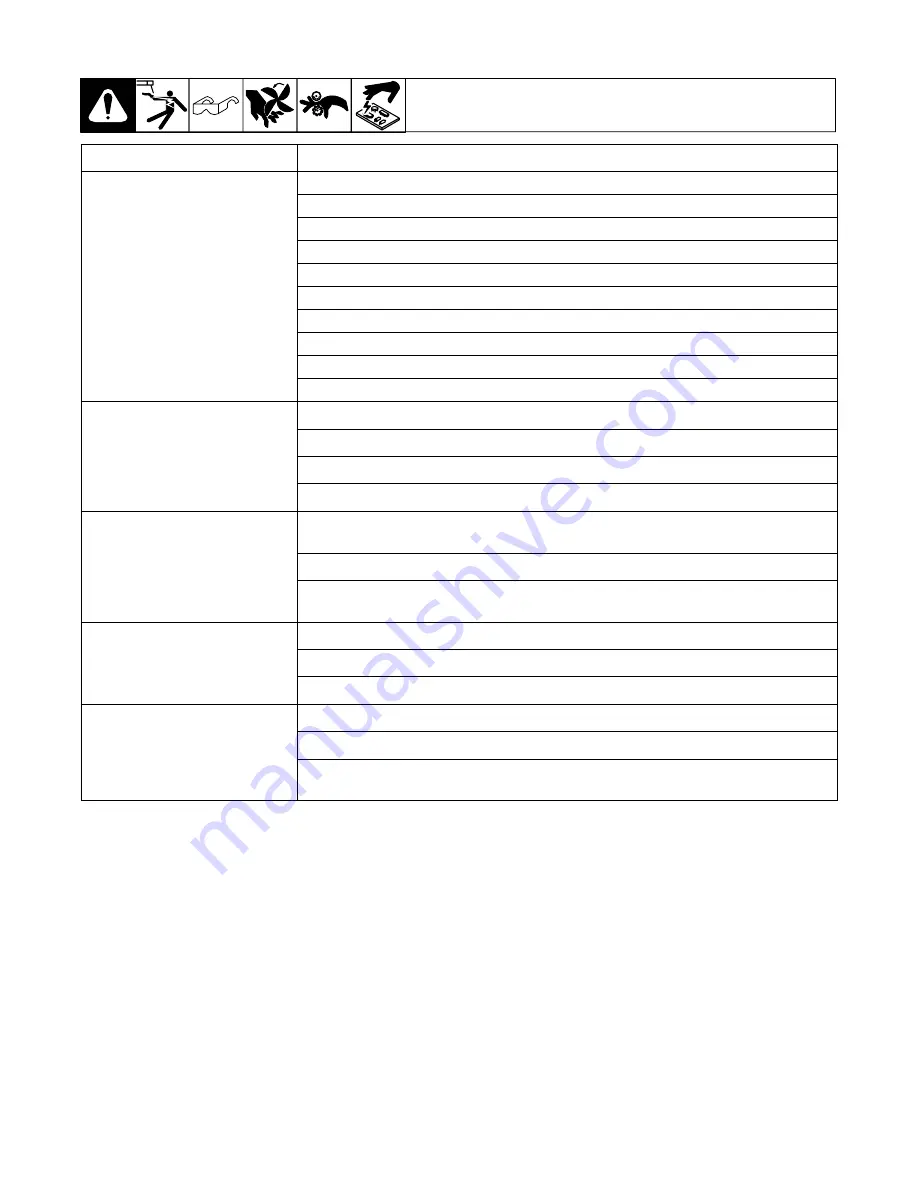
OM-923 Page 24
6-8. Troubleshooting Table
Trouble
Remedy
Electrode wire feeding stops during
welding
Straighten gun cable and/or replace damaged parts.
welding.
Adjust drive roll pressure (see Section 4-7).
Change to proper drive roll groove (see Section 6-4).
Readjust hub tension (see Section 4-4).
Replace contact tip if blocked (see Section 6-5).
Clean or replace wire inlet guide or liner if dirty or plugged (see Section 6-4).
Replace drive roll or pressure bearing if worn or slipping (see Section 6-4).
Check and clear any restrictions at drive assembly and liner (see Section 4-7).
Release gun trigger and allow gun and motor protection circuitry to reset.
Have nearest Factory Authorized Service Agent check drive motor.
No weld output; wire does not feed; fan
does not run
Secure power cord plug in receptacle (see Section 4-5).
does not run.
Replace building line fuse or reset circuit breaker if open.
Place Power switch in On position (see Section 5-1).
Reset welding power source supplementary protector if open.
No weld output; wire does not feed; fan
motor continues to run.
Thermostat TP1 open (overheating). Allow fan to run with gun trigger switch off; thermostat resets when
unit has cooled (see Section 3-2).
Be sure that Material Thickness Selector switch is not set between ranges (see Section 5-1).
Disassemble torch handle and check trigger switch lead connections, tighten or reconnect any loose
connections.
No weld output; wire feeds.
Connect work clamp to get good metal to metal contact.
Check cable connection at work clamp and tighten hardware, if necessary (see Section 4-1).
Replace contact tip (see Section 6-5).
Low weld output.
Connect unit to proper input voltage or check for low line voltage.
Place Material Thickness Selector switch in correct setting (see Section 5-1).
If using an extension cord, check that wire size and length is the proper size for power rating of welding
power source (see Section 3-1).