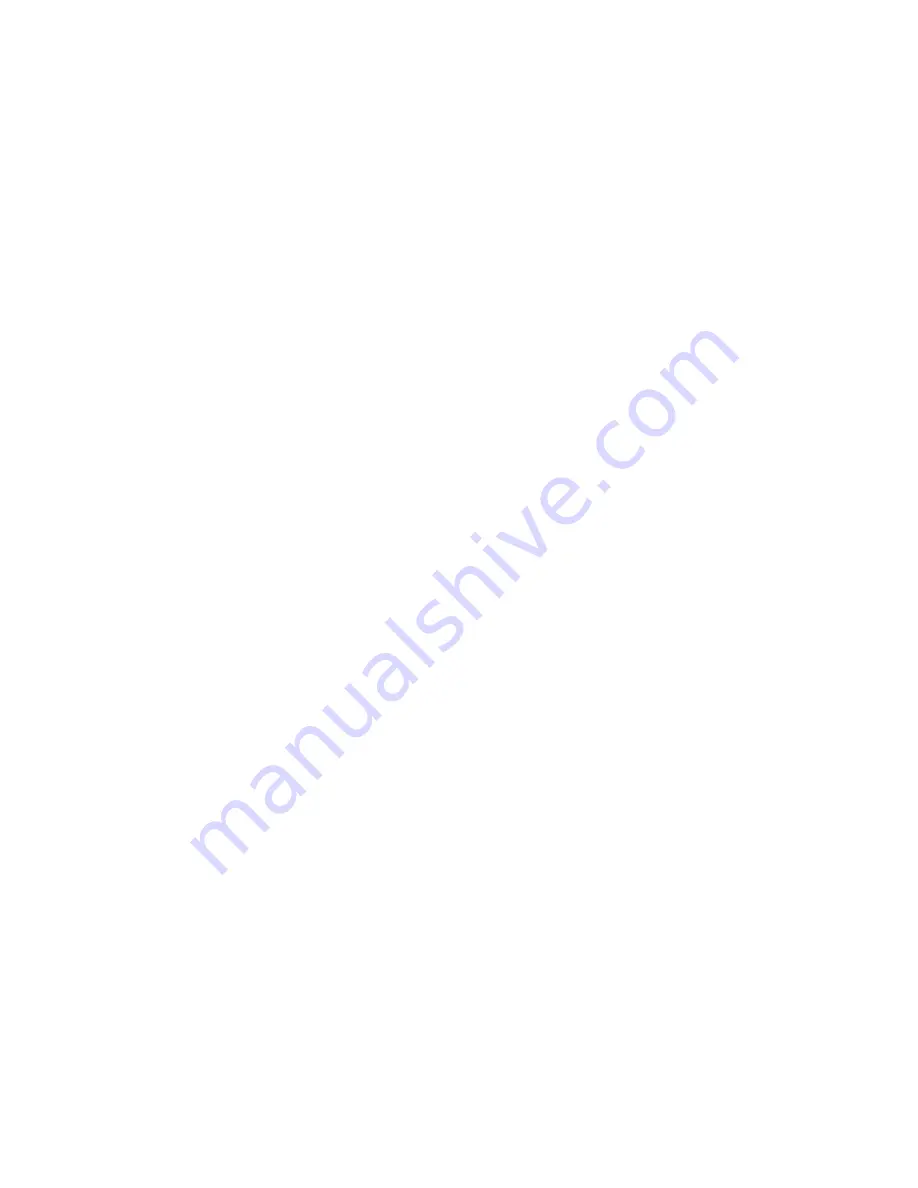
H.E.R.O. INDUSTRIES LTD.
1100MD OWNERS MANUAL - “B” VERSION
3
IMPORTANT SAFETY PRECAUTIONS
WARNING
NEVER PLACE FINGERS NEAR SPRAY TIP OF GUN. NEVER POINT GUN TOWARD
ANY PART OF YOUR BODY, OR THAT OF ANY OTHER PERSON. MATERIAL ISSUING
FROM THE SPRAY TIP IS AT HIGH PRESSURE. IF FINGERS, OR ANY PART OF THE
BODY ARE PLACED NEAR THE TIP OF THE SPRAY GUN, IT IS POSSIBLE THAT THE
SPRAY COULD BREAK THE SKIN AND INJECT SOME OF THE SPRAY MATERIAL. IF
INJURY DOES OCCUR, SEEK THE IMMEDIATE ATTENTION OF A MEDICAL DOCTOR.
BE PREPARED TO INFORM THE DOCTOR WHAT FLUID WAS INJECTED, IF THE
INJURY IS OF AN INJECTION NATURE.
EQUIPMENT AND CHEMICALS WHEN USED
IMPROPERLY CAN BE DANGEROUS!
ý
NEVER
place any part of the body in front of the spray tip or aim the gun toward any part of the
body.
ý
NEVER
point the gun toward any individual.
ý
NEVER
treat any injury as a simple cut. If injury does occur, seek immediate medical attention. Be
prepared to inform the doctor what fluid was injected.
ý
NEVER
allow another person to use the sprayer unless he is thoroughly instructed on its
operation and has read all safety precautions in this manual and all safety warning labels attached to
unit.
ý
NEVER
use around children.
ý
NEVER
attempt to perform any maintenance or service on any part of the unit spray system
without first;
1. Shutting off the unit.
2. Disconnecting the power cord from the outlet.
3. Relieving all pressure in the pump by triggering the gun.
4. Locking gun trigger in "LOCKED" position, with gun locked closed.
ý
NEVER
operate the sprayer without the tip guard complete and in place.
ý
NEVER
spray any material in the vicinity of open flame, pilot lights, electrical outlets or any
other source of ignition.
ý
NEVER
spray volatile materials with flash points lower than 140 F (60 C).
ý
NEVER
attempt to stop any leakage in the paint line or at any fitting with your hand or any part of
your body. Immediately shut off the unit should leakage occur.
ý
NEVER
wash an electric motor, nor operate it in the rain or in wet or damp areas, to protect
yourself from electric shock.
ý
NEVER
allow paint hose to become kinked, or to vibrate against rough or sharp surfaces.
ý
NEVER
operate the unit at pressures higher than the pressure rating of the lowest rated
component in the system, or at pressure higher than factory preset.
ý
NEVER
spray in an enclosed area. The spraying area must be well ventilated to safely remove
chemical vapors.
ý
NEVER
operate the unit with worn or damaged accessories, or with accessories other than those
supplied by H.E.R.O. Industries, unless the accessories have been first specifically approved in
writing by H.E.R.O. Industries Ltd.
ý
NEVER
allow the unit to be serviced or repaired anywhere other than an authorized H.E.R.O.
Service Center, or with other than genuine H.E.R.O. parts or components.
ý
NEVER
leave unit unattended without first shutting off, triggering the gun to relieve all pump
pressure, and setting the trigger lock on gun in "LOCKED" position, with gun locked closed.