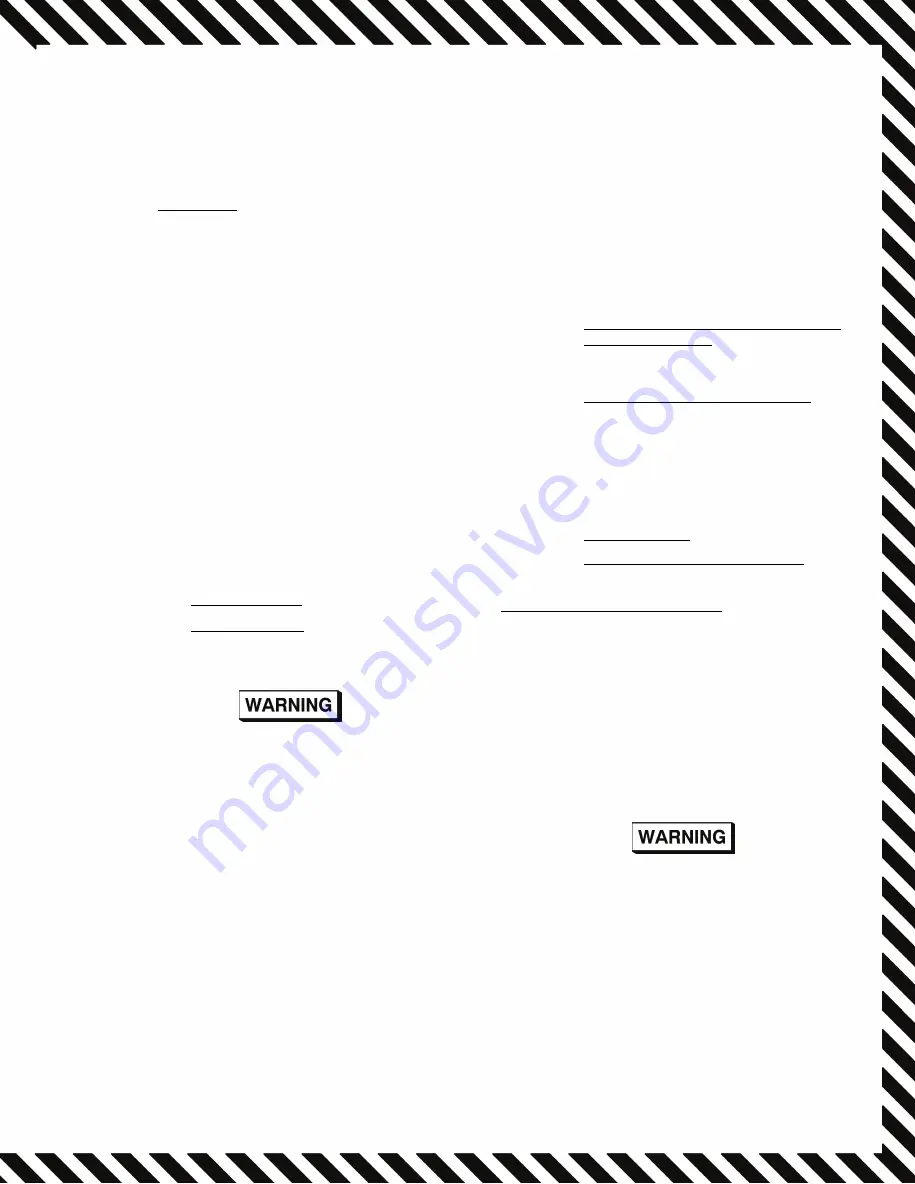
(1)
Varying degrees of right yaw depending on
power applied and airspeed at time of failure.
(2)
Forward CG shift.
b. Procedure:
(1)
Enter autorotative descent (power off).
(2)
Maintain airspeed above minimum rate of
descent airspeed.
(3)
If run-on landing is possible, complete au-
torotation with a touchdown airspeed above effective
translational lift.
(4)
If run-on landing is not possible, start to
decelerate from about 75 feet altitude, so that forward
groundspeed is at a minimum when the helicopter
reaches 10 to 20 feet; execute the touchdown with a
rapid collective pull just prior to touchdown in a level
attitude with minimum ground run.
9-22. LOSS OF TAIL ROTOR EFFECTIVENESS
(LTE).
This is a situation involving a loss of effective
tail rotor thrust without a break in the drive system which
cannot be stopped with full left pedal application. If LTE
is experienced, simultaneously:
1. Pedal - Full Left.
2. Cyclic - Forward.
3. As recovery is effected, adjust controls for
normal
fl
ight.
Collective reduction will aid In arresting the yaw
rate; however, if a rate of descent has been es-
tablished, collective reduction may increase the
rate of descent to an excessive value. The re-
sultant large and rapid Increase in collective to
prevent ground or obstacle contact may further
increase the yaw rate, decrease the rotor RPM
and cause an overtorque and/or over-temper-
ature condition. Therefore, the decision to re-
duce collective must be based on the pilot as-
sessment of the altitude available for recovery.
If spin cannot be stopped and crash is imminent, an au-
torotation may be the best course of action. Maintain
full left pedal until the spin stops, then adjust to maintain
heading.
9-23. MAIN DRIVESHAFT FAILURE.
A failure of the
main driveshaft will be indicated by a sudden increase
in engine RPM, decrease in rotor RPM, left yaw and
activation of the low RPM audio, and illumination of the
ROTOR RPM warning light. A transient overspeed of
N1 and N2 may occur but will stabilize. In the event of
main driveshaft failure:
1. AUTOROTATE - Establish a power-on
autorotational glide. The engine must
continue to operate at normal operating
RPM in order to provide tail rotor control.
2. EMER SHUTDOWN after landing.
9-24. CLUTCH FAILS TO DISENGAGE.
A clutch
failing to disengage in
fl
ight will be indicated by the
rotor RPM decaying with engine RPM as the throttle
is reduced to the engine idle position when entering
autorotational descent. This condition results in total
loss of autorotational capability. If a failure occurs:
1. Throttle - Open.
2. LAND AS SOON AS POSSIBLE.
9-25. MAST BUMPING.
LAND AS SOON AS POSSIBLE.
9-26. FIRE.
The safety of helicopter occupants is the
primary consideration when a
fi
re occurs; therefore, it is
imperative that every effort be made by the
fl
ight crew
to put the
fi
re out. On the ground, it is essential that the
engine be shut down, crew and passengers evacuated
and
fi
re
fi
ghting begun immediately. If time permits, a
"MAYDAY" radio call should be made before the electri-
cal power is off to expedite assistance from
fi
re
fi
ghting
equipment and personnel. If the helicopter is airborne
when a
fi
re occurs, the most important single action that
can be taken by the pilot is to land the helicopter.
Toxic fumes of the extinguishing agent may
cause injury, and liquid agent may cause frost-
bite or low temperature burns.
Change 14 9-9
TM 55-1520-228-10
Summary of Contents for OH-58A
Page 2: ......
Page 5: ......
Page 6: ......
Page 10: ......
Page 12: ......
Page 18: ......
Page 19: ......
Page 20: ......
Page 21: ......
Page 22: ......
Page 23: ......
Page 24: ......
Page 26: ......
Page 28: ......
Page 30: ......
Page 32: ......
Page 34: ......
Page 53: ...TM 55 1520 228 10 Change 13 2 11 Figure 2 5 Principal Dimensions Sheet 1 of 2 ...
Page 56: ...TM 55 1520 228 10 Figure 2 7 Float Gear Equipped Helicopter 2 14 ...
Page 57: ...TM 55 1520 228 10 Figure 2 8 Locking Devices for Doors 2 15 ...
Page 59: ...TM 55 1520 228 10 2 17 Figure 2 9 WSPS Configuration ...
Page 61: ...TM 55 1520 228 10 Change 11 2 19 FIGURE 2 10 HAS BEEN DELETED ...
Page 62: ...TM 55 1520 228 10 2 20 Change 11 Figure 2 11 Engine ...
Page 64: ...TM 55 1520 228 10 Figure 2 12 Overhead Console 2 22 Change 10 ...
Page 66: ......
Page 69: ...TM 55 1520 228 10 2 25 Figure 2 13 Instrument Panel and Console Typical A ...
Page 70: ...TM 55 1520 228 10 2 26 Change 11 Figure 2 14 Instrument Panel and Console Typical C ...
Page 75: ...TM 55 1520 228 10 Figure 2 15 Auxiliary Fuel System 2 29 ...
Page 84: ...TM 55 1520 228 10 Figure 2 17 Heater Control and Vent Pull Knobs 2 38 Change 12 ...
Page 92: ...TM 55 1520 228 10 Figure 2 18 1 AAU 32 A Altitude Encode Pneumatic Altimeter 2 46 Change 4 ...
Page 95: ...TM 55 1520 228 10 Change 11 2 47 Figure 2 19 Warning and Caution Panels ...
Page 98: ...TM 55 1520 228 10 Figure 2 20 Servicing Diagram Sheet 2of 2 2 50 Change 11 ...
Page 107: ...TM 55 1520 228 10 Figure 2 22 Gravity Refueling With Closed Circuit Receiver 2 59 ...
Page 109: ...TM 55 1520 228 10 Change 11 2 61 Figure 2 23 Refueling Receptacle ...
Page 116: ......
Page 133: ...TM 55 1520 228 10 Change 11 3 13 FIGURE 3 7 HAS BEEN DELETED ...
Page 146: ......
Page 152: ...TM 55 1520 228 10 FIGURE 3 15 HAS BEEN DELETED 3 30 Change 10 ...
Page 157: ...TM 55 1520 228 10 3 32 3 ...
Page 164: ......
Page 166: ......
Page 168: ...TM 55 1520 228 10 Figure 5 1 Instrument Markings A 5 2 Change 11 ...
Page 169: ......
Page 170: ...TM 55 1520 228 10 Figure 5 2 Instrument Markings Sheet 1 of 3 5 3 blank 5 4 Change 14 ...
Page 171: ...TM 55 1520 228 10 Change 11 5 5 Figure 5 2 Instrument Markings Sheet 2 of 3 ...
Page 175: ...TM 55 1520 228 10 Change 11 5 9 T63 A 720 Figure 5 3 Airspeed Operating Limits Chart ...
Page 182: ...TM 55 1520 228 10 6 4 Change 10 Figure 6 3 Cargo Space ...
Page 183: ...TM 55 1520 228 10 Change 11 6 5 Figure 6 4 Fuel Loading Chart ...
Page 184: ...TM 55 1520 228 10 6 6 Figure 6 5 Personnel Loading ...
Page 186: ......
Page 187: ......
Page 188: ......
Page 190: ......
Page 204: ...TM 55 1520 228 10 Figure 7 12 Torque Available Continuous Operation Chart Sheet 1 of 4 7 52 ...
Page 205: ...TM 55 1520 228 10 Figure 7 12 Torque Available Continuous Operation Chart Sheet 2 of 4 7 53 ...
Page 206: ...TM 55 1520 228 10 Figure 7 12 Torque Available Continuous Operation Chart Sheet 3 of 4 7 54 ...
Page 209: ......
Page 210: ......
Page 211: ...TM 55 1520 228 10 Change 10 7 59 Figure 7 13 Hover Chart Sheet 3 of 3 ...
Page 213: ......
Page 215: ...TM 55 1520 228 10 Figure 7 15 Cruise Chart Sheet 1 of 13 7 63 ...
Page 216: ...TM 55 1520 228 10 Figure 7 15 Cruise Chart Sheet 2 of 13 7 64 ...
Page 217: ...TM 55 1520 228 10 Figure 7 15 Cruise Chart Sheet 3 of 13 7 65 ...
Page 218: ...TM 55 1520 228 10 Figure 7 15 Cruise Chart Sheet 4 of 13 7 66 ...
Page 219: ...TM 55 1520 228 10 Figure 7 15 Cruise Chart Sheet 5 of 13 7 67 ...
Page 220: ...TM 55 1520 228 10 Figure 7 15 Cruise Chart Sheet 6 of 13 7 68 ...
Page 221: ...TM 55 1520 228 10 Figure 7 15 Cruise Chart Sheet 7 of 13 7 69 ...
Page 222: ...TM 55 1520 228 10 Figure 7 15 Cruise Chart Sheet 8 of 13 7 70 ...
Page 223: ...TM 55 1520 228 10 Figure 7 15 Cruise Chart Sheet 9 of 13 7 71 ...
Page 224: ...TM 55 1520 228 10 Figure 7 15 Cruise Chart Sheet 10 of 13 7 72 ...
Page 225: ...TM 55 1520 228 10 Figure 7 15 Cruise Chart Sheet 11 of 13 7 73 ...
Page 226: ...TM 55 1520 228 10 Figure 7 15 Cruise Chart Sheet 12 of 13 7 74 ...
Page 227: ...TM 55 1520 228 10 Figure 7 15 Cruise Chart Sheet 13 of 13 7 75 ...
Page 231: ...TM 55 1520 228 10 7 79 Figure 7 17 Climb Descent Chart C ...
Page 233: ......
Page 234: ......
Page 235: ......
Page 237: ...TM 55 1520 228 10 Figure 7 19 Idle Fuel Flow Chart 7 85 7 86 blank ...
Page 238: ......
Page 242: ...TM 55 1520 228 10 8 4 Change 10 Figure 8 1 Exterior Check Diagram ...
Page 256: ......
Page 259: ...Figure 9 1 Emergency Exits and Equipment Sheet 1 of 2 Change 14 9 3 TM 55 1520 228 10 ...
Page 260: ...Figure 9 1 Emergency Exits and Equipment Sheet 2 of 2 9 4 Change 14 TM 55 1520 228 10 ...
Page 261: ...Figure 9 2 Autorotational Glide Characteristics Chart Change 14 9 5 TM 55 1520 228 10 ...
Page 268: ...SECTION II MISSION EQUIPMENT NOT APPLICABLE 9 12 Change 14 TM 55 1520 228 10 ...
Page 270: ......
Page 282: ......
Page 284: ......
Page 286: ......
Page 292: ...PIN 014142 000 ...