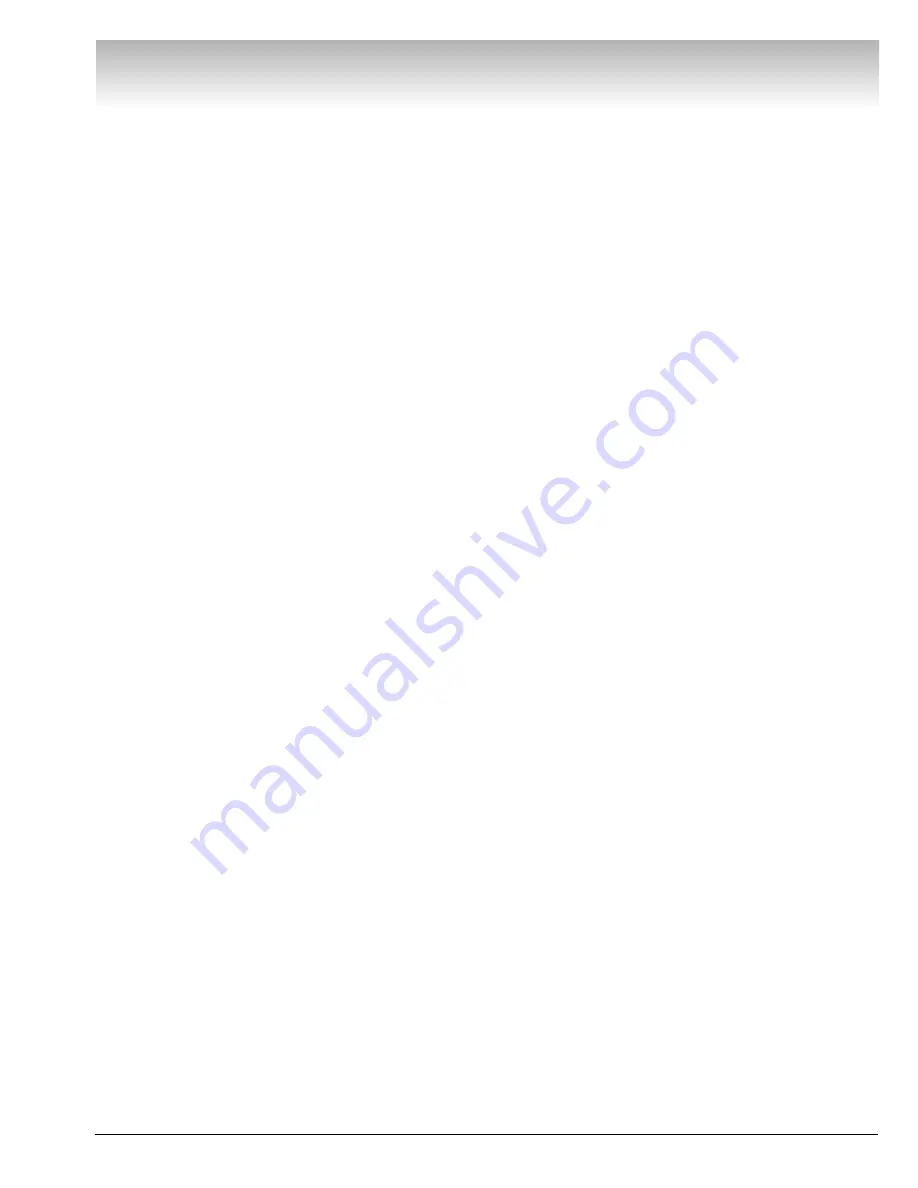
Service Manual — COATS Models 950/950 ProRacer/1025/1050/1055 • 5
14.0). After these parameters have been entered, the
weight displays will show 0 and the machine returns to
normal operating mode.
5.
Return the arm to the park position. Then pull the
arm out and position into the radius of the wheel. The
correct A and D readings should appear on the wheel
parameter display. These values would be within ± 0.20
of the values entered in calibration. If the readings are
not within tolerance, check for slippage of the pot pul-
leys. If they are tight, see A & D ARM PROBLEMS.
Stop-On-Top Calibration (Code 20/21)
1.
If the test wheel is not mounted to the machine,
mount it.
2.
Press and hold the SHIFT key and press 0. Then
press 2 followed by 0. This will toggle the machine into
Stop on Top feature. The weight display should now
read SOT ON. If the display now reads SOT OFF, repeat
the key sequence shown above.
3.
Add a 4 oz. weight to the outside of the test wheel.
4.
Press the START button.
5.
When the wheel stops press and hold the SHIFT
key and press 0. Then press 2 followed by 1 to cali-
brate.
6.
Repeat steps 4 and 5 until the wheel stops with
the 4 oz. weight at approximately 6 o'clock.
*Distance Gauge Tape Placement (Optimize A)
If the ACCURACY CHECK fails, try entering an A dimen-
sion .1 higher than the one used originally. If the plane
separation gets worse, try using an A dimension .1 lower
than the one used originally. If the plane separation gets
better, keep increasing or decreasing the A dimension
until an acceptable value is achieved. Calibrate the
machine and perform the ACCURACY CHECK. Repeat
this procedure until the ACCURACY CHECK produces an
acceptable result. Move the distance tape to the posi-
tion to allow proper A dimension entry. Calibrate the bal-
ancer using the new A dimension.
Error Codes
The following is a list of error codes. When the bal-
ancer is cycled several operating parameters are
checked. If one of these parameters is not within toler-
ance, the machine will generate one of the following
error codes and use the weight reading LEDs to display
the error code. An explanation of these codes and a
troubleshooting procedure follows each code.
Err -
Displayed when an entered parameter entered
is not in the acceptable range or not entered.
Err Hod -
Displayed when the hood switch is not
closed (the hood is up, the hood switch is bad) when
the machine cycle is started. Try closing the hood if the
machine still gives this error. See WHEEL DOES NOT
SPIN.
Err Hub -
Displayed when the machine detects a no
“load” condition on the motor at start up. If there is a
wheel mounted on the arbor, check the mounting of
the wheel to make sure it is not “slipping”. See
REPEATABILITY PROBLEMS.
Err Cal -
Displayed when an error has occurred dur-
ing the calibration process. It can be caused by not
placing the calibration weight on the wheel for one or
both spins, or a defective PCB. The code is generated
by equal piezo outputs in consecutive spins.
Err 1 -
Displayed when the wheel moves slowly
when the start button is depressed. This can be caused
by a defective motor, defective contactor, motor control
board, or incorrect wiring of either of the previous. See
WHEEL DOES NOT SPIN.
Err 2 -
Similar to Err 1, this message is displayed
when the time to reach measurement speed is too
long. This can be caused by a defective motor, defec-
tive contactor, motor control board, or incorrect wiring
of either. See WHEEL DOES NOT SPIN.
Err 3 -
Displayed when no encoder pulse is detected
after the start button is pressed (the motor did not
spin). This can be caused by incorrect wiring to the
encoder, contactor, motor control board, motor, PCB, or
safety interlock switch, If the drive motor did not start
see the troubleshooting procedure for WHEEL DOES
NOT SPIN. If the drive motor does begin to spin. See
OPTICAL ENCODER CHECKING PROCEDURE.
Err 4 -
Displayed when the machine detects the
wheel rotation in the reverse direction. This can be
caused by incorrect encoder or motor phasing, motor
control board or a bad PCB. See WHEEL DOES NOT
STOP.
Err 5 -
This message is displayed when the time to
brake the wheel to a stop at the end of the cycle is too
Direct Drive