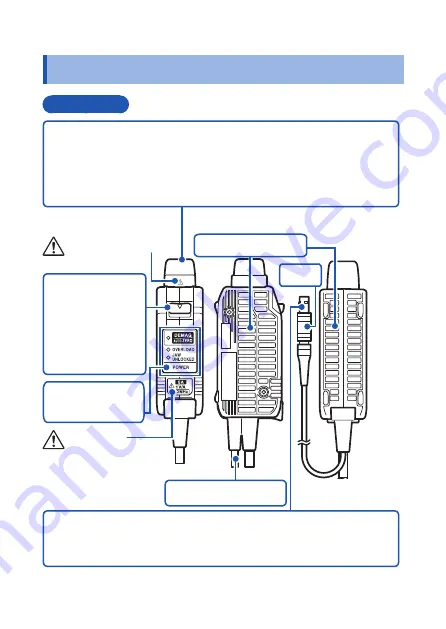
25
Parts Names and Functions
1.3 Parts Names and Functions
Terminator
Upper
side
Bottom side
Output connector
The current waveform of the measured conductor is output at a
constant rate (1 V/A).
Connect to the BNC input connector of the waveform
measurement instrument.
Unlock lever
The output
connector can be
disconnected by
pulling this part
toward you.
Power supply cord
Ventilation holes
Side
Power plug
Connect this to the 3269 or the 3272 Power Supply to supply
power to the sensor terminator.
Shell
Key and LEDs
(p. 28)
Summary of Contents for CT6700
Page 2: ......
Page 4: ...ii Contents...
Page 69: ...16 01 EN...
Page 70: ......
Page 71: ......
Page 72: ......