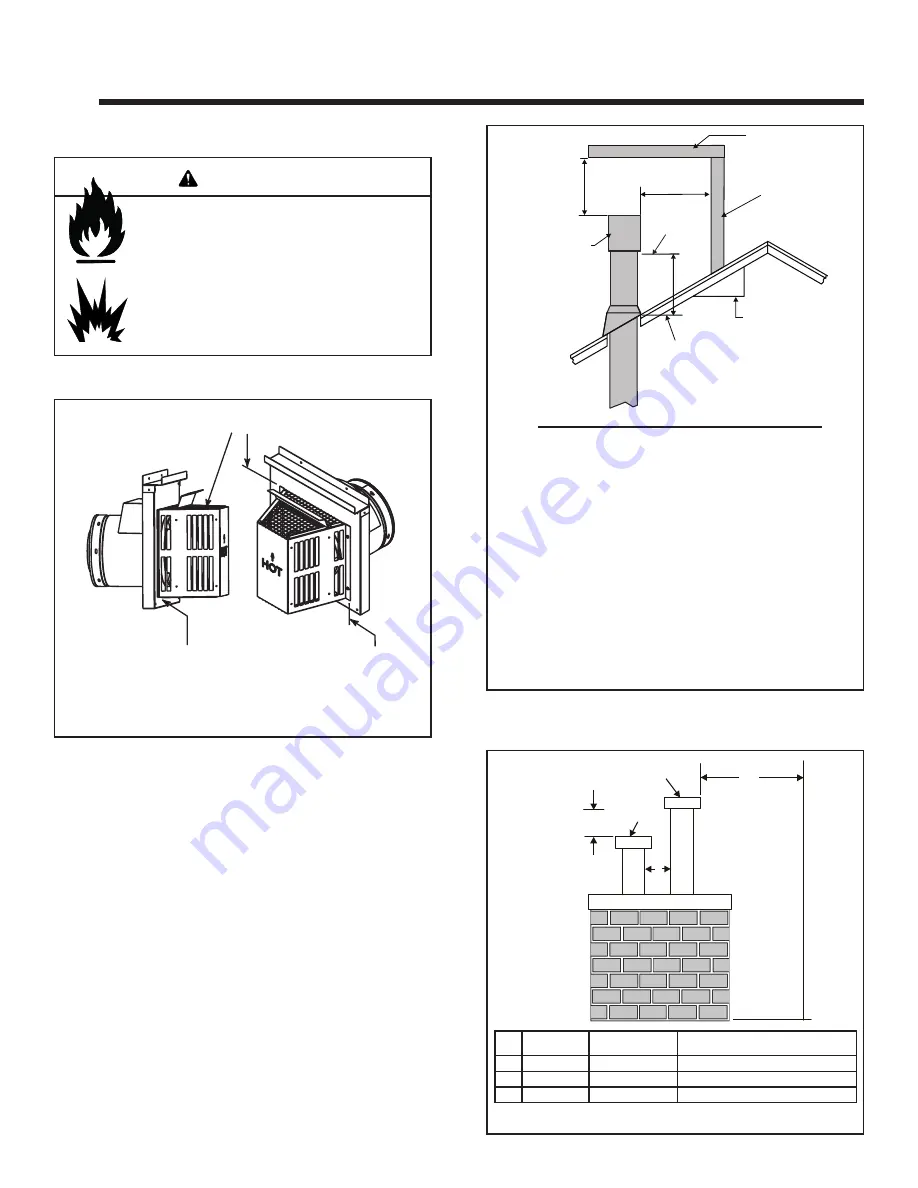
Heat & Glo • Paloma • 7031-220 Rev. P • 10/08
9
A. Vent Termination Minimum Clearances
Fire Risk.
Explosion Risk.
Maintain vent clearance to combustibles as
specifi ed.
• Do not pack air space with insulation or other
materials.
Failure to keep insulation or other materials
away from vent pipe may cause fi re.
Figure 4.1
4
4
Termination Locations
Measure horizontal clearances from this surface.
Measure vertical clearances from this surface.
(See Figure 4.4 for specifi c clearances)
WARNING
Roof Pitch
H (Min.) Ft.
Flat to 6/12...........................................................1.0*
Over 6/12 to 7/12 .................................................1.25*
Over 7/12 to 8/12 .................................................1.5*
Over 8/12 to 9/12 .................................................2.0*
Over 9/12 to 10/12 ...............................................2.5
Over 10/12 to 11/12 .............................................3.25
Over 11/12 to 12/12 .............................................4.0
Over 12/12 to 14/12 .............................................5.0
Over 14/12 to 16/12 .............................................6.0
Over 16/12 to 18/12 .............................................7.0
Over 18/12 to 20/12 .............................................7.5
Over 20/12 to 21/12 .............................................8.0
Figure 4.2 Minimum height from roof to lowest discharge
opening
Figure 4.3 Multiple Vertical Termination
Figure 4.2 specifi es minimum vent heights for various
pitched roofs.
* 3 foot minimum in snow regions
HORIZONTAL
OVERHANG
VERTICAL
WALL
GAS DIRECT VENT
TERMINATION CAP
12
X
ROOF PITCH
IS X/ 12
LOWEST
DISCHARGE
OPENING
2 FT.
MIN.
20 INCHES MIN.
H (MIN.) - MINIMUM HEIGHT FROM ROOF
TO LOWEST DISCHARGE OPENING
C
A
GAS
TERMINATION
B
GAS, WOOD OR FUEL
OIL TERMINATION
Gas
Termination
Wood & Fuel Oil
Termination
Comments
A
6 in.
20 in. min.
Horizontal distance between terminations
B
20 in.
24 in. min.
Distance to perpendicular wall
C
18 in.
18 in.
Vertical distance between terminations