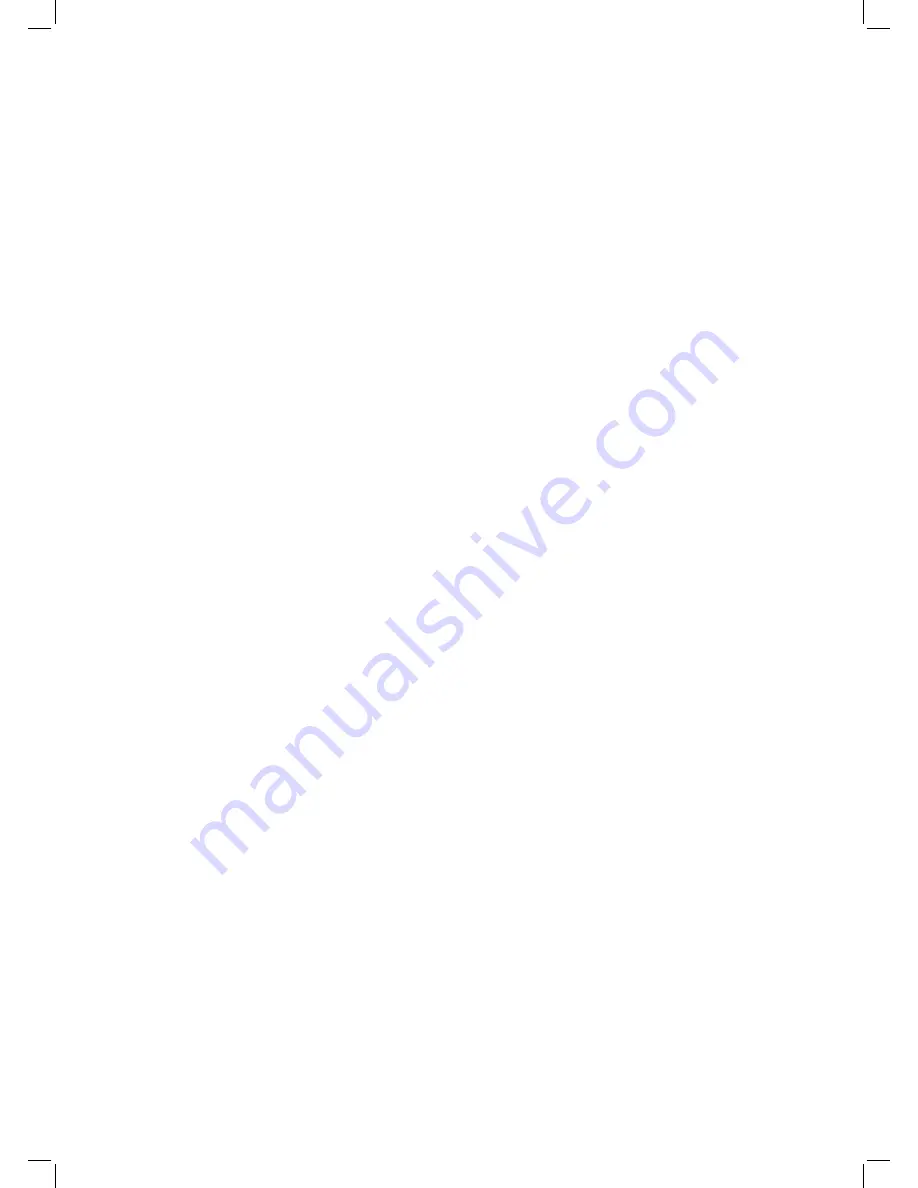
17
8.0 COMMISSIONING
The boiler controls are fully automatic, making the operation very simple.
Only after the system has been flushed through and then filled with water inhibitor and set to the correct pressure
(sealed systems), can the electrical supply be switched on.
Check 1.
When filling the system check for leaks. The warranty will be invalidated if water leaks into the
boiler. Ensure the joints above the boiler are sound.
Check 2.
Before switching on the mains supply, check the main electrical power connections are tight.
Support the back of the PCB behind the power terminals when tightening the main power
terminals. Loose connections can cause a fire.
Initial set up procedure: - (See figure. 13, page.18)
1. Ensure the main electrical supply and the programmer controls to the boiler are off and isolated.
2. Remove the pump live and neutral connection from the control terminal block in the boiler, and
reconnect the pump live wire into the control terminal ‘R’ together with the control signal wire.
Connect the pump neutral wire into the control terminal ‘N’ together with the control neutral wire.
3. Unplug the control block from the main PCB, ensure it is safe and not touching anything. The pump
is now fed from the control signal.
4. Check all air is purged from the system and set the pump to maximum.
5. Switch on the control supply only (3 amp or 6 amp) MCB.
6. With the programmer and room thermostat on, check the pump is running and water is flowing.
Ensure the whole system, valves etc. are operating correctly. Continue to run the pump for some
time to purge any air. Don’t forget to bleed the pump.
7. Switch off the main supply RCD and MCB’s. Ensure it is all safe before reconnecting the pump
connections to the pump terminals as was originally wired. Reconnect the control terminal block
onto the PCB. Check all connections are made correctly, check the main supply terminals in the
boiler are tight, close and secure the top front cover of the boiler.
Main test procedure: -
Only after a satisfactory initial test, proceed as follows; -
1. Switch on the main boiler MCB.
Switch on the programmer “control” (3 amp or 6 amp) MCB.
Switch on the RCD unit / isolation switch.
Check the boiler front panel SUPPLY indicator is illuminated (green).
2. Set the programmer for central heating to ON.
Set the room thermostat to be ON.
The boiler front panel CALL indicator will flash (green).
This indicator will illuminate as a steady green after approximately 2-3 minutes.
Following the steady green, the HEAT indicator will build up gradually.
3. Check the temperature of the FLOW pipework from the boiler. This pipework should start to rise
in temperature. The rate of rise will depend upon the size of the boiler and system.
4. Check the full system operates correctly. If at any time the temperature difference between the
boiler return and flow is greater than 14
0
C, then there is a flow restriction problem and must be
rectified immediately. Set pump speed to give 5
0
C-10
0
C differential between return and flow on
the boiler when operating at maximum power output. The heat may be seen to modulate if the
temperature rise is to quick.