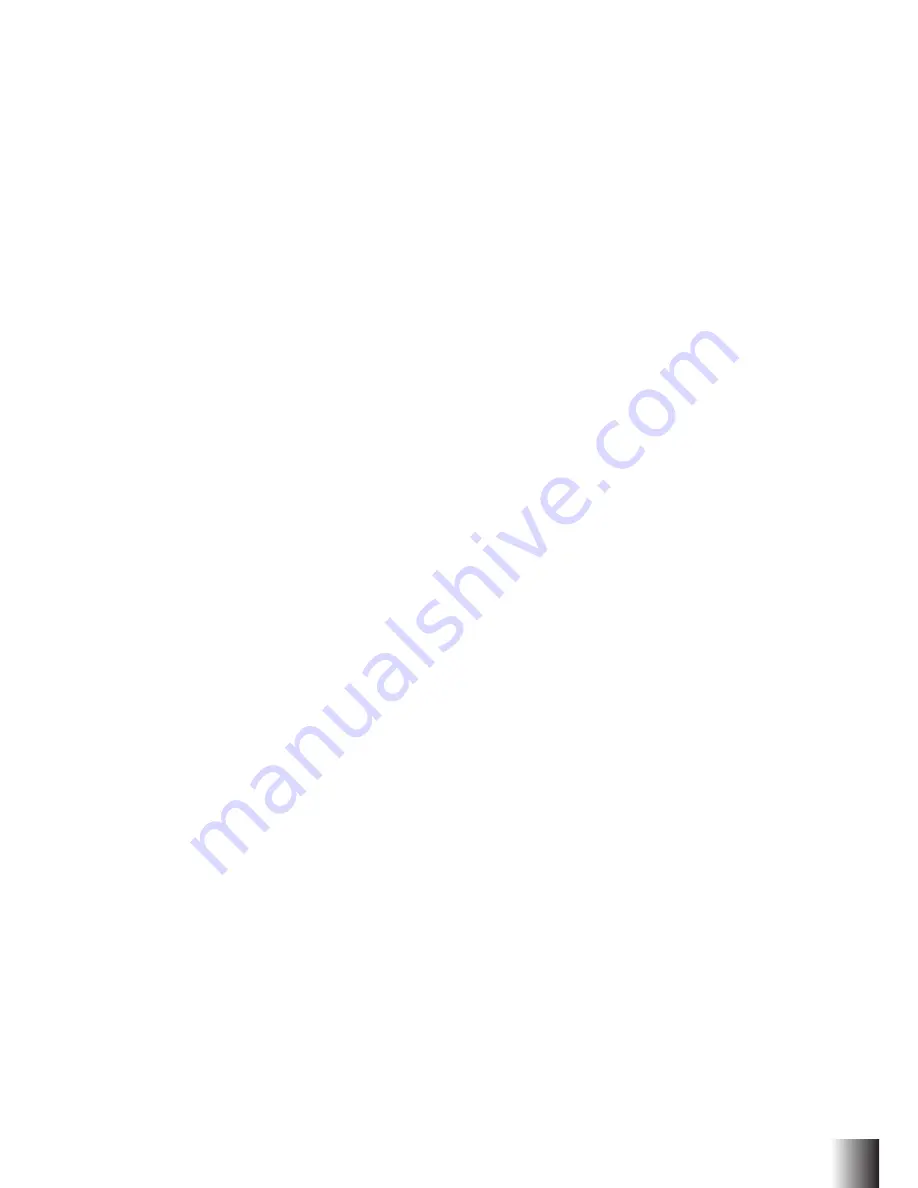
NOTE:
it may be necessary to cool the PremierPlus SystemFit down to allow the indirect thermostat to call for heat, it
may also be necessary to increase the required room temperature setting if the room temperature has already reached
that programmed. The pump should run and the boiler fire (both a tap symbol and a flame symbol should appear in the
controller display). The primary flow to the Premier Plus SystemFit and the radiator circuit should become hot. If it does
not, check for a wiring or piping error.
When the heating and hot water temperatures are reached, the 2-port motorised valves should close, the pump stops
running and the boiler stops firing.
NOTE:
If a pump over-run boiler is fitted, the pump may continue to run for a short
time after the boiler has shut down.
Check that no water is discharged from either the expansion valve or temperature and pressure relief valve during the heating
cycle. If the user temperatures or “On” and “Off” times have been adjusted for commissioning purposes, the controller
should be reset to the desired settings. The operation of the controller should be demonstrated to the user and the controller
installation and user instructions left with them for future reference.
AUTOMATIC SYSTEM BY-PASS
An automatic differential bypass valve is fitted to the PremierPlus SystemFit. This has been factory set to an optimum position
for most domestic heating systems. However, in some systems it may require further adjustment. To do this:
Turn the adjustment spindle fully clockwise such that the 0.5 marking is level with the top of the valve body.
Turn on the system and set the controller to heating only. Balance the system in the normal manner.
With the boiler firing and the pump running, slowly turn the adjustment knob anti-clockwise until hot water can be felt on
the outlet side of the bypass valve. Turn the adjustment knob clockwise by half a turn.
MAINTENANCE
MAINTENANCE REQUIREMENTS
Unvented hot water systems have a continuing maintenance requirement in order to ensure safe working and optimum
performance. It is essential that the relief valve(s) are periodically inspected and manually opened to ensure no blockage
has occurred in the valves or discharge pipework. Similarly cleaning of the strainer element and replacement of the air in
the expansion vessel will help to prevent possible operational faults.
The maintenance checks described below should be performed by a competent person on a regular basis, e.g. annually to
coincide with boiler maintenance.
After any maintenance, please complete the relevant service interval record section of the Benchmark Checklist on page 27
of this document.
INSPECTION
The immersion heater boss can be used as an access for inspecting the cylinder internally.
SAFETY VALVE OPERATION
Manually operate the temperature/pressure relief valve for a few seconds. Check water is discharged and that it flows freely
through the tundish and discharge pipework. Check valve reseats correctly when released.
NOTE:
Water discharged may
be very hot!
Repeat the above procedure for the expansion relief valve.
STRAINER
Turn off the cold water supply, boiler and immersion heaters. The lowest hot water tap should then be opened to de-pressurise
the system. Remove the pressure reducing cartridge to access the strainer mesh. Wash any particulate matter from the strainer
under clean water. Re-assemble ensuring the seal is correctly fitted. DO NOT use any other type of sealant.
DESCALING IMMERSION HEATER(S)
Before removing the immersion heater(s), the unit must be drained. Ensure the water, electrical supply and boiler are OFF before
draining. Attach a hosepipe to the drain cock having sufficient length to take water to a suitable discharge point below the
level of the unit. Open a hot tap close to the unit and open the drain cock to drain the unit.
Summary of Contents for PremierPlus SystemFit
Page 1: ...PremierPlus SystemFit Unvented Indirect Hot Water Cylinder Installation and User Manual...
Page 26: ...25...
Page 27: ...26...