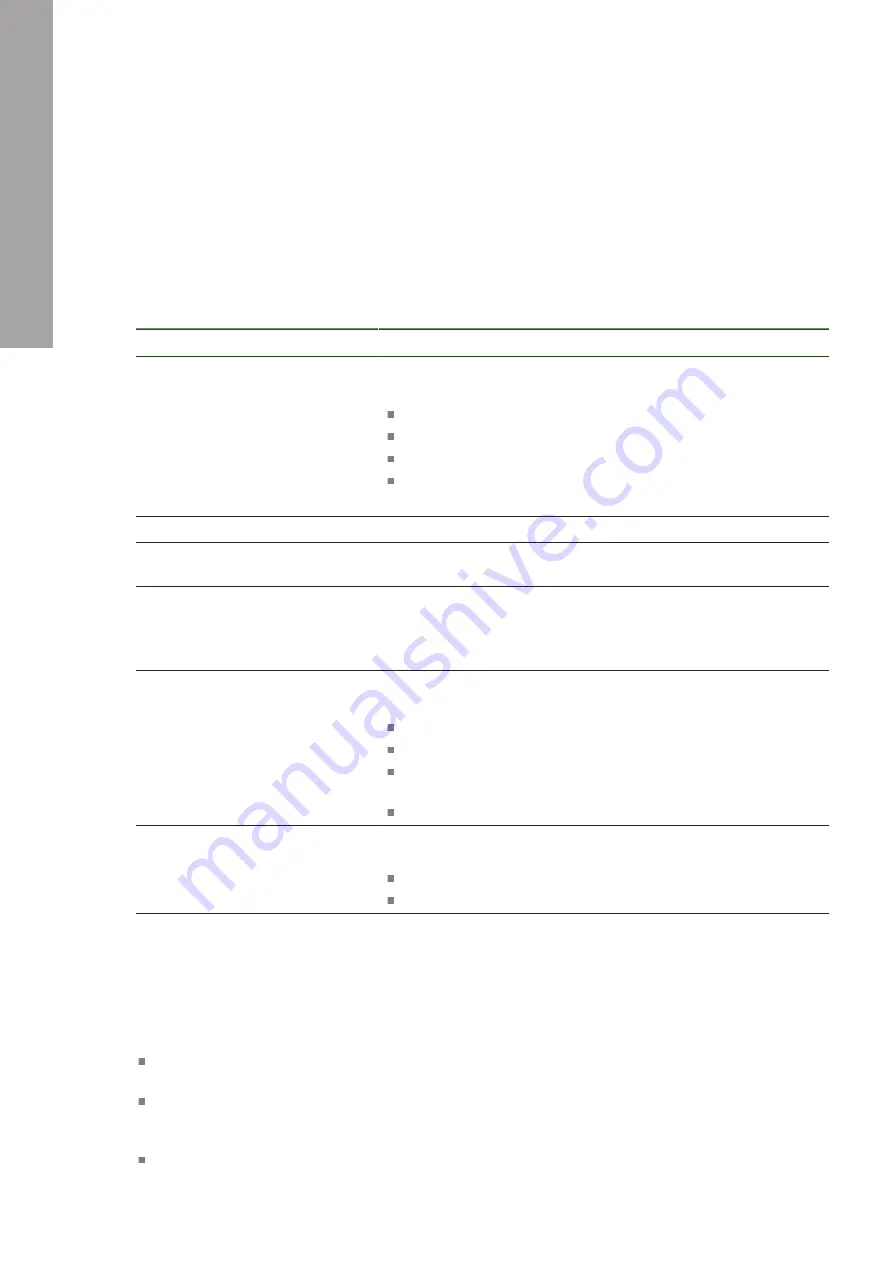
Information for OEM and Setup users | Commissioning
II
4.6.3
Configuring axes for encoders with EnDat interface
If the corresponding encoder input has already been assigned to an axis, a
connected encoder with EnDat interface is automatically detected upon restart, and
the settings are adapted. Alternatively, you can assign the encoder input after you
have connected the encoder.
Prerequisite:
An encoder with EnDat interface is connected to the product.
Settings
►
Axes
►
<Axis name>
►
Encoder
Parameter
Explanation
Encoder input
Assignment of the encoder input to the axis of the product
Settings:
Not connected
X1
X2
X3
Interface
Automatically detected
EnDat
interface type
ID label
Information on the encoder that was read from the electronic ID
label
Diagnosis
Results of encoder diagnostics, evaluation of encoder function
(e.g., based on functional reserves)
"Diagnostics for encoders with EnDat inter-
Encoder model
Connected encoder model
Settings:
Linear encoder
: Linear axis
Angle encoder
: Rotary axis
Angle encoder as linear encoder
: Rotary axis is displayed as
linear axis
Default value: Depending on the connected encoder
Mechanical ratio
For display of a rotary axis as a linear axis:
traverse path in mm per revolution
Setting range:
0.1 mm ... 1000 mm
Default value:
1.0
Reference point displacement
Configuration of the offset between the reference mark and the
zero point
"Reference point displacement", Page 87
Using an
Angle encoder as linear encoder
Certain parameters must be taken into account when configuring an angle encoder
or rotary encoder as a linear encoder, in order to prevent an overrun of the system.
The mechanical ratio must be chosen such that the maximum traverse range of
21474.483 mm is not exceeded
The reference mark shift should only be used when considering the maximum
traverse range of
±
21474.483 mm, since this limit applies both with and without
a reference mark shift
Only for multiturn rotary encoders with EnDat 2.2:
the rotary encoder must be
mounted such that an overrun of the rotary encoder does not affect the machine
coordinates negatively
86
HEIDENHAIN | GAGE-CHEK 2000 | Operating Instructions | 06/2022
Summary of Contents for GAGE-CHEK 2000
Page 1: ...GAGE CHEK 2000 Operating Instructions Evaluation Unit English en 06 2022...
Page 3: ...I General information...
Page 7: ...1 Fundamentals...
Page 14: ...2 Safety...
Page 19: ...3 Basic operation...
Page 43: ...II Information for OEM and Setup users...
Page 48: ...1 Transport and storage...
Page 54: ...2 Mounting...
Page 60: ...3 Installation...
Page 72: ...4 Commissioning...
Page 121: ...5 Setup...
Page 150: ...6 File management...
Page 157: ...7 Settings...
Page 172: ...8 Servicing and maintenance...
Page 184: ...9 Removal and disposal...
Page 186: ...10 Specifications...
Page 194: ......
Page 195: ...III Information for the Operator user...
Page 240: ...14 What to do if...