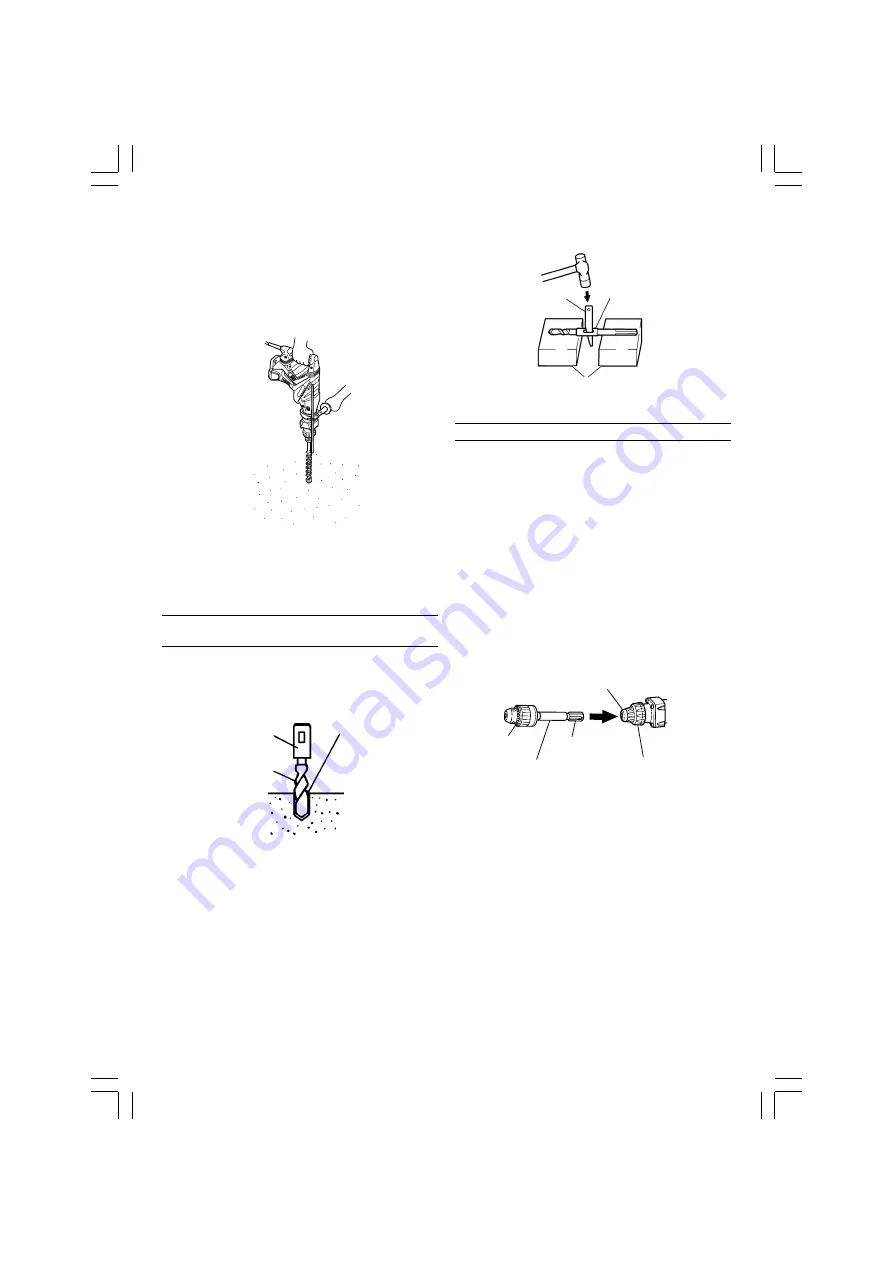
7
6. Warming up (Fig. 11)
The grease lubrication system in this unit may
require warming up in cold regions.
Position the end of the bit so makes contact with
the concrete, turn on the switch and perform the
warming up operation. Make sure that a hitting
sound is produced and then use the unit.
Fig. 11
CAUTION:
When the warming up operation is performed, hold
the side handle and the main body securely with
both hands to maintain a secure grip and be careful
not to twist your body by the jammed drill bit.
DRILLING AND DRIVING-IN OPERATIONS FOR
ANCHORS
1. When a taper shank adapter is used. (Fig. 12)
(1) Install drill bit with taper shank in the taper shank
adapter.
Fig. 12
(2) Turn the power on and drill a base hole to the depth
sounded by indicating groove on the drill bit.
(3) After cleaning out dust with a syringe, attach the
plug to the anchor tip and drive in the anchor with
a manual hammer.
(4) To remove the drill bit (taper shank), insert the
cotter into the slot of the taper shank adapter and
strike the head of the cotter with a manual hammer
supporting on a rest. (
Fig. 13
)
Fig. 13
USING DRILL CHUCK, CHUCK ADAPTER
Note that this machine can be used at “rotation only”
if separately sold parts such as drill chuck and chuck
adapter are attached. Use it with the selector lever
positioned at “ro hammering”.
CAUTION:
During operation, be sure to grip the handle and
the side handle firmly to prevent your body from
swaying.
(1) Switching to “ro hammering”
For switching to “ro hammering”, follow the
same procedures mentioned in [3. When drilling at
“ro hammering”].
(2) Attaching chuck adapter to drill chuck (
Fig. 14
)
(a) Attach the chuck adapter to the drill chuck.
(b) The SDS max shank of the chuck adapter is
equivalent to the drill bit. Therefore, follow the
same procedure as [How to install tool] for
attaching and detaching.
Fig. 14
(3) Drilling
(a) Even if you apply more-than-required pressure to
the machine body, drilling can never be performed
as quickly as you expect. Applying more force or
pressure to the machine body than what is needed,
on the contrary, damages the drill tip, resulting in
the declined working efficiency and shortened life
of this machine.
(b) A drill can snap sometimes when drilling is almost
finished. It is important to relax your thrusting
pressure when drilling is nearing the end.
Taper shank adapter
Drill bit (taper shank)
Indicating groove
shows standard
depth matching
the outside
diameter of the
anchor for
drilling.
Taper shank adapter
Cotter
Part of SDS
max shank
Chuck adapter
Drill chuck
Grip
Front cap
Rest
01Eng_DH50MRY_ENG
7/18/13, 8:54 AM
7