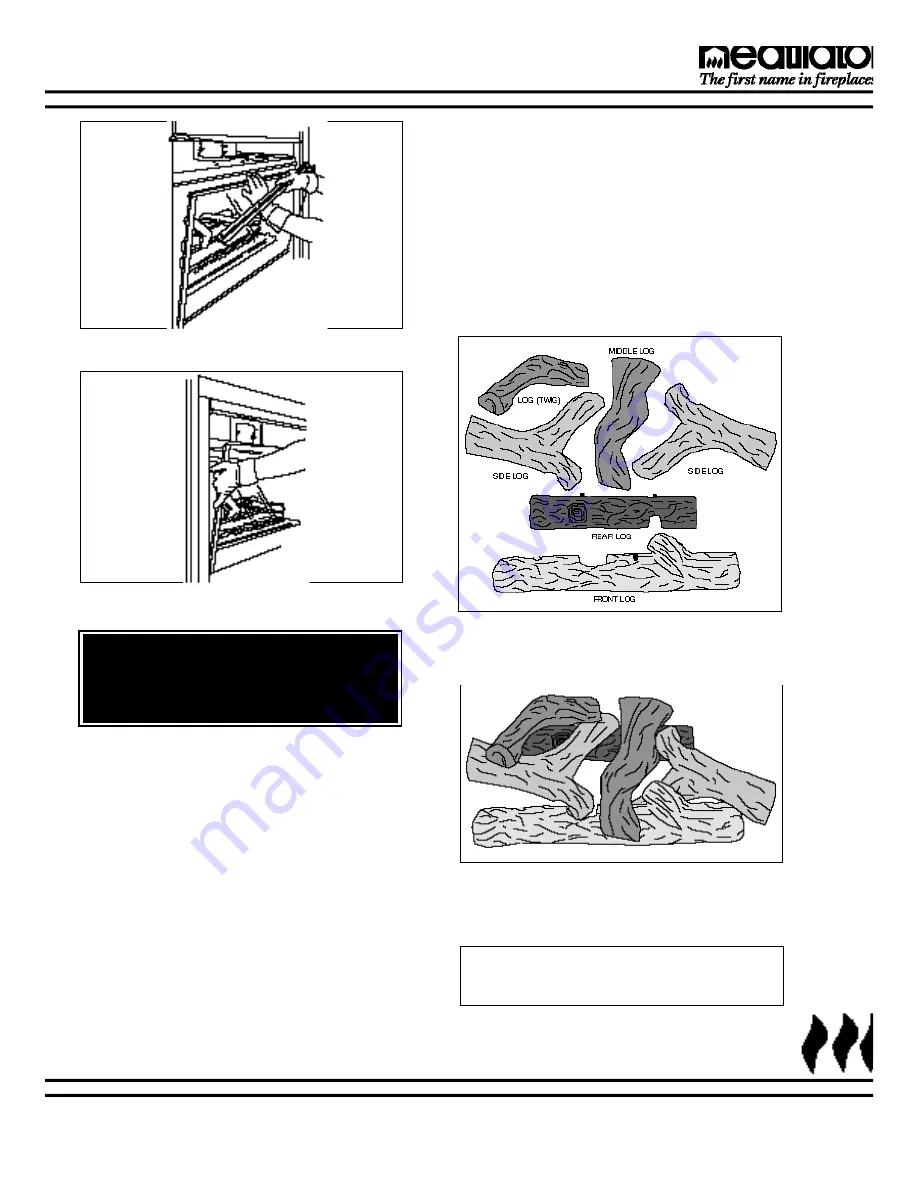
12-98
17
21322K
GC150 SERIES DIRECT VENT GAS APPLIANCE
STEP 12 - Positioning the Logs
Open carton labeled #21442 and remove the logs
carefully , laying them out as shown in Figure 27.
Please note that Figure 27 is the orientation for the
logs within the firebox. At this point inspect the logs
for any damage.
Begin positioning the logs into the firebox by first plac
-ing the Rear Log on the rear log support(at the back
of the firebox ) with the pins to the top and the indent
to the lower right hand side (as you look at it). Next,
place the Front Log behind (on top of supports) the
burner tube (the portion closest to the front of the fire-
box).
The right Side Log should be positioned between the
Rear and Front Logs with the short portion of the “Y”
up and leaning towards the pilot/ignitor and the indent
on the Rear Log. The Middle Log is positioned next
and is placed across the Rear and Front Logs. On
the upper back of the Middle Log is a pin cavity which
is placed on the right hand pin of the Rear Log.
Figure 25
Glass Removal
Figure 26
Glass Removal
Figure 28
Positioning the Logs
Figure 27
Arranging the Logs
Note: The shading of the logs in this instal-
lation manual is for definition only. It does
not represent the actual color of the logs
The left Side Log is placed with the short portion of
the “Y” into the indent on the Front Log. The long
portion of the “Y” leans against the Rear Log and the
leg portion of the Side Log is placed on the side log
support (located on the left hand side of the firebox).
The last log to be placed is the Log(Twig). It has a
pin cavity in the upper back portion and is placed on
the left pin on the Rear Log. The long portion of the
Log(Twig) rests on the left Side Log.
WARNING!
DO NOT OPERATE THIS APPLIANCE IF
THE GLASS IS BROKEN OR CRACKED.