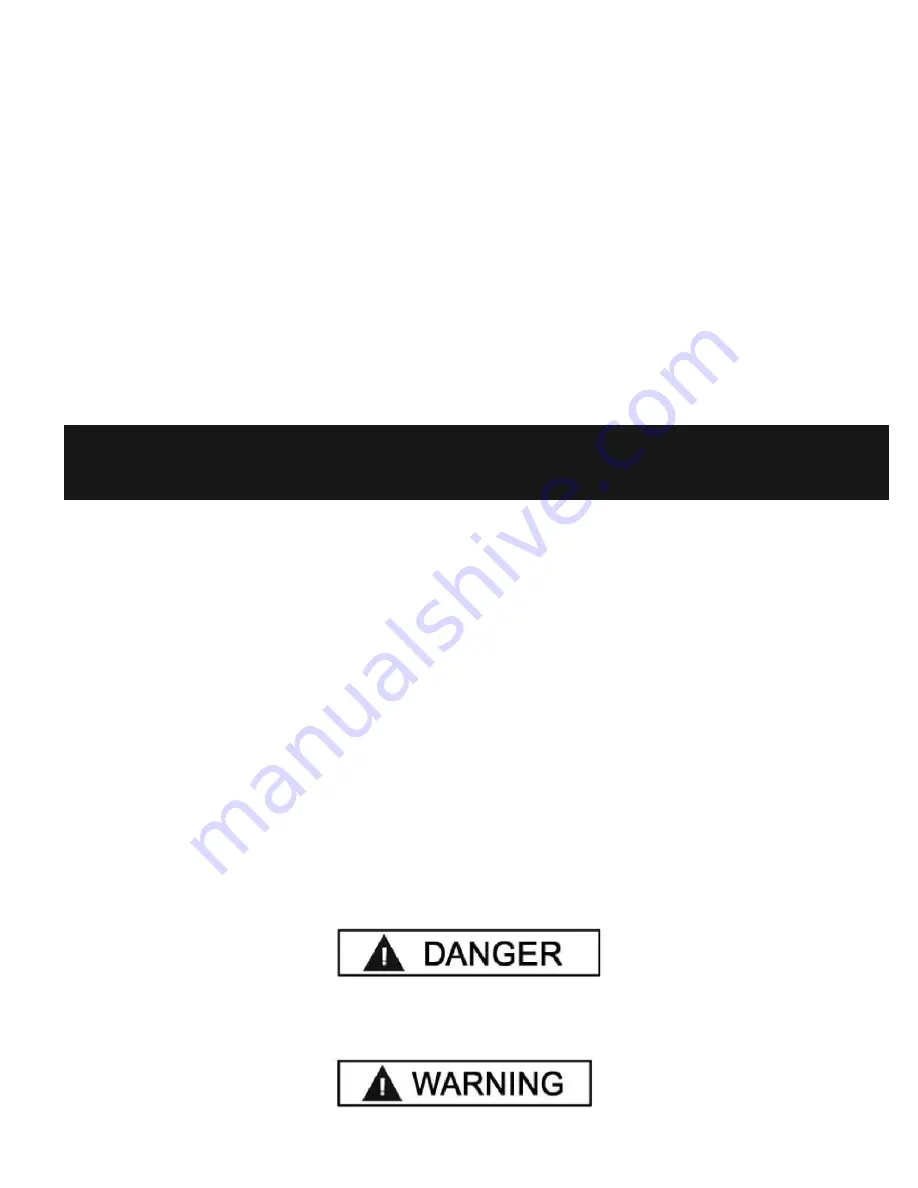
5
•
Shall establish procedures to periodically inspect the lift in accordance with the lift manufacturer’s instructions and
regional requirements. The Employer Shall ensure that lift inspectors are qualified and that they are adequately trained
in the inspection of the lift.
•
Shall establish procedures to periodically maintain the lift in accordance with the lift manufacturer’s instructions and
regional requirements, Inspection and Maintenance and The Employer Shall ensure that lift maintenance personnel are
qualified and that they are adequately trained in the maintenance of the lift.
•
Shall maintain the periodic inspection and maintenance records recommended by the manufacturer and regional
requirements.
•
Shall display the lift manufacturer’s operating instructions; ALI/SM 93
-1, ALI Lifting it Right safety manual; ALI/ST-10
ALI Safety Tips card; in a conspicuous location in the lift area convenient to the operator.
•
Shall not modify the lift in any manner without the prior written consent of the manufacturer or regional requirements.
•
Shall provide necessary lockout/ tagout means for energy sources per ANSI Z244.1-1982 (R1993), safety requirements
for the lockout / tagout of energy sources, before beginning any lift repairs.
INSTALLER / OPERATOR: PLEASE READ THE ENTIRE CONTENTS OF THIS MANUAL PRIOR TO INSTALLATION
AND OPERATION. BY PROCEEDING WITH LIFT INSTALLATION AND OPERATION YOU AGREE THAT YOU FULLY
UNDERSTAND AND COMPREHEND THE FULL CONTENTS OF THIS MANUAL. FORWARD THIS MANUAL TO ALL
OPERATORS. FAILURE TO OPERATE THIS EQUIPMENT AS DIRECTED MAY CAUSE INJURY OR DEATH.
•
I have visually inspected the site where the lift is to be installed and verified the concrete to be in good condition and
free of cracks or other defects. I understand that installing a lift on cracked or defective concrete could cause lift failure
resulting in personal injury or death.
•
I understand that a level floor is required for proper installation and level lifting.
•
I understand that I am responsible if my floor is of questionable slope and that I will be responsible for all charges
related to pouring a new level concrete slab if required and any charges.
•
I understand that High Lift lifts are supplied with concrete fasteners meeting the criteria of the Australian Standards, and
that I will be responsible for all charges related to any special regional structural and/or seismic anchoring requirements
specified by any other agencies and / or codes such as the Uniform Building Code (UBC) and / or International Building
Code (IBC).
•
I will assume full responsibility for the concrete floor and condition thereof, now or later, where the above equipment
model(s) are to be installed. Failure to follow danger, warning, and caution instructions may lead to serious personal
injury or death to operator or bystander or damage to property.
•
I understand that High Lift lifts are designed to be installed in indoor locations only. Failure to follow installation
instructions may lead to serious personal injury or death to operator or bystander or damage to property or lift.
Failure to follow danger, warning, and caution instructions may lead to serious personal injury or death to operator or
bystander or damage to property.
HIGH-LIFT
Summary of Contents for YL130
Page 9: ...9 MAXJAX PARTS BOX H I G H L I F T ...
Page 12: ...12 1 2 NOTE 3 4 5 H I G H L I F T ...
Page 26: ...26 H I G H L I F T ...