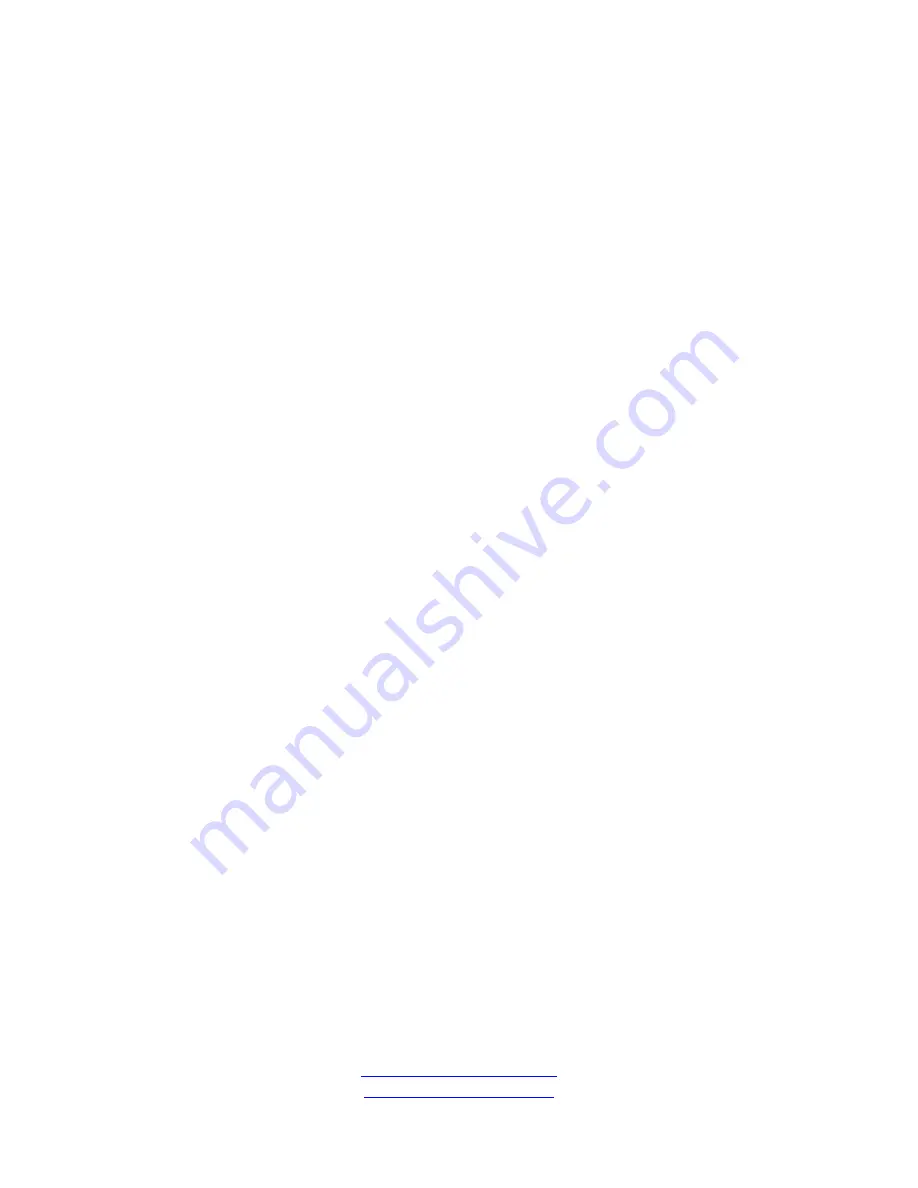
- 1 -
TABLE OF CONTENTS
HLA Attachments
8082 Rd 129
RR# 3
Listowel ON N4W 3G8
Canada
1-866-567-4162
www.horstwelding.com
Introduction, General Information, Serial Number .……… ………… 2
Owner and Operator and Safety Information …………………….. 3-6
Definitions of Safety Terms and Symbols, Accident Prevention
…….. 3
Safety Instructions
…………………………………………………. 4-5
Safety Signs
…………………………………………………………..
6
Power Unit Specifications ………………………………….…………. 7
Installation Instructions …………………………………………………7
Hydraulic Instructions ………………………………………………….. 7
Operation ………………………………………………………….….. 8-9
Maintenance ………………………………………………………….. 10
Service ……………………………………………………………..….. 10
Mounting Locations…...…………………………………………..….. 11
Parts Illustrations …………………………………………….…… 12-13
Grease Zerk Locations ………………………………………….…… 14
Selector Valve Diagram ……………………………………………… 14
Hydraulic Parts List ……………………………………………….….. 15
Hydraulic Plumbing …………………………………………………... 16
Specifications ……………………….…………………………….….. 17
Troubleshooting ………………………………….…………………… 18
Warranty Policy………………………………………….…………….. 19
Summary of Contents for BIG ARM BH600
Page 1: ...OPERATOR S MANUAL BH600 Manual Number BH600 08_1 August 2008 ...
Page 2: ......
Page 14: ... 12 ...
Page 15: ... 13 ...
Page 16: ... 14 ...
Page 17: ... 15 ...