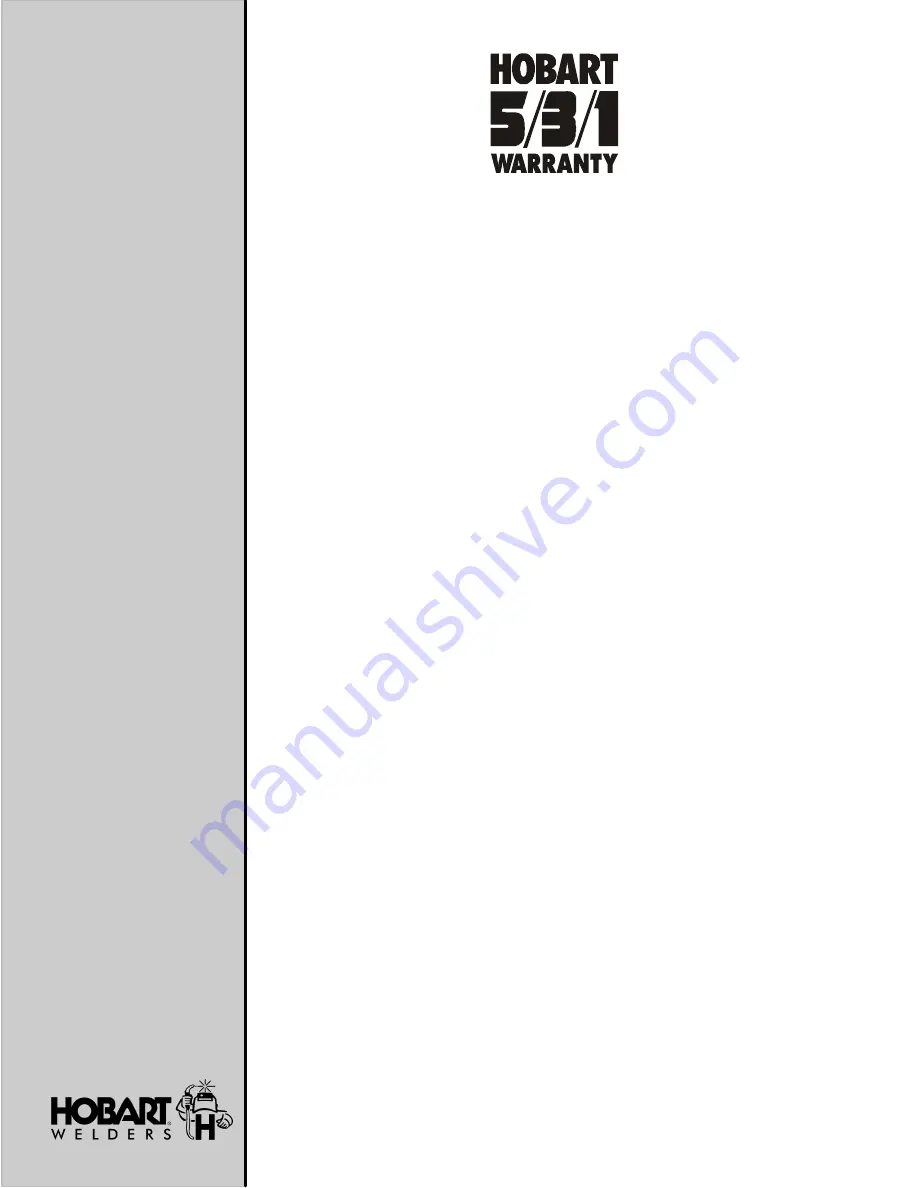
Warranty Questions?
Call
1-877-HOBART1
for your local
Hobart distributor.
hobart retail 4/00
Service
You always get the fast,
reliable response you
need. Most replacement
parts can be in your
hands in 24 hours.
Support
Need fast answers to the
tough welding questions?
Contact your distributor or
call 1-800-332-3281. The
expertise of the distributor
and Hobart is there to
help you, every step of
the way.
Effective October 1, 1999
5/3/1 WARRANTY applies to all Handler 135 and 175 models, Airforce 250, 250A, and 375
models, and Champion 10,000 models.This warranty also applies to the Beta-Mig 1800, Champ
1435, 2060, 8500 models, Ironman 250, Stickmate models, Tigmate models, and HSW-15 and
HSW-25 spot welder models effective with Serial No. KK200262 and newer.
This limited warranty supersedes all previous Hobart warranties and is exclusive with
no other guarantees or warranties expressed or implied.
Hobart products are serviced by Hobart or Miller Authorized Service Agencies.
LIMITED WARRANTY – Subject to the terms and conditions
below, Hobart/Miller Electric Mfg. Co., Appleton, Wisconsin,
warrants to its original retail purchaser that new Hobart
equipment sold after the effective date of this limited warranty
is free of defects in material and workmanship at the time it is
shipped by Hobart. THIS WARRANTY IS EXPRESSLY IN
LIEU OF ALL OTHER WARRANTIES, EXPRESS OR
IMPLIED, INCLUDING THE WARRANTIES OF
MERCHANTABILITY AND FITNESS.
Within the warranty periods listed below, Hobart/Miller will
repair or replace any warranted parts or components that fail
due to such defects in material or workmanship. Hobart/Miller
must be notified in writing within thirty (30) days of such defect
or failure, at which time Hobart/Miller will provide instructions
on the warranty claim procedures to be followed.
Hobart/Miller shall honor warranty claims on warranted
equipment listed below in the event of such a failure within the
warranty time periods. All warranty time periods start on the
date that the equipment was delivered to the original retail
purchaser, or one year after the equipment is sent to a North
American distributor or eighteen months after the equipment
is sent to an International distributor.
1.
5 Years — Parts and Labor
*
Original Main Power Rectifiers
*
Transformers
*
Stabilizers
*
Reactors
*
Rotors, Stators and Brushes
2.
3 Years — Parts and Labor
*
Drive Systems
*
PC Boards
*
Idle Module
*
Solenoid Valves
*
Switches and Controls
*
Spot Welder Transformer
3.
1 Year — Parts and Labor (90 days for industrial use)
*
Motor-Driven Guns
*
MIG Guns/TIG Torches
*
Relays
*
Contactors
*
Regulators
*
Water Coolant Systems
*
HF Units
*
Running Gear/Trailers
*
Plasma Cutting Torches
*
Remote Controls
*
Replacement Parts (No labor)
*
Accessories
*
Field Options
(NOTE: Field options are covered
for the
remaining warranty period of the product they are
installed in, or for a minimum of one year —
whichever is greater.)
4.
Engines, batteries and tires are warranted separately by
the manufacturer.
Hobart’s 5/3/1 Limited Warranty shall not apply to:
1.
Consumable components such as contact tips,
cutting nozzles, slip rings, drive rolls, gas diffusers,
plasma torch tips and electrodes, weld cables, and
tongs and tips, or parts that fail due to normal wear.
2.
Items furnished by Hobart/Miller, but manufactured by
others, such as engines or trade accessories. These
items are covered by the manufacturer’s warranty, if any.
3.
Equipment that has been modified by any party other
than Hobart/Miller, or equipment that has been
improperly installed, improperly operated or misused
based upon industry standards, or equipment which has
not had reasonable and necessary maintenance, or
equipment which has been used for operation outside of
the specifications for the equipment.
HOBART PRODUCTS ARE INTENDED FOR PURCHASE
AND USE BY COMMERCIAL/INDUSTRIAL USERS AND
PERSONS TRAINED AND EXPERIENCED IN THE USE
AND MAINTENANCE OF WELDING EQUIPMENT.
In the event of a warranty claim covered by this warranty, the
exclusive remedies shall be, at Hobart’s/Miller’s option: (1)
repair; or (2) replacement; or, where authorized in writing by
Hobart/Miller in appropriate cases, (3) the reasonable cost of
repair or replacement at an authorized Hobart/Miller service
station; or (4) payment of or credit for the purchase price (less
reasonable depreciation based upon actual use) upon return
of the goods at customer’s risk and expense. Hobart’s/Miller’s
option of repair or replacement will be F.O.B., Factory at
Appleton, Wisconsin, or F.O.B. at a Hobart/Miller authorized
service facility as determined by Hobart/Miller. Therefore no
compensation or reimbursement for transportation costs of
any kind will be allowed.
TO THE EXTENT PERMITTED BY LAW, THE REMEDIES
PROVIDED HEREIN ARE THE SOLE AND EXCLUSIVE
REMEDIES. IN NO EVENT SHALL HOBART/MILLER BE
LIABLE FOR DIRECT, INDIRECT, SPECIAL, INCIDENTAL
OR CONSEQUENTIAL DAMAGES (INCLUDING LOSS OF
PROFIT), WHETHER BASED ON CONTRACT, TORT OR
ANY OTHER LEGAL THEORY.
ANY EXPRESS WARRANTY NOT PROVIDED HEREIN
AND ANY IMPLIED WARRANTY, GUARANTY OR
REPRESENTATION AS TO PERFORMANCE, AND ANY
REMEDY FOR BREACH OF CONTRACT TORT OR ANY
OTHER LEGAL THEORY WHICH, BUT FOR THIS
PROVISION, MIGHT ARISE BY IMPLICATION,
OPERATION OF LAW, CUSTOM OF TRADE OR COURSE
OF DEALING, INCLUDING ANY IMPLIED WARRANTY OF
MERCHANTABILITY OR FITNESS FOR PARTICULAR
PURPOSE, WITH RESPECT TO ANY AND ALL
EQUIPMENT FURNISHED BY HOBART/MILLER IS
EXCLUDED AND DISCLAIMED BY Hobart/Miller.
Some states in the U.S.A. do not allow limitations of how long
an implied warranty lasts, or the exclusion of incidental,
indirect, special or consequential damages, so the above
limitation or exclusion may not apply to you. This warranty
provides specific legal rights, and other rights may be
available, but may vary from state to state.
In Canada, legislation in some provinces provides for certain
additional warranties or remedies other than as stated herein,
and to the extent that they may not be waived, the limitations
and exclusions set out above may not apply. This Limited
Warranty provides specific legal rights, and other rights may
be available, but may vary from province to province.
Summary of Contents for AirForce 750
Page 4: ......
Page 26: ...OM 279 Page 22 194 148 Figure 5 2 Circuit Diagram For 230 460 575 Volt Models ...
Page 27: ...OM 279 Page 23 Notes ...
Page 31: ...OM 279 Page 27 Notes ...
Page 32: ...OM 279 Page 28 Notes ...
Page 33: ...Notes ...
Page 34: ...Notes ...