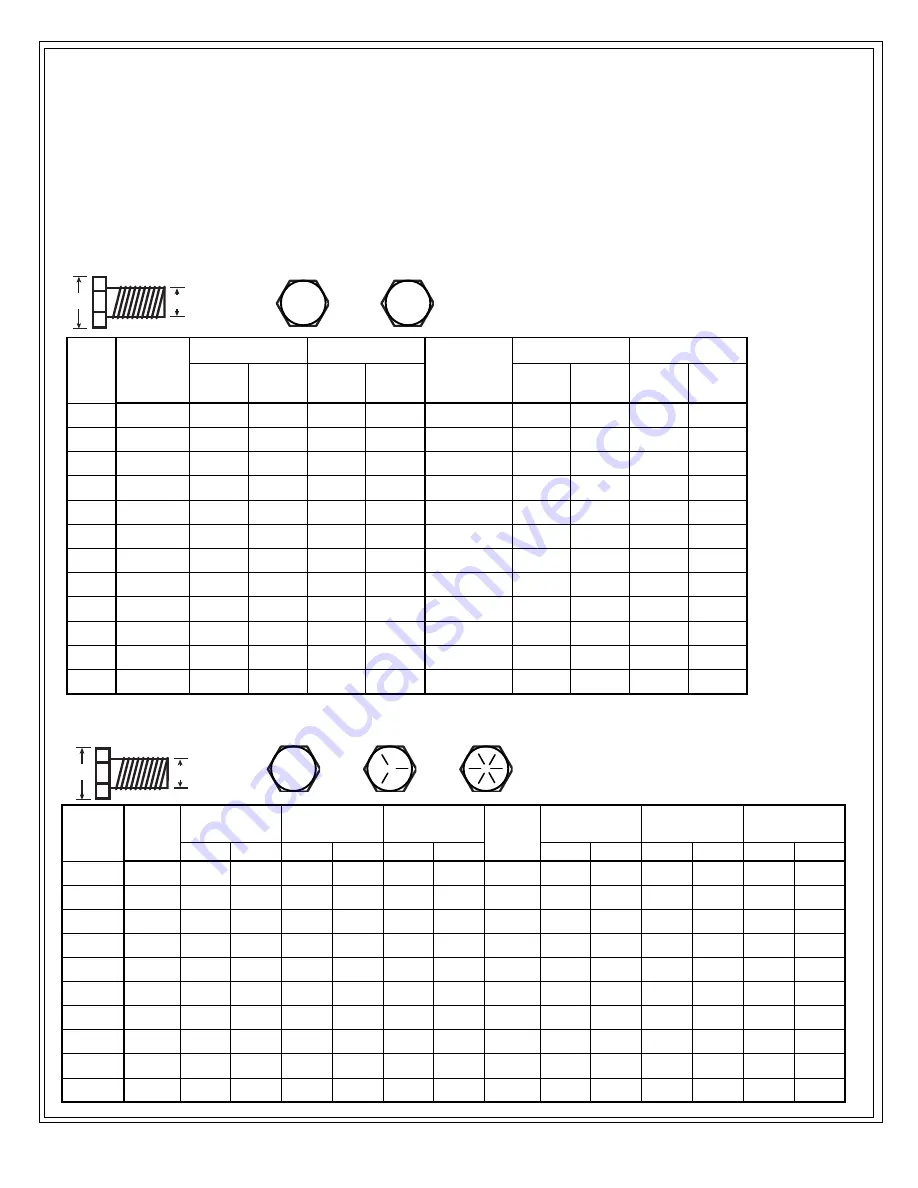
28
Bolt Torque Table
B
A
B
A
8.8
10.9
SAE 2
SAE 5
SAE 8
These table
s
are offered as the suggested maximum torque values for dry (not lubricated) threaded products and
are only a general guide.
Check tightness of bolts periodically, replace hardware with the same strength bolt.
Torque specification for bolts are identified by their head markings as shown.
See the “Wheel Torque Specification” page for wheel bolt /nut torque settings
METRIC TORQUE SPECIFICATIONS
SAE TORQUE SPECIFICATIONS
N-m
lbs-ft
N-m
lbs-ft
N-m
lbs-ft
N-m
lbs-ft
10 mm
6 x 0.75
---
---
---
---
6 x 1.0
11.3
8.3
16.5
12.2
13 mm
8 x 1.0
27
20
38
28
8 x 1.25
27.3
20.1
40.1
29.6
16 mm
10 x 1.25
52
38
73
54
10 x 1.5
54
40
49
36
18 mm
12 x 1.25
95
70
135
100
12.1.75
93
69
137
101
21 mm
14 x 1.5
150
111
210
155
14 x 2.0
148
109
218
161
24 mm
16 x 1.5
225
166
315
232
16 x 2.0
230
170
338
249
27 mm
18 x 1.5
325
240
460
339
18 x 2.5
329
243
469
346
30 mm
20 x 1.5
460
339
640
472
20 x 2.5
464
342
661
487
34 mm
22 x 1.5
610
450
860
634
22 x 2.5
634
468
904
667
36 mm
24 x 2.0
780
575
1100
811
24 x 3.0
798
588
1136
838
41 mm
27 x 3.0
---
---
---
---
27 x 3.0
1176
867
1674
1234
46 mm
30 x 2.0
---
---
---
---
30 x 3.0
1597
1178
2274
1677
Class 10.9
Class 8.8
Wrench
Size:
"A"
Thread Size:
"B"
Fine
Thread Size: "B"
Coarse
Class 10.9
Class 8.8
lbs-ft
.
N-m
lbs-ft
N-m
lbs-ft
N-m
lbs-ft
N-m
lbs-ft
N-m
lbs-ft
N-m
7/16”
1/4-28
6
8.1
10
13.6
14
19.0
1/4-20
5
6.8
8
10.8
12
16.3
1/2”
5/16-24
13
17.6
19
25.7
27
36.6
5/16-18
11
14.9
17
23.0
25
33.9
9/16”
3/8-24
23
31.2
35
47.4
49
66.4
3/8-16
20
27.1
31
42.0
44
59.6
5/8”
7/16-20
36
48.8
55
74.5
75
101.6
7/16-14
32
43.4
49
66.4
70
94.9
3/4”
1/2-20
55
74.5
85
115.2
120
162.6
1/2-13
49
66.4
75
101.6
107
145.0
13/16”
9/16-18
79
107.0
122
165.3
172
233.1
9/16-12
70
94.9
109
147.7
154
208.7
15/16”
5/8-18
110
149.1
170
230.4
240
325.2
5/8-11
97
131.4
150
203.3
212
287.3
1-1/8”
3/4-16
192
260.2
297
402.4
420
569.1
3/4-10
173
234.4
266
360.4
376
509.5
1-5/16”
7/8-14
184
249.3
474
642.3
668
905.1
7/8-9
166
224.9
429
581.3
606
821.1
1-1/2”
1.0-12
274
371.3
705
955.3
995
1348.2
1.0-8
250
338.8
644
872.6
909
1231.7
SAE 8
SAE 2
SAE 5
SAE 8
Wrench
Size:
"A"
Thread
Size: "B"
Fine
Thread
Size: "B"
Coarse
SAE 2
SAE 5
Summary of Contents for BK48LF
Page 2: ...2 Notes ...