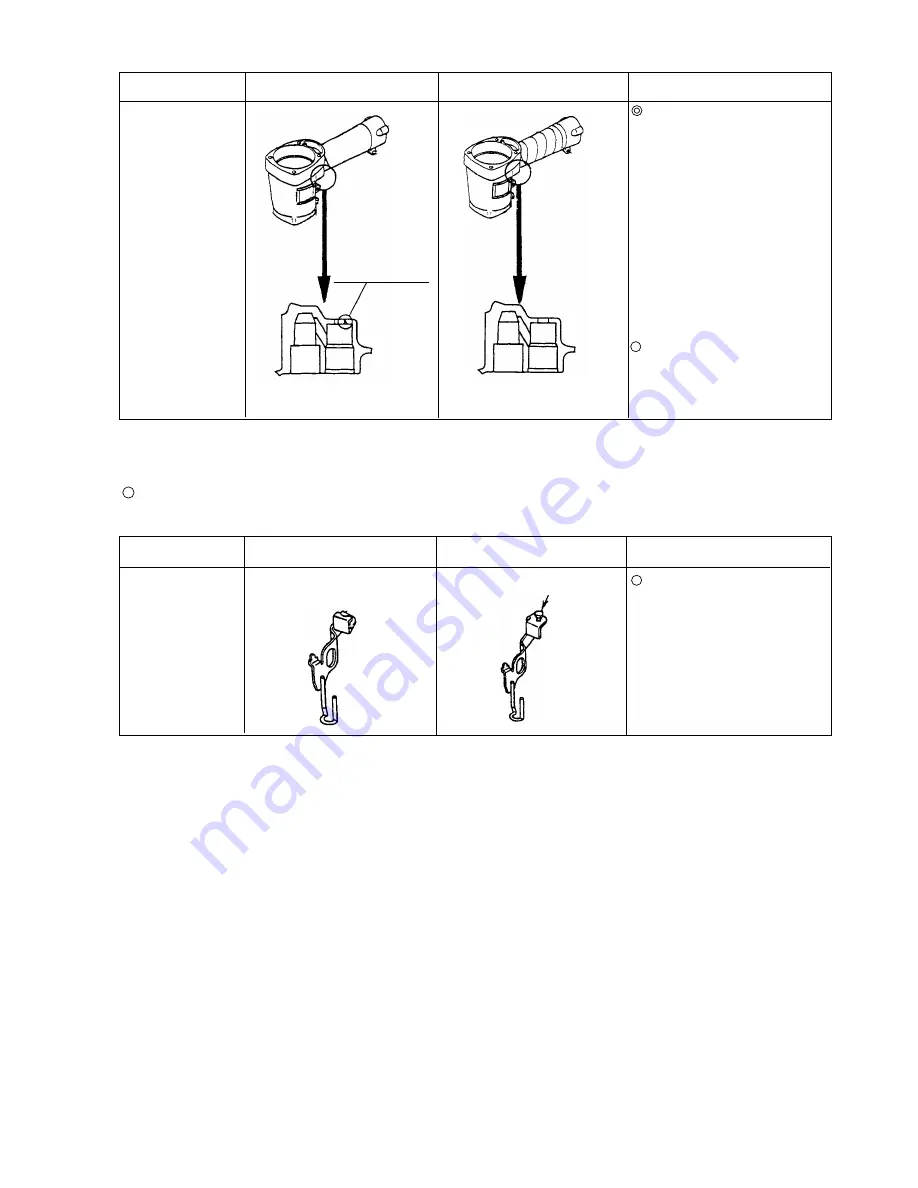
--- 11 ---
Part
Air escape groove
Caution
Do not mount the body ass'y
for the Model NT 65A2 to the
Model NT 65A3. Otherwise,
air may be remained in the
valve if the air hose is
removed with the trigger
pulled when selecting the
single actuation (single
sequential actuation)
mechanism. (It is prohibited
to remove the air hose with
the trigger pulled and it is
also specified in the Handling
Instructions.)
There is no problem in
mounting the body ass'y for
the Model NT 65A3 to the
Model NT 65A2.
NT 65A3
NT 65A2
Body Ass'y [19]
(2) Driving section
Parts that were changed for the Model NT 65A3 and not interchangeable with those of the Model NT 65A2
though they are similar to those of the Model NT 65A2
Pushing Lever [65]
Part
NT 65A3
NT 65A2
Caution
Without safety bolt
Safety bolt
The pushing lever for the
Model NT 65A3 is not
interchangeable with that of
the Model NT 65A2 because
the adjustment method is
different (safety bolt is not
provided).
The parts of the output section except the above are common to those of the Model NT 65A2.
The parts of the driving section except the above are common to those of the Model NT 65A2.
Summary of Contents for NT 65A3
Page 45: ......