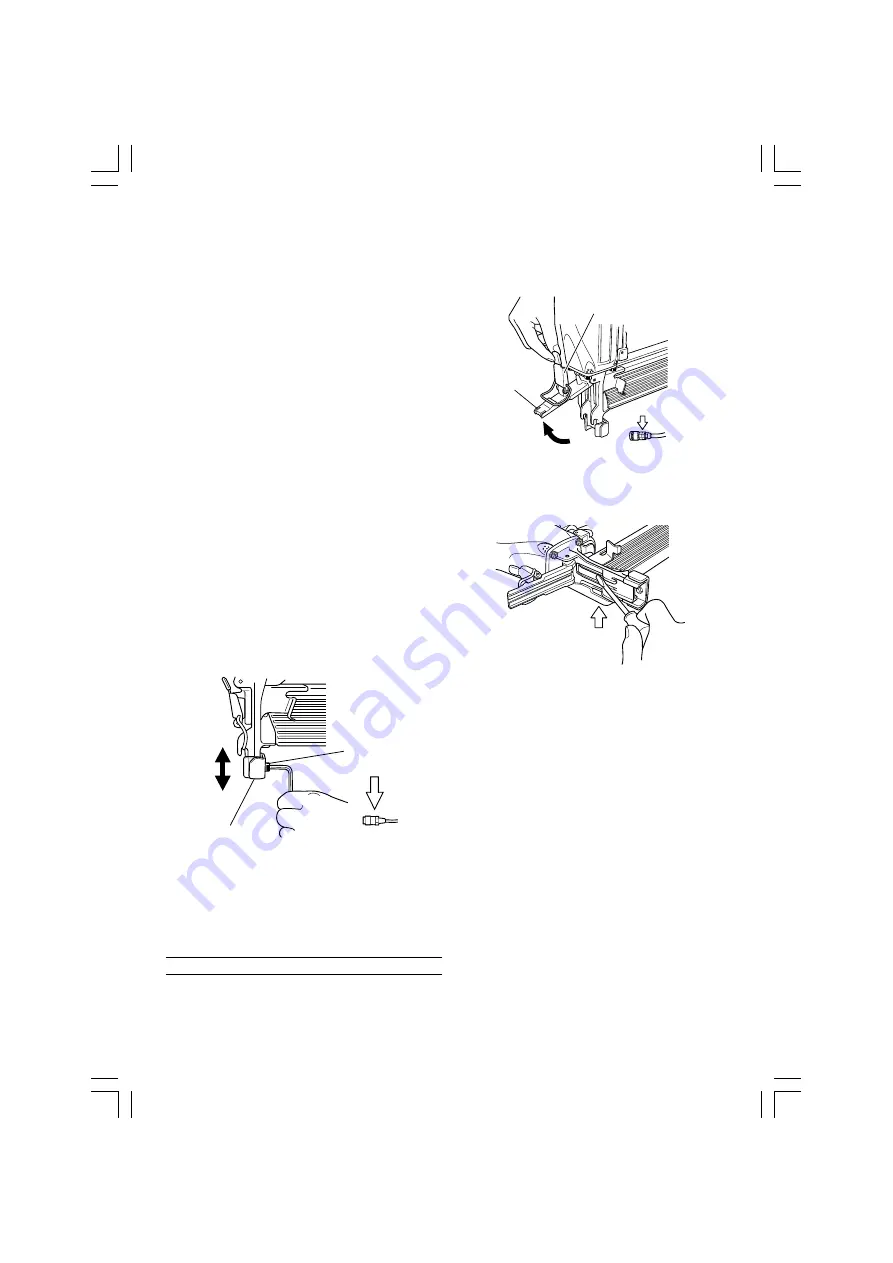
6
䡬
After stapling:
(1) disconnect air hose from the stapler;
(2) remove all staples from the stapler;
(3) supply 5 – 10 drops of Hitachi pneumatic tool
lubricant into the air plug on the stapler; and
(4) open the petcock on the air compressor tank to
drain any moisture.
䡬
Under low temperature conditions, the machine
sometimes does not operate correctly. Always operate
the machine at the appropriate ambient temperature.
2. How to adjust the stapling depth
To assure that each staple penetrates to the same
depth, be sure that:
(1) the air pressure to the stapler remains constant
(regulator is installed and working properly), and
(2) the stapler is always held firmly against the
workpiece.
If staples are driven too deep or shallow into the
workpiece, adjust the stapling in the following order.
CAUTIONS:
䡬
Before adjustment, always disconnect the hose
and release compressed air in the power tool.
䡬
During adjustment always keep your finger off the
trigger.
䡬
During adjustment make sure that no part of the
body, hands, or legs is ever in front of the staple
outlet.
Please carry out adjustments in the following order.
(See
Fig. 7
)
To adjust the driven-in depth of a staple, loosen the
screw that secures a push lever piece.
If the staple is driven in deeply, adjust the push lever
piece to ”down”, and if it’s driven in shallowly, adjust
the push lever piece to “up”.
Tighten the screw to fasten the push lever piece.
Fig. 7
NOTE:
䡬
Please use the minimum air pressure that is sufficient
to drive the staples to a suitable depth. If an overly
high pressure is used, the life of the piston damper
etc. will be shortened.
INSPECTION AND MAINTENANCE
CAUTION:
Be sure to disconnect the hose during cleaning
jams, inspection, maintenance and cleaning.
1. Countermeasure for staple jamming
(1) Remove all staples.
(2) Release the lock lever and open the blade guide. (See
Fig. 8
)
Fig. 8
(3) Remove the jammed staple with a slotted-head
screwdriver. (See
Fig. 9
)
Fig. 9
(4) Close the blade guide and latch.
(5) In case of frequent jam, contact a Hitachi authorized
service center.
2. Inspection and maintenance
Periodically inspect the device.
(1) Remove the four hexagon socket hd. bolts securing
the exhaust cover and remove the exhaust cover.
Then, cylinder, piston, and other parts can be removed
in respective assembly groups.
Wipe the drive bit, the piston sliding part and the body
interior with a cloth to remove deposited dirt.
(2) Confirm that the piston damper offers normal
operation. A damaged piston damper may cause
damage to other component parts.
(3) Carefully check the O-ring for wear while
disassembling. A worn or damaged O-ring may
deteriorate overall performance. Replace a worn or
damaged O-ring with new one.
(4) Prior to reassembling the device, apply grease
(Attolub No. 2 Grease) to the O-ring. Also, lubricate
the device with the recommended oil.
3. Check on mounting screws for each part
At regular intervals check every part for loose
mounting screws and whether or not there are any
air leaks. Retighten any loose screws. Operating the
equipment with loose screws untightened will incur
a hazard.
Push Lever Piece
Screw
Disconnect air hose
Blade Guide
Lock Lever
Disconnect air hose
01Eng_N5008AC2_Eng
08/7/31, 22:46
6