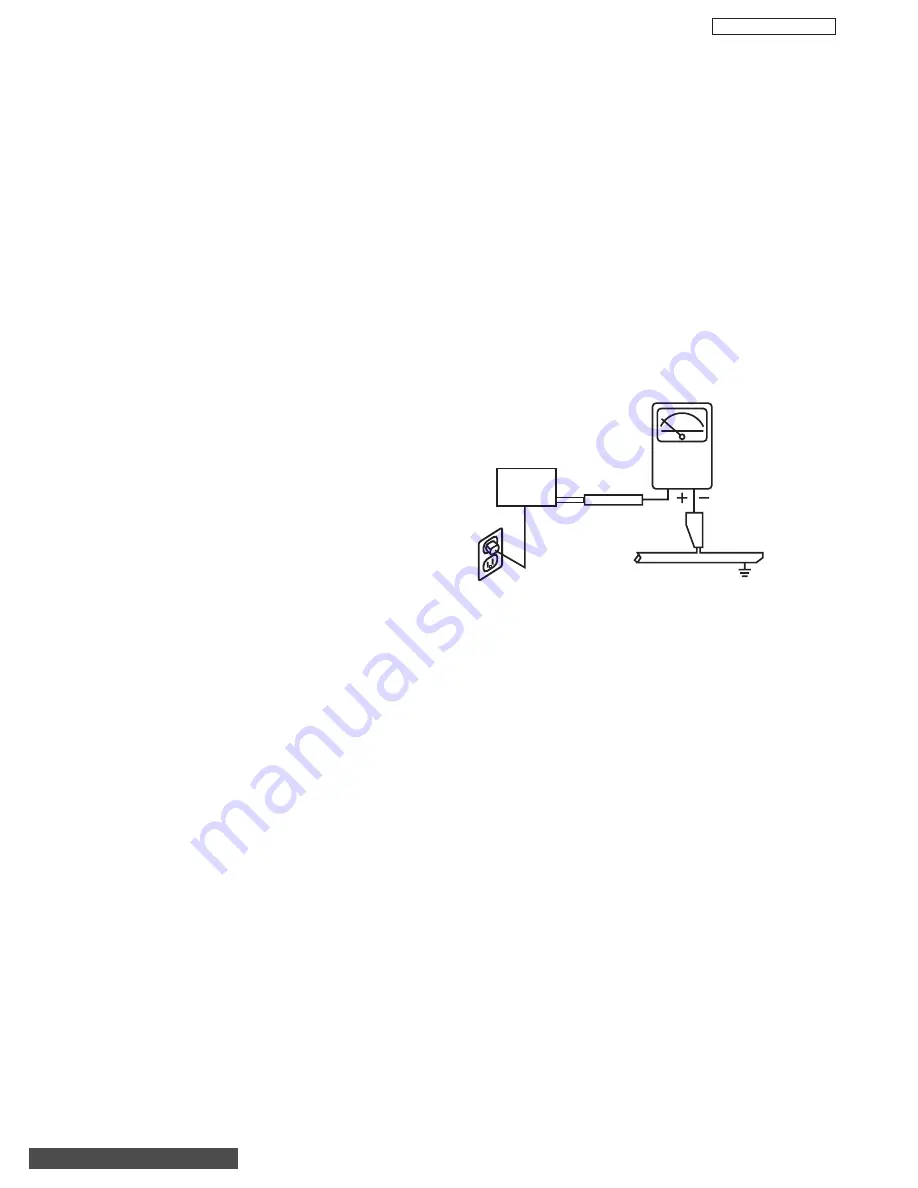
2
PT3-E/G AVC3-U
NOTICE:
Comply with all cautions and safety-related notes
located on or inside the cover case and on the chassis or plasma
module.
WARNING:
Since the chassis of the AVC unit and Plasma Panel
unit is connected to both sides of the AC power supply during
operation, whenever the receiver is plugged in, service should
not be attempted by anyone unfamiliar with the precautions
necessary when working on this type of receiver.
1. When service is required, an isolation transformer should be
inserted between power line and the receiver before any
service is performed on a “HOT” chassis receiver.
2. When replacing a chassis in the receiver, all the protective
devices must be put back in place, such as barriers, non-
metallic knobs, insulating cover-shields, and isolation
resistors, capacitors, etc.
3. When service is required, observe the original lead dress.
4. Always use manufacturer’s replacement components. Critical
components as indicated on the circuit diagram should not be
replaced by another manufacturer’s. Furthermore, where a
short circuit has occurred, replace those components that
indicate evidence of over heating.
5. Before returning a serviced receiver to the customer, the
service technician must thoroughly test the unit to be certain
that it is completely safe to operate without danger of electrical
shock, and be sure that no protective device built into the
receiver by the manufacturer has become defective, or
inadvertently defeated during servicing.
Therefore, the following checks should be performed for the
continued protection of the customer and service technician.
Leakage Current Cold Check
With the AC plug removed from the 120V AC 60Hz source,
place a jumper across Line 1 and Line 2 of the three plug
prongs, do not connect with the third prong, which is physical
ground.
Using an insulation tester (DC500V), connect one of its leads
to the AC plug jumper and touch with the other lead each
exposed metal part (antennas, screwheads, metal overlays,
control shafts, etc.), particularly any exposed metal part
having a return path to the chassis should have a resistor
reading over 4M
Ω
. Any resistance value below this range
indicates an abnormality which requires corrective action. An
exposed metal part not having a return path to the chassis will
indicate an open circuit.
SAFETY PRECAUTIONS
Leakage Current Hot Check
This check must be done considering the AVC or the PDP
monitor as one instrument each.
With any of the instruments completely reassembled (being
the instrument either the AVC center or the PDP monitor), plug
the AC line cord directly into a 120V AC outlet. (Do not use an
isolation transformer during this test.) Use a leakage current
tester or a metering system that complies with the American
National Standards Institute (ANSI) C101.0 Leakage Current
for Appliances. In the case of the PDP monitor set the AC
switch first in the ON position and then in the OFF position,
measure from across Line 1 and Line 2 of the three plug
prongs, do not connect with the third prong, which is physical
ground, to all exposed metal parts of the instrument
(antennas, handle bracket, metal cabinet, screw heads,
metallic overlays, control shafts, etc.), especially any exposed
metal parts that offer an electrical return path to the chassis.
Any current measured must not exceed 0.5 MIU. Reverse the
instrument power cord plug in the outlet and repeat test.
AC LEAKAGE TEST
ANY MEASUREMENTS NOT WITHIN THE LIMITS OUTLINED
ABOVE ARE INDICATIVE OF A POTENTIAL SHOCK HAZARD
AND MUST BE CORRECTED BEFORE RETURNING THE
RECEIVER TO THE CUSTOMER.
LEAKAGE
CURRENT
TESTER
(READING
SHOULD NOT
BE ABOVE 0.5MIU)
EARTH
GROUND
TEST ALL
EXPOSED
METAL SURFACES
DEVICE
UNDER
TEST
3-WIRE CORD
ALSO TEST WITH PLUG
REVERSED
(USING AC ADAPTER
PLUS AS REQUIRED)
TABLE OF CONTENTS
Summary of Contents for 32HDT50
Page 35: ...35 PT3 E G AVC3 U 5 7 WHITE BALANCE ADJUSTMENT OSD FLOW DIAGRAM BACK TO ADJUSTMENTS ...
Page 84: ...PRINTED CIRCUIT BOARD AVC3 U Audio Video PWB 84 PT3 E G AVC3 U BACK TO TABLE OF CONTENTS ...
Page 85: ...PRINTED CIRCUIT BOARD AVC3 U Audio Video PWB 85 PT3 E G AVC3 U ...
Page 86: ...PRINTED CIRCUIT BOARD AVC3 U Power PWB 86 PT3 E G AVC3 U ...
Page 87: ...PRINTED CIRCUIT BOARD AVC3 U Power PWB 87 PT3 E G AVC3 U ...
Page 88: ...PRINTED CIRCUIT BOARD AVC3 U SW Jig Control Filter PWB 88 PT3 E G AVC3 U PT3 E G FILTER PWB ...
Page 89: ...PT3 E G AVC3 U PRINTED CIRCUIT BOARD PT3 E G Signal Audio PWB 89 ...
Page 90: ...PRINTED CIRCUIT BOARD PT3 E G Signal Audio PWB 90 PT3 E G AVC3 U ...
Page 92: ...PT3 E G AVC3 U BLOCK DIAGRAM FC4 Unit 92 ...
Page 99: ...PT3 E G AVC3 U AVC3 U CHASSIS WIRING DRAWING 99 BACK TO TABLE OF CONTENTS ...
Page 100: ...100 PT3 E G AVC3 U PT3 E G CHASSIS WIRING DRAWING 42 Plasma Monitor Front ...
Page 101: ...101 PT3 E G AVC3 U PT3 E G CHASSIS WIRING DRAWING 42 Plasma Monitor Back ...
Page 102: ...102 PT3 E G AVC3 U PT3 E G CHASSIS WIRING DRAWING 32 Plasma Monitor Front ...
Page 103: ...103 PT3 E G AVC3 U PT3 E G CHASSIS WIRING DRAWING 32 Plasma Monitor Back ...