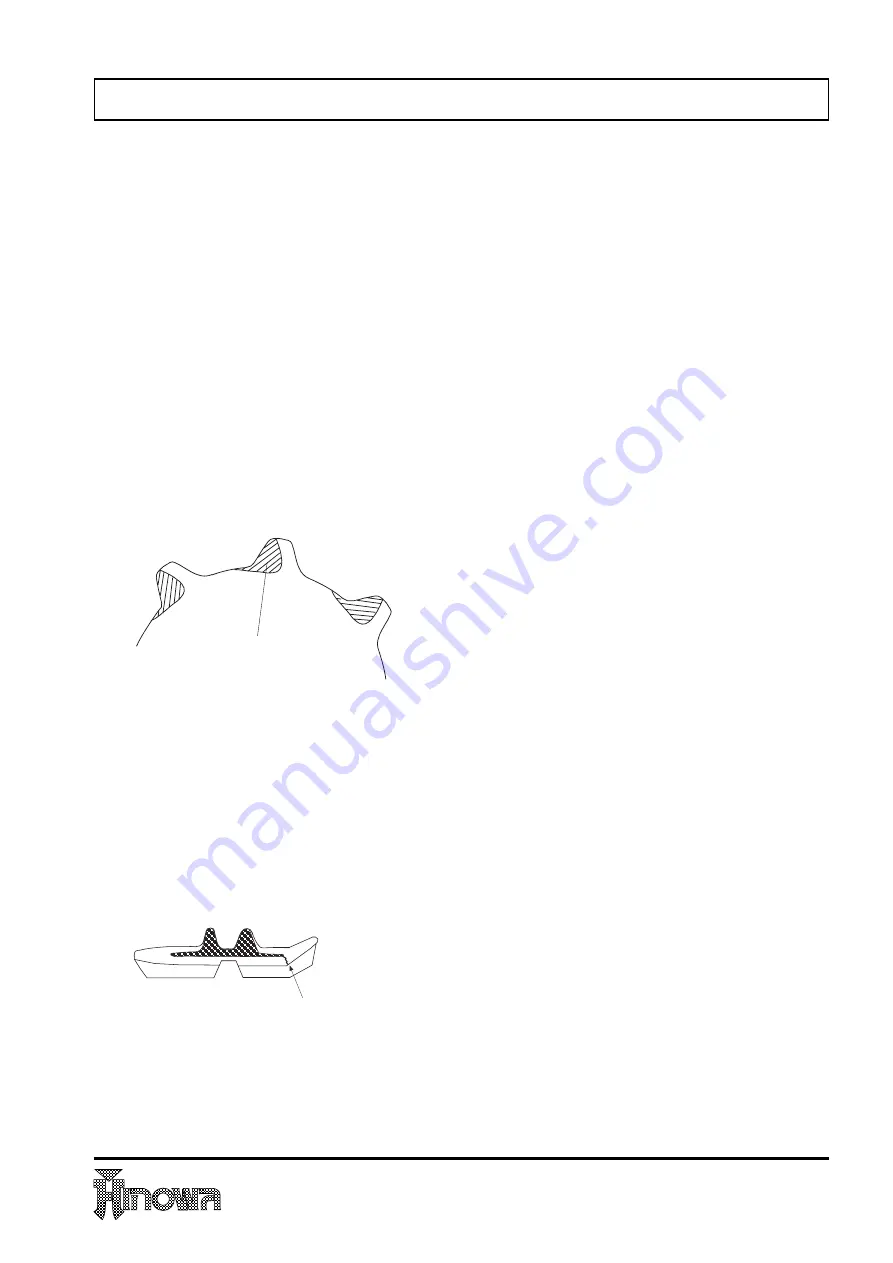
41
O
O
P
P
E
E
R
R
A
A
T
T
I
I
O
O
N
N
A
A
N
N
D
D
M
M
A
A
I
I
N
N
T
T
E
E
N
N
A
A
N
N
C
C
E
E
M
M
A
A
N
N
U
U
A
A
L
L
TP2000
‑ when stones or foreign matter accumulate between the track and the chassis of the
undercarriage;
‑ when the track comes off its guide;
‑ in the event of considerable friction, such as rapid changes in direction.
B)
Wear and breakage of the metal cores
As for the breakage of the steel wires described above, excessive tension may cause
the metal cores to bend or break, together with one of the following causes:
‑ improper contact between the cogwheel and the track;
‑ rotation of the inside rollers;
‑ operation on sandy ground.
C)
Separation of the metal cores
The metal core acts as the 'adhesive' for the
rubber between the core itself and the steel
wires.
Separation may be caused by excessive tension,
as for the breakage of the wires, for the fol‑
lowing reasons:
‑ the metal cores have been rolled up by the
worn cogwheel as shown in the figure. When
such wear and abrasions are found, the
cogwheel must be replaced as soon as possible.
In the case of breakage as described in paragraphs A‑B‑C, the track must be repla‑
ced, as this damage causes a complete loss of operability.
D)
Abrasion and cracks due to fatigue
1. Cracks at the base of the track patterns occur due to fatigue, since the rubber is
bent by the cogwheel and the idler roller, as shown in photo 4 (see the appen‑
dix).
2. Cracks and bends on the edge of the rubber are due to
the fact that the track is operated on curbs and sharp
concrete edges.
3. Cracks and abrasion on the rubber along the line of the guide rollers are due to
fatigue from the compression of the rubber by the weight of the wheel, together
with operation on sandy ground, or repeated and sudden changes in direction,
as shown in photos 6‑8‑9 (see the appendix).
PARTI USURATE
CRACK
W
ORN PARTS
Summary of Contents for TP2000
Page 12: ...Generelt 52220012 12 35 NO ...
Page 69: ......