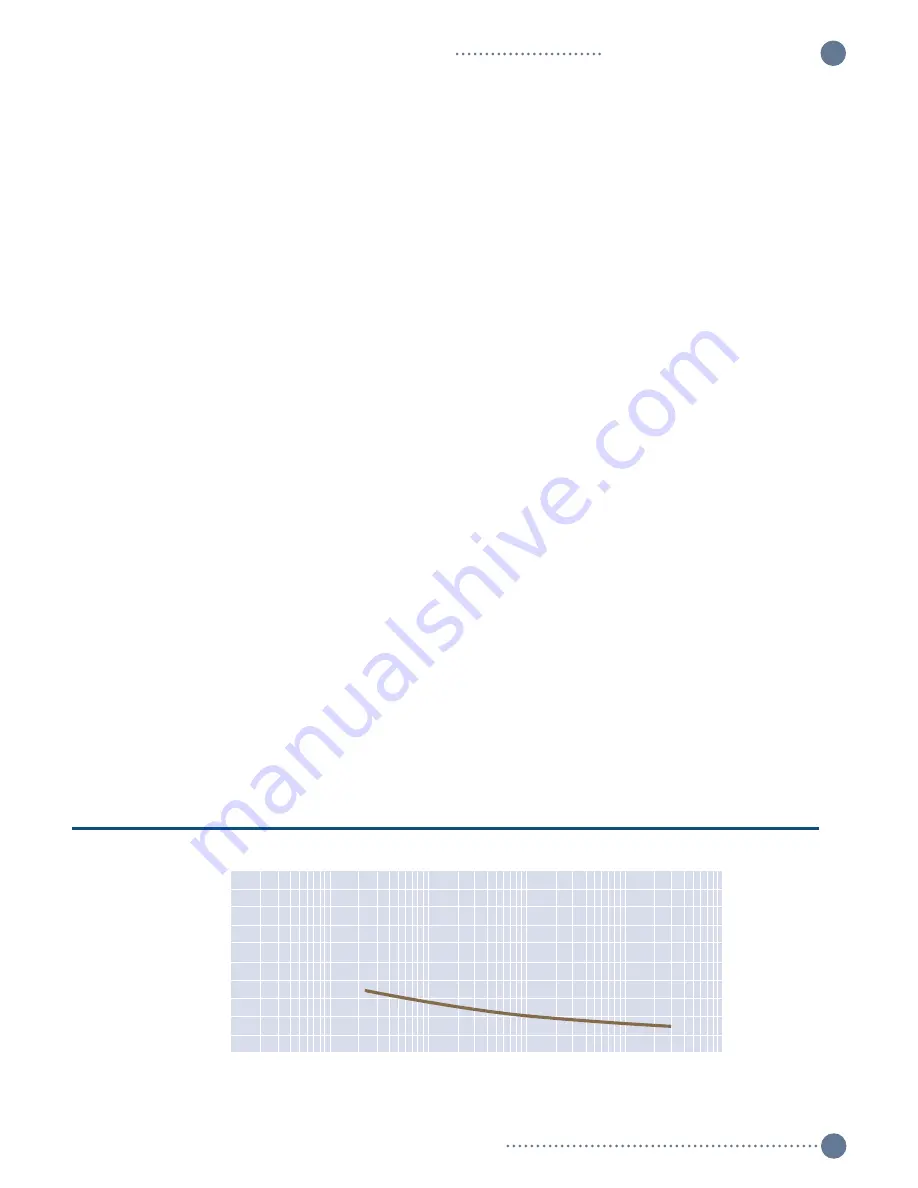
Strain Gage Reaction Torquemeters Installation Guide
S. Himmelstein and Company
© 2017 S. Himmelstein and Company—all rights reserved www.himmelstein.com
9
D.2 Allowable Torque Loads
D.2.1 Overload Considerations
Himmelstein Reaction Senors have torque overload ratings between
two (2) and five (5) times their full scale rating, model dependent.
The overload rating of your sensor is listed on the cover sheet. The
torque sensor will not yield (evidenced by a non-return to zero) if
subjected to an instantaneous peak torque up to its overload value.
Full scale and overload ratings are based on the peak stress seen
by the transducer. They are independent of stress duration except,
for cyclical (or fatigue) loading. Virtually all rotary power produc-
ing and absorbing devices produce pulsating rather than smooth
torque. Thus, in addition to its average torque value, the driveline
torque usually includes a fundamental (driving) frequency and
superimposed harmonics. Those torque perturbations can be mul-
tiplied when driveline resonance occurs. Additionally, in produc-
tion and other real-world applications, accidental loads and other
unforseen events can produce higher than expected torque levels.
Please refer to Application Note 221101D for more information.
For these reasons, reserve the region between the peak instan-
taneous torque and the sensor overload rating as a safety margin
for unexpected loads. Do not knowingly operate in the overload
region. When torques are expected to reach or exceed the full scale
rating, change to a higher capacity sensor or one with a higher
overload rating.
D.2.2 Fatigue Considerations
The sensor has infinite fatigue life with full torque reversals equal to
or less than half the overload rating. If instantaneous peak torques
exceed 50% of the overload rating, fatigue failure can occur.
When operating with peak torques greater than half the over-
load rating, fatigue life is a function of several factors. They include
the torque magnitude, the magnitude and type of extraneous loads
simultaneously applied, the total number of loading cycles, the
driveline damping, etc.
D.3 Allowable Extraneous Loads
Any force or moment the sensor sees, other than the reaction
torque input, is an extraneous load. Depending on the installa-
tion, they can include bending moments and axial thrust; see
Figures 7 and 8
. Rated Torque can be simultaneously applied
with rated bending or thrust loads without damage, provided
the extraneous loads are applied singly. Typical extraneous
load crosstalk is 1 to 2%. Crosstalk signals can be electrically
canceled. Refer to Section A.3.
D.3.1 Bending Loads
Allowable bending loads are model dependent. Most range from
half rated torque to eight times rated torque. Please refer to Model
Specifications for complete ratings.
D.3.2 Thrust Loads
Allowable thrust loads are model dependent. Most range, in
lbf, from rated torque, in lbf-in, to twenty times rated torque.
Please refer to Model Specifications for complete ratings.
D.4 Contaminants
These devices should not be exposed to corrosive or electrically
conductive fluids. They are not waterproof although they are water
resistant. Pure water and hydrocarbon lubricants have no effect
on operation. As a precaution, they should be shielded from direct
liquid spraying.
D.5 Hazardous Environments
If used in a hazardous environment, the sensors must be connected
via approved safety barriers. Safety barriers are sealed, passive
networks installed in each wire that connects the hazardous and
safe locations. They limit electrical energy passing between the two
locations to a safe value.
10
3
10
4
10
5
10
6
10
7
10
8
Fatigue Life, Cycles
200
180
160
140
120
100
80
60
40
20
0
Minimun Stress, KSI
Figure 11. Typical Fatique Life Characteristics