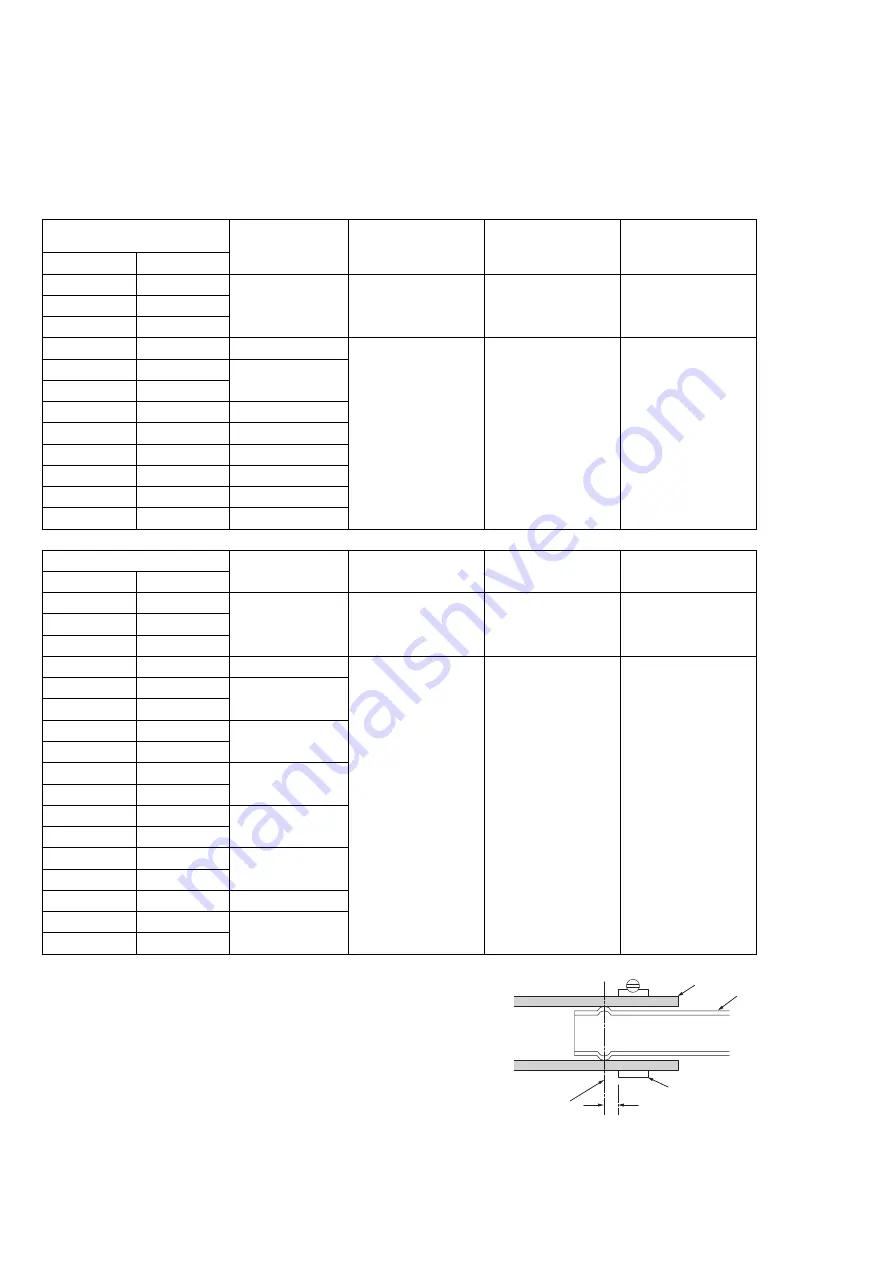
00-16
General Information
Outline
Hose band tightening torque
To connect the hose to the pipe, tighten the hose band
at the following position:
Low pressure hose
(heat resisting hose)
Hose band
Tightening torque
(N-m)
Tightening torque
(kgf-cm)
Tightening torque
(lb-ft)
Inner dia. (mm) Outer dia. (mm)
6.3
16.5
69002-02200
1.6
16
1.2
7.9
18.5
9.5
20.5
12.7
24.5
69002-02700
4
40
2.9
15.9
29.9
69002-03100
19.0
30.0
25.4
38.0
69002-04400
31.8
45.8
69002-05200
38.1
52.1
69002-05700
50.8
67.8
69002-07100
60.5
76.0
69002-08200
75.5
93.0
69002-09500
Low pressure hose
Hose band
Tightening torque
(N-m)
Tightening torque
(kgf-cm)
Tightening torque
(lb-ft)
Inner dia. (mm) Outer dia. (mm)
6
16.5
69002-02200
1.6
16
1.2
8
18.5
9
20.5
9
22.0
69002-02300
4
40
2.9
12
24.5
69002-02700
12
26.0
15
29.0
69002-03100
15
30.5
19
32.0
69002-03800
19
34.0
25
39.5
69002-04400
25
41.5
32
46.0
69002-05200
32
48.0
38
54.0
69002-05700
50
70.5
69002-07600
50
73.0
70ZV00003
10~20 mm
Hose
Pipe
Center of pipe
protrusion
Hose band
Summary of Contents for ZW 550-G
Page 1: ...Find manuals at https best manuals com ...
Page 2: ...Find manuals at https best manuals com ...
Page 17: ...00 1 General Information General Information How to Use Manual 00 2 Outline 00 4 ...
Page 50: ...This as a preview PDF file from best manuals com Download full PDF manual at best manuals com ...