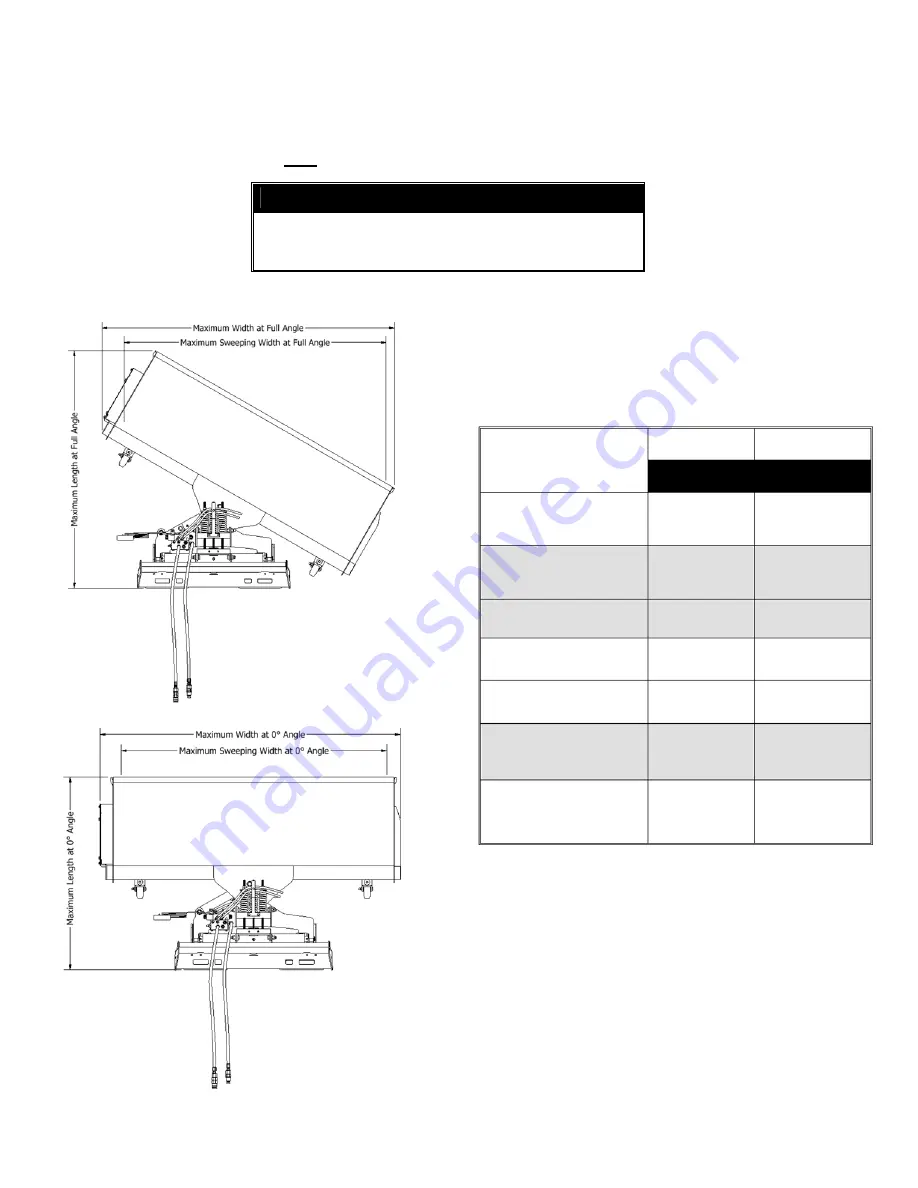
- 7 -
POWER UNIT SPECIFICATIONS
IMPORTANT
Exceeding any of the recommended power unit specifications
•
CAN
result in damage to your power unit and/or this product and
•
WILL
void all HLA warranties.
ATTACHMENT SPECIFICATIONS
LOADER SPECIFICATIONS
Minimum 12 gpm
Maximum 20 gpm
Maximum 3000 PSI
Model #
Mode l#
BR72 BR84
Approx. Weight
(lbs.)
955 lbs.
1070 lbs.
Max. Length at
0° Angle
57.5 inches
57.5 inches
Max. Width at
0° Angle
78 inches
90 inches
Max. Length at
Full Angle
67.5 inches
74 inches
Max. Width at
Full Angle
80 inches
90.5 inches
Sweeping Width at
0° Angle
67.5 inches
79.5 inches
Sweeping Width at
Full Angle
70.5 inches
81 inches