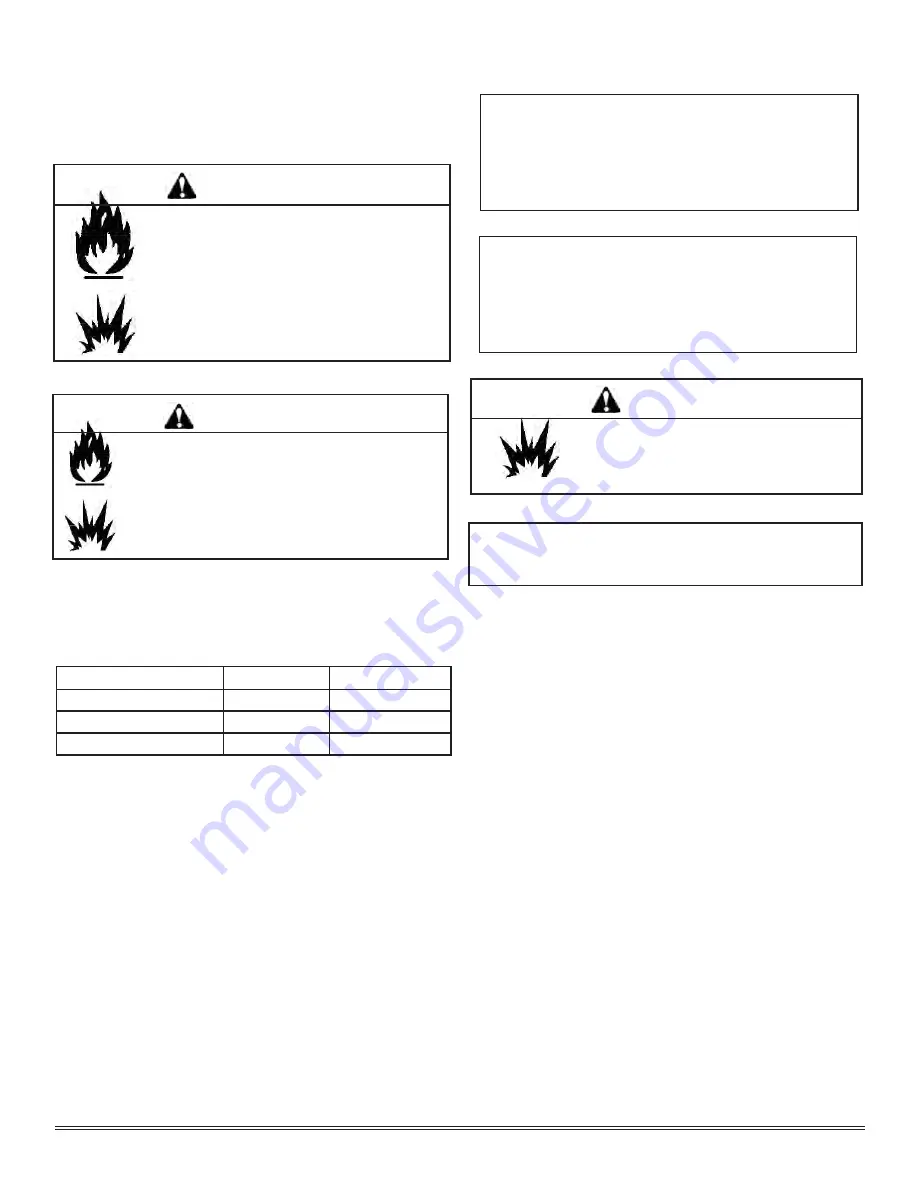
Page 24
July 12, 2006
Heat & Glo · Mission Bay · 250-7512F
B. Gas Pressures
If the pressure is not sufficient, ensure:
1) the piping used is large enough.
2) the supply regulator is adequately adjusted.
3) that the total gas load for the residence does not exceed
the amount supplied.
The supply regulator (the regulator that attaches directly to the
residence inlet or to the propane tank) should supply gas at
the suggested input pressure listed above. Contact the local
gas supplier if the regulator is at an improper pressure.
Pressure requirements for appliance are shown in the table
below. Minimum pressures must be met when other house-
hold gas appliances are operating.
Proper input pressures required for optimum appliance per-
formance, gas line sizing requirements need to be followed
from NFPA51.
WARNING
Fire Risk.
Explosion Hazard.
High pressure will damage valve.
• Disconnect gas supply piping BEFORE
pressure testing gas line at test pressures
above 1/2 psig.
• Close the manual shutoff valve BEFORE
pressure testing gas line at test pressures
equal to or less than 1/2 psig.
PRESSURE
NG
LP
Minimum Inlet Pressure
5 inches w.c.
11 inches w.c.
Maximum Inlet Pressure
7 inches w.c.
14 inches w.c.
Manifold Pressure on “HI” 3.5 inches w.c.
10 inches w.c.
WARNING
Verify inlet pressures.
• High pressure may cause overfire condition.
• Low pressure may cause explosion.
• Verify minimum pressures when other household
gas appliances are operating.
Install regulator upstream of valve if line pressure is
greater than 1/2 psig.
NOTE:
A listed (and Commonwealth of Massachusetts
approved) 1/2 inch (13mm) T-handle manual shut-off valve and
flexible gas connector are connected to the 1/2 inch (13mm)
control valve inlet.
• If substituting for these components, please consult
local codes for compliance.
NOTE:
The gap between the supply piping and gas access
hole may be plugged with non-combustible insulation to prevent
cold air infiltration.
C. Gas Connection
NOTE:
Have the gas supply line installed in accordance with
local building codes, if any. If not, follow ANSI Z223.1. Instal-
lation should be done by a qualified installer approved and/or
licensed as required by the locality. (In the Commonwealth of
Massachusetts, installation must be performed by a licensed
plumber or gas fitter.)
Leak test all gas line joints and the gas control valve prior
to and after starting the appliance.
Before making the gas connection, ensure that the appliance
you are installing is designed for the type of gas being
supplied. This information can be found on the ratings label
under the appliance. If the appliance has been converted
to propane (LP), the valve cover should have a label stating
that the appliance has been converted to propane.
Connect the gas line at the 3/8 in. (10mm) pipe connector
on the valve at the back of appliance.
We recommend
connecting the appliance with an approved flex gas line.
If flex gas lines are not approved in your area, you must
connect a hard pipe to the gas hookup.
You must supply a manual shut-off valve in a visible location
within 3 ft. (914mm) of the appliance.
WARNING
Gas Leak Risk.
• Support control when attaching pipe to
prevent bending gas line.