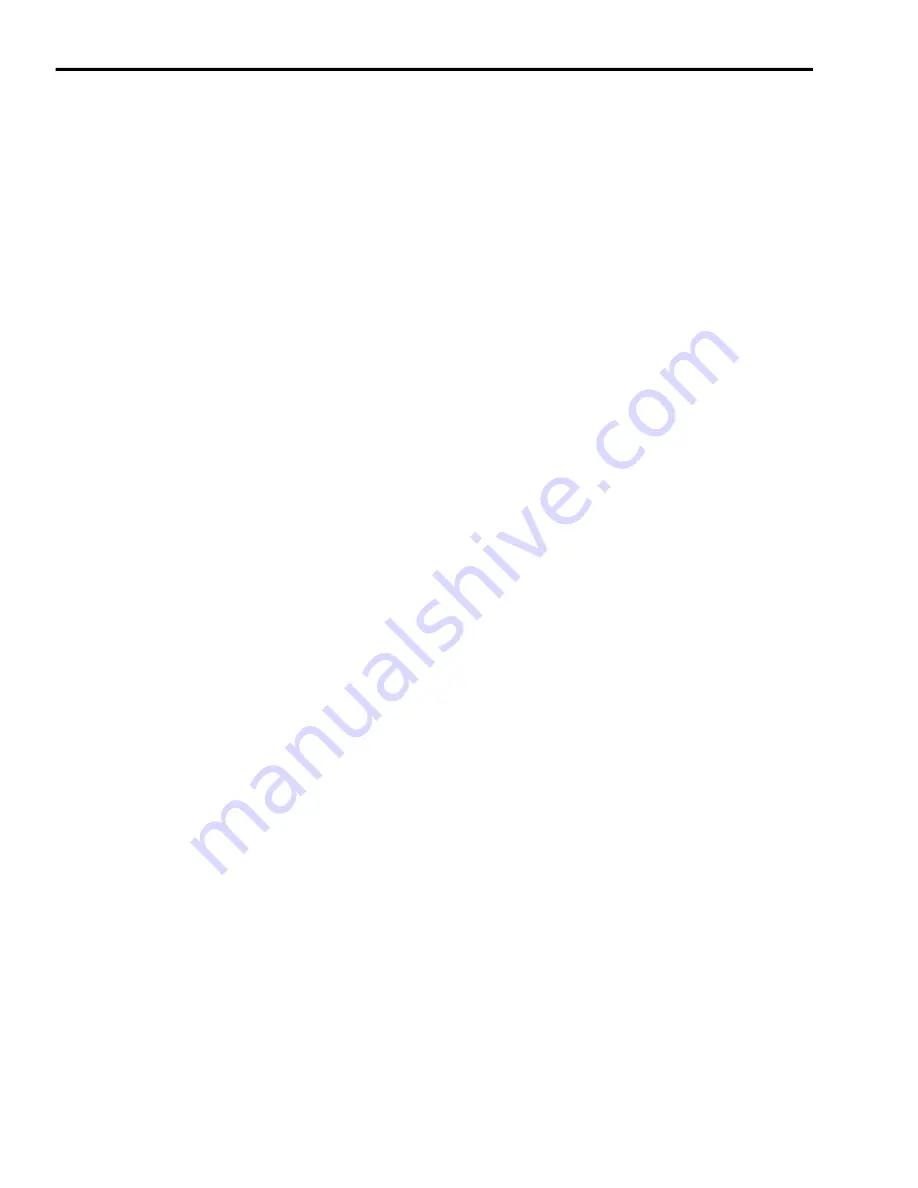
10
HM1734-WM Strain Gage Input Module
OUTPUT TAG DESCRIPTIONS
VIB
RATION FILTER
Filter ON/OFF Bit
0 = Normal Average
1 = Rolling Average
MSF BITS – (Motion Stabilization Filter)
Used for applications with constant or static type loads to keep display value stable.
MSF1_2 (1 count up – 2 counts down).
MSF2_4
MSF4_8
MSF5_10
Set one bit only.
ZERO-DEAD-BAND Bits
Useful for Auto-Tare functions with production runs.
Set only one bit.
ZEROBAND_025 = .025% full scale
ZEROBAND_05 = .05% full scale
ZEROBAND_075 = .075% full scale
Auto tare occurs when load cell weight is at bit level or lower.
SET AVERAGE SAMPLE Bits
See Required Controller Tags:
HM1734WM1_a[8]