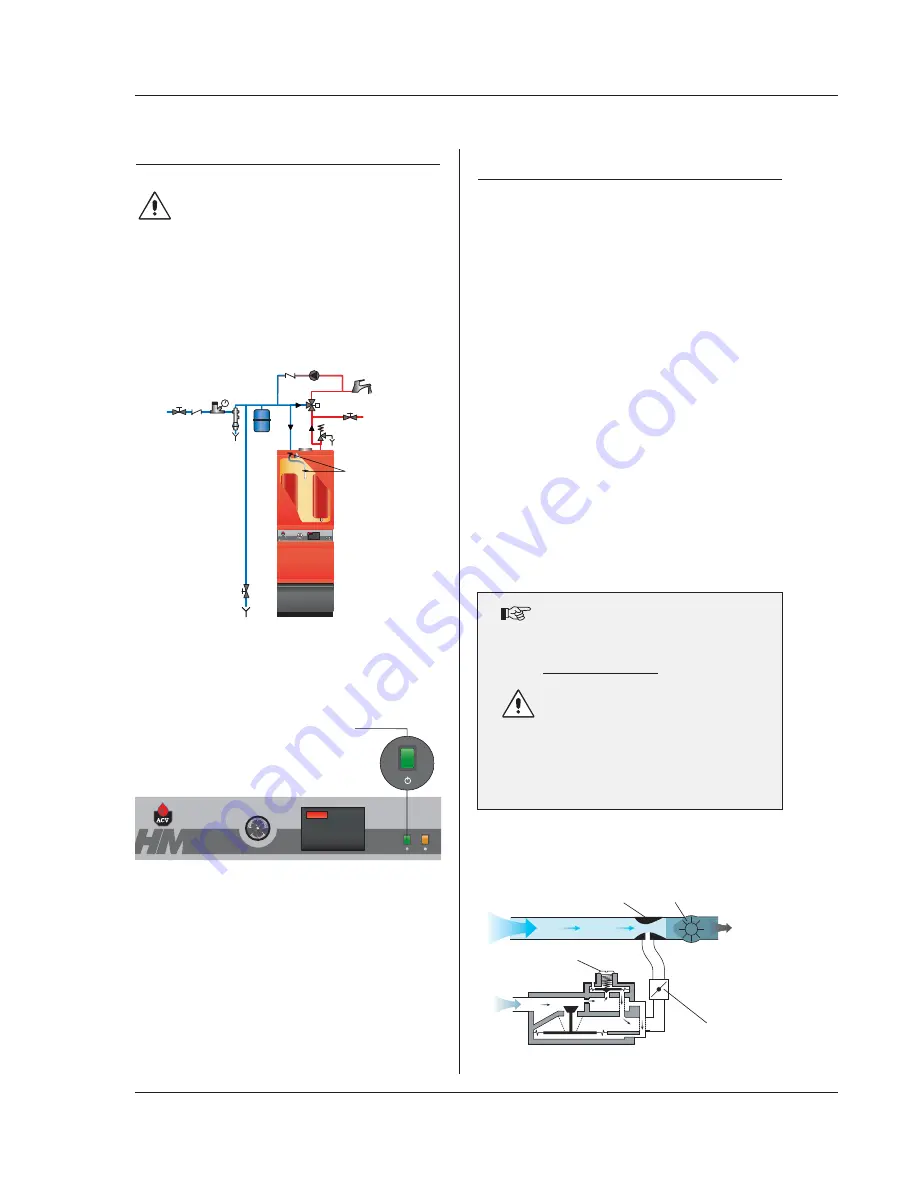
12
COMMISSIONING
FILLING THE HOT WATER AND HEATING CIRCUITS
IMPORTANT
The hot water tank must be pressurised before the
heating circuit is filled.
1.
Close the primary circuit filling valves (11).
2.
Open the stop valve (1) and the drawoff tap (8).
When water flows out of the tap, the hot water tank is full and
the drawoff tap (8) should be closed.
3.
Fill the primary (heating) circuit by opening the valves (11) and
pressurising to 1 bar.
4.
Open the automatic air vent located on top of the boiler.
IMPORTANT - the screw cap must be left loose to allow future
automatic venting to take place.
5.
After venting the air from the system, bring the pressure up to
the static head plus 0.5 bar: 1.5 bar = 10m and 2 bar = 15 m.
6.
Check that the electrical connection and boiler room ventilation
conform to the relevant standards.
7.
Switch the on/off switch to the ON position.
8.
Set the temperature settings
(see pages 15-16)
.
9.
Check the gas supply pressure
(see page 13)
.
10. When the burner operates, check the chimney connection for
leaks.
11. After 5 minutes of operation, turn the boiler off and vent the heating
circuit system again maintaining the water pressure at 1 bar.
12. Then restart the unit and check the combustion
(see page 13)
.
Burner troubleshooting
See page 15-17
Spare parts
Refer to the specific document available from ACV or your distributor.
ACV BG 2000-M MODULATING
PREMIX GAS BURNERS
Description of operation:
The BG 2000-M modulating burner continually adjusts output to
demand, improving operating efficiency.
The burner tube is coated with metal fibre (NIT) which, in addition to
its remarkable heat exchange capabilities, gives greater durability.
The main components are a venturi and one (model 71) or two
(model 101) gas valves, technology specially developed by
Honeywell for low Nox premix air/gas burners with automatic ignition
and ionisation flame detection.
The pressure at the gas valve outlet is equal to the air pressure in
the neck of the venturi, less the offset. The fan sucks combustion air
through the venturi, into which the gas inlet emerges.
As it passes through, the air produces a pressure differential in the
constriction of the venturi and sucks the gas into the venturi outlet.
A perfect mix of air and gas then passes through the fan to the
burner tube.
This design ensures very quiet and safe operation:
•
If there is an air blockage, the pressure differential in the venturi
falls, the gas flow diminshes, the flame goes out and the gas
valve closes: the burner is in safety shutdown mode.
•
If there is a blockage in the chimney outlet, the air flow diminishes,
and the same reactions as those described above cause the
burner to shut down in safety mode.
•
The BG 2000-M burner fitted to the HeatMaster 71 and 101 is
regulated by a MCBA controller (Honeywell) which controls burner
operating safety as well as temperature modulation.
BG 2000-M burners are preset at the factory
for natural gas.
Conversion to propane:
Not applicable for Belgium.
Conversion kit included with burner comprising:
- Cap(s)
- Nameplate(s)
- Sticker with settings.
- Mounting instructions.
Air-gas mixture control system
1
2
3
4
5
2
6
7
8
9
10
12
11
Air
Venturi
Fan
Air - gas
mixture
Gas flow
regulating screw
Offset regulation
screw
Gas
BURNER FEATURES