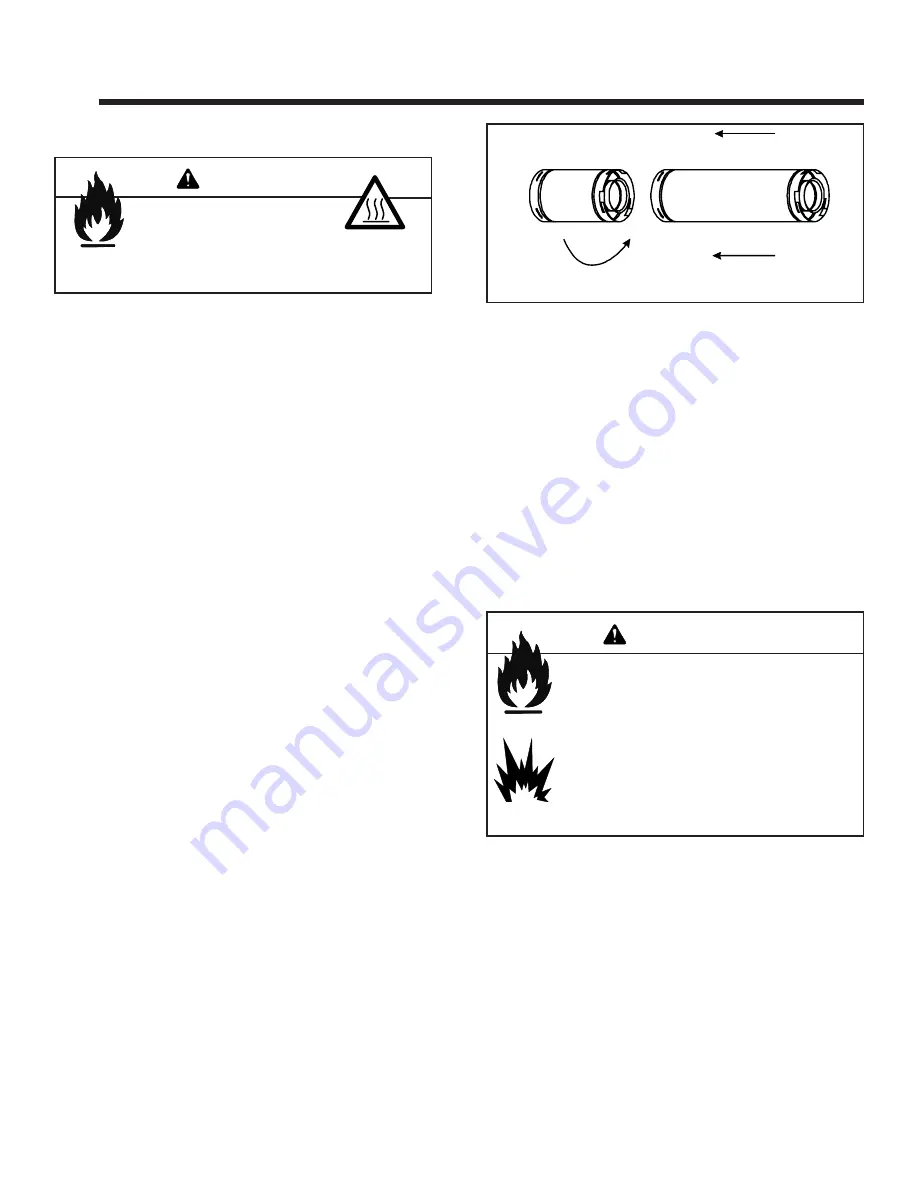
Heat & Glo • Soho-CE • 2111-900 Rev. D • 6/07
18
8
8
Installing Flue Pipe
Figure 8.1 Adding Flue Components
Install Support Brackets
For Horizontal Runs -
The fl ue system must be supported
every 1.5 meters of horizontal run by a horizontal pipe
support.
To install support brackets for horizontal runs:
• Place the pipe supports around the fl ue pipe.
• Nail the pipe supports to the framing members.
For Vertical Runs -
The fl ue system must be supported
every 2.4 meters above the appliance fl ue outlet by wall
brackets. To install support brackets for vertical runs:
• Attach wall brackets to the fl ue pipe and secure the wall
bracket to the framing members with nails or screws.
Attach the First Flue Component to Starting Collars
To attach the fi rst fl ue component to the starting collars
of the appliance:
• Lock the flue components into place by sliding the
concentric pipe sections with four (4) equally spaced
interior beads into the appliance collar or previously
installed component end with four (4) equally spaced
indented sections.
• When the internal beads of each outer pipe line up, rotate
the pipe section clockwise about one-quarter (1/4) turn
(see Figure 8.1). The fl ue pipe is now locked together.
• Slide the ceramic rope ring over the fi rst fl ue section and
place it fl ush to the appliance. This will prevent cold air
infi ltration. High temp caulk may be used to hold the part
in place. Continue to add fl ue components.
Continue Adding Flue Components
• Continue adding flue components, locking each
succeeding component into place.
• Ensure that each succeeding fl ue component is securely
fi tted and locked into the preceding component.
• 90° elbows may be installed and rotated to any point
around the preceding component’s vertical axis. If an
elbow does not end up in a locked position with the
preceding component, attach with a minimum of two (2)
sheet metal screws.
Fire Risk
Exhaust Fumes Risk
Impaired Performance of Appliance
• Ensure fl ue components are locked together correctly.
• Pipe may separate if not properly joined.
Fire Risk.
Explosion Risk.
Combustion Fume Risk.
Use fl ue run supports per installation instructions.
Connect fl ue sections per installation instructions.
• Maintain all clearances to combustibles.
• Do NOT allow fl ue to sag below connection point
to appliance.
Improper support may allow fl ue to sag or separate.
A. Assembly of Flue Sections
WARNING
WARNING