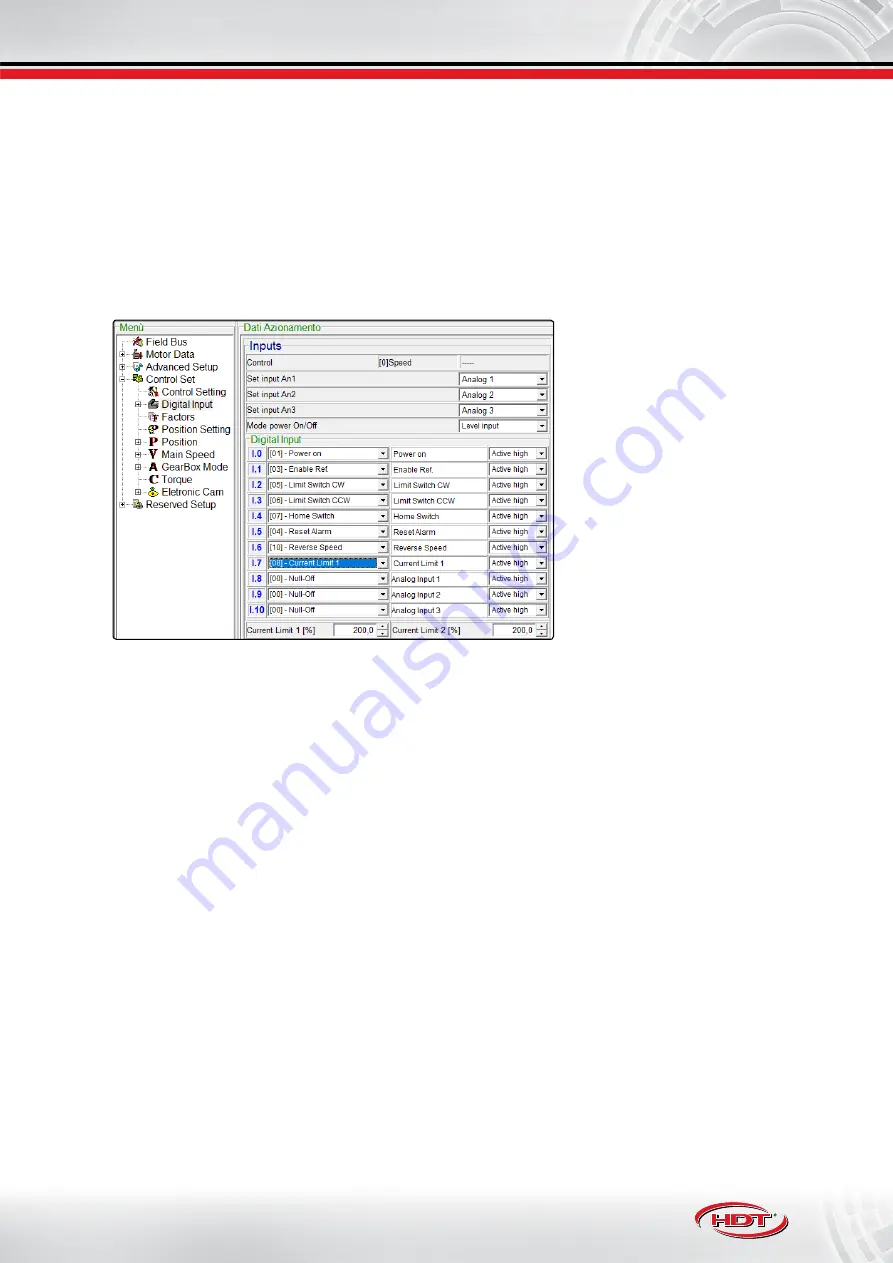
83
NTT 240/460
Operation mode
Installation and user guide
Rev: 4.0
6.08 Digital I/O
Digital input (also analog input used as digital input) and output ports are totally configurable with all theri input
function, so they are not linked to hardware input position, exception for 2 input capture functions, as Touch
Probe.
To learn more about digital I/O functions according to choosen operation mode, please see
, and for information about I/O topology, please see
“5.10 J7-8-9 connectors: Frequency, digital
Please remember that ‘Digital Input’ sub item is nested in Menu item releated to desired operation mode; for
example, a kind of useful configuration for digital input functions, with related settings, during speed control in
I/O operation mode is shown below:
Setting into window is shown below:
• setting input 6 and 7 as analog or digital
input.
• setting Power ON/OFF activation type
between Level or Edge of selected input
signal.
• setting input function from dropdown
menu and desired logic state.
Digital input functions are listed below:
1.
Power ON
o
Switch ON
: motor locked in torque standstill condition command.
2.
Power ON/Reset
: reset alarms and torque standstill condition joint command.
3.
Power/Operat.
: torque standstill condition and reference enabled joint command.
4.
Power/Operat./ Reset
: reset + torque stan reference enabled joint command.
5.
Enable Reference
o
Enable Operation
: reference enabled command.
6.
Start Reference
: Start position command.
7.
Halt
: Halt command.
8.
Position Abs./Rel.
: target conversion between absolute and relative and viceversa.
9.
Reset Alarms
o
Fault Reset
: drive alarms reset command.
10.
Limit Switch CW
and
Limit Switch CCW
: input for clockwise (CW) and counterclockwise limit switch (CCW).
11.
Home Switch
: input for Home switch.
12.
Current limit 1
and
Current limit 2
: input for 1
ST
and 2
ND
torque limit at specified percentage value.
13.
Reverse Speed
: reverse speed command.
14.
Home Position
: start Home Position procedure command.
15.
JOG+
and
JOG-
: speed JOG command.
16.
Selection-Start
: target table selection input and start per input-start position control.
17.
Reference Select(0-5)
: target table selection input via Modbus operation mode.
18.
Reset Index
: cyclic positioner index reset.
19.
Position on Input X
: index stop, at relative position, when event happens on defined Input.
20.
Measure position on In X
: start/stop position measurement on defined input.
21.
Selection Cam
: electronic cam table selection input.
22.
Input Sync Cam
: electronic cam sync input.
23.
Input Sync Slave
: electronic cam slave module sync input.
Summary of Contents for NTT 240
Page 129: ......