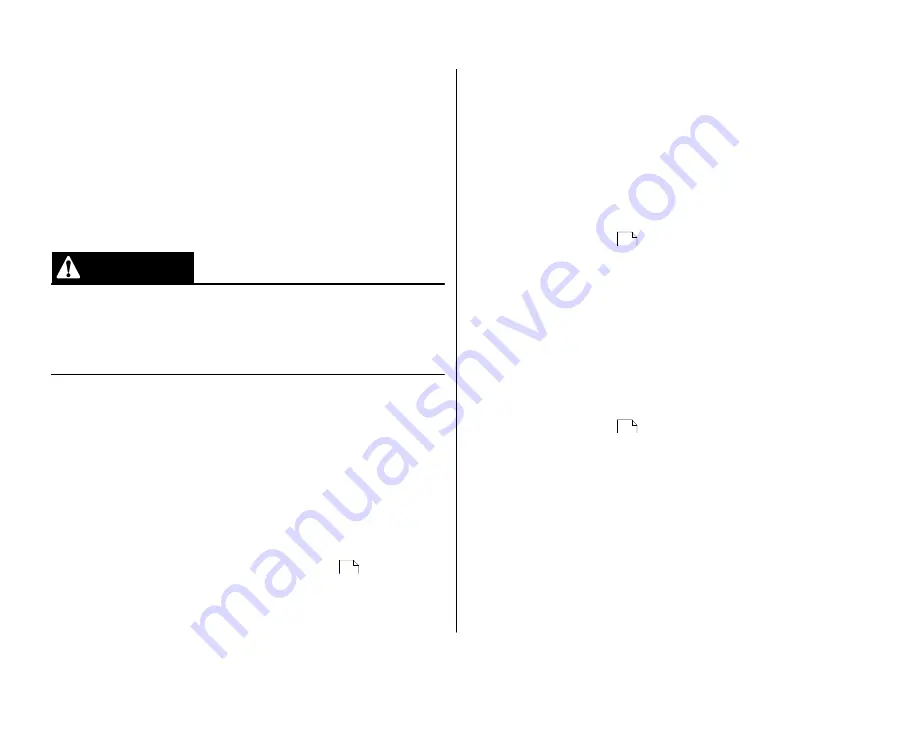
Issued September 2017
On-Route Operation Procedures
Copyright 2017, Heil Environmental
Printed in U.S.A.
127
DuraPack
®
5000
LOADING REFUSE WITH A ROLL BAR
MECHANISM (CONTINUED)
d. When the refuse container’s cover is not closed
because it is overfilled with refuse:
o
Raise the container enough to empty part of
the refuse from container into the hopper.
o
Lower the container to the ground.
CAUTION
The upper panel in/out and blade up/down operations can
push refuse out of the hopper or break objects. Refuse
broken by the blade can cause moderate or minor injury.
Stay clear of the packer panel during upper panel in/out
and blade up/down operations.
o
Perform Step 3 (sweep the refuse and
compact it into the hopper).
o
RAISE the container and finish emptying the
container.
e. After the refuse container is empty of refuse,
PUSH the control lever for the roll bar mechanism
until the refuse bin rests firmly on the ground and
you can release the latch bar.
f. RELEASE the container’s trunnion bar from the
.
g. RELEASE the container from the roll bar
mechanism.
h. MOVE the container to its pick-up location.
3. Sweep the refuse from the hopper and pack it into
the body.
a. PULL the upper panel and blade levers at the
same time and RELEASE the levers. The levers
will self-center at the end of the commanded
position by way of valve internal hydraulic
pressure. See
.
b. The upper panel will move OUT and the blade will
move UP. STOP the blade UP operation when the
blade is at the pinch point with the hopper sill.
c. Watch for refuse that is pushed out of the hopper.
d. PUSH the upper panel and blade levers at the
same time and RELEASE the levers. The levers
will self-center at the end of the commanded
position by way of valve internal hydraulic
pressure. See
.
e. The upper panel and blade move and compact
the refuse into the body.
4. Repeat Steps 1 and 3 as necessary to compact the
refuse.
133
111
111
Summary of Contents for DuraPack 5000 2017
Page 10: ...NOTES DuraPack 5000 2...
Page 36: ...NOTES DuraPack 5000 28...
Page 64: ...NOTES DuraPack 5000 56...
Page 68: ...NOTES DuraPack 5000 60...
Page 86: ...NOTES DuraPack 5000 78...
Page 104: ...NOTES DuraPack 5000 96...
Page 114: ...NOTES DuraPack 5000 106...
Page 152: ...NOTES DuraPack 5000 144...
Page 156: ...NOTES DuraPack 5000 148...
Page 160: ...NOTES DuraPack 5000 152...
Page 164: ...NOTES DuraPack 5000 156...
Page 202: ...NOTES DuraPack 5000 194...