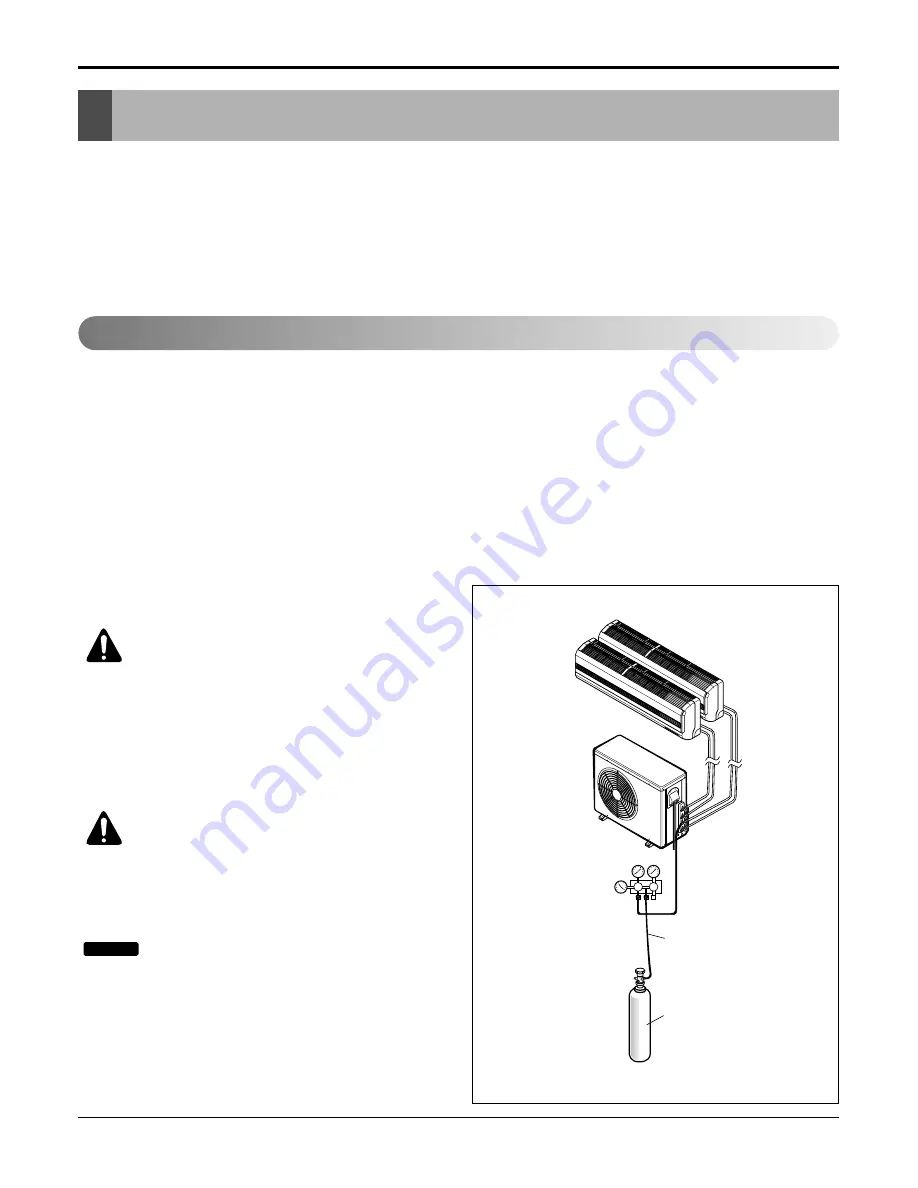
Service Manual 31
Air Purging and Evacuation
Air Purging and Evacuation
Air and moisture remaining in the refrigerant system have undesirable effects as indicated below.
1. Pressure in the system rises.
2. Operating current rises.
3. Cooling(or heating) efficiency drops.
4. Moisture in the refrigerant circuit may freeze and block capillary tubing.
5. Water may lead to corrosion of parts in the refrigeration system.
Therefore, the indoor/outdoor unit and connecting tube must be checked for leak tight, and vacuumed to remove
incondensible gas and moisture in the system.
Preparation
• Check that each tube(both liquid and gas side tubes)
between the indoor and outdoor units have been properly
connected and all wiring for the test run has been complet-
ed. Remove the service valve caps from both the gas and
the liquid side on the outdoor unit. Check that both the liq-
uid and the gas side service valves on the outdoor unit are
kept closed at this stage.
Leakage test
• Connect the manifold valve(with pressure gauges) and dry
nitrogen gas cylinder to this service port with charge
hoses.
CAUTION: Be sure to use a manifold
valve for leak testing.
The high side manifold valve must always
be kept closed.
• Pressurize the system to no more than 150 P.S.I.G.
with dry nitrogen gas and close the cylinder valve
when the gauge reading reached 150 P.S.I.G. Next,
test for leaks with liquid soap.
CAUTION: To avoid nitrogen entering the
refrigerant system in a liquid state, the top
of the cylinder must be higher than its bottom
when you pressurize the system. Usually, the
cylinder is used in a vertical standing position.
: Leakage test shoud be done for each
indoor unit connection set, separately.
1. Do a leakage test of all joints of the tubing(both
indoor and outdoor) and both gas and liquid side ser-
vice valves.
Bubbles indicate a leak. Be sure to wipe off the soap
with a clean cloth.
2. After the system is found to be free of leaks, relieve
the nitrogen pressure by loosening the charge hose
connector at the nitrogen cylinder. When the system
pressure is reduced to normal, disconnect the hose
from the cylinder.
NOTICE
Checking method
Charge hose
Nitrogen gas
cylinder(in vertical
standing position)
Indoor unit
Outdoor unit
Lo
Hi
Manifold valve
Pressure
gauge
Summary of Contents for DMH18DB-1
Page 49: ...Service Manual 49 1 Room Type Indoor Unit Wiring Diagram Schematic Diagram 2 Outdoor Unit...
Page 51: ...Service Manual 51 Schematic Diagram 2 Display ASSEMBLY 1 Split Type 6871A20682A...
Page 52: ...52 Multi type Air Conditioner Schematic Diagram 3 Outdoor Unit 1 Component side...
Page 53: ...Service Manual 53 Schematic Diagram 2 Solder side...