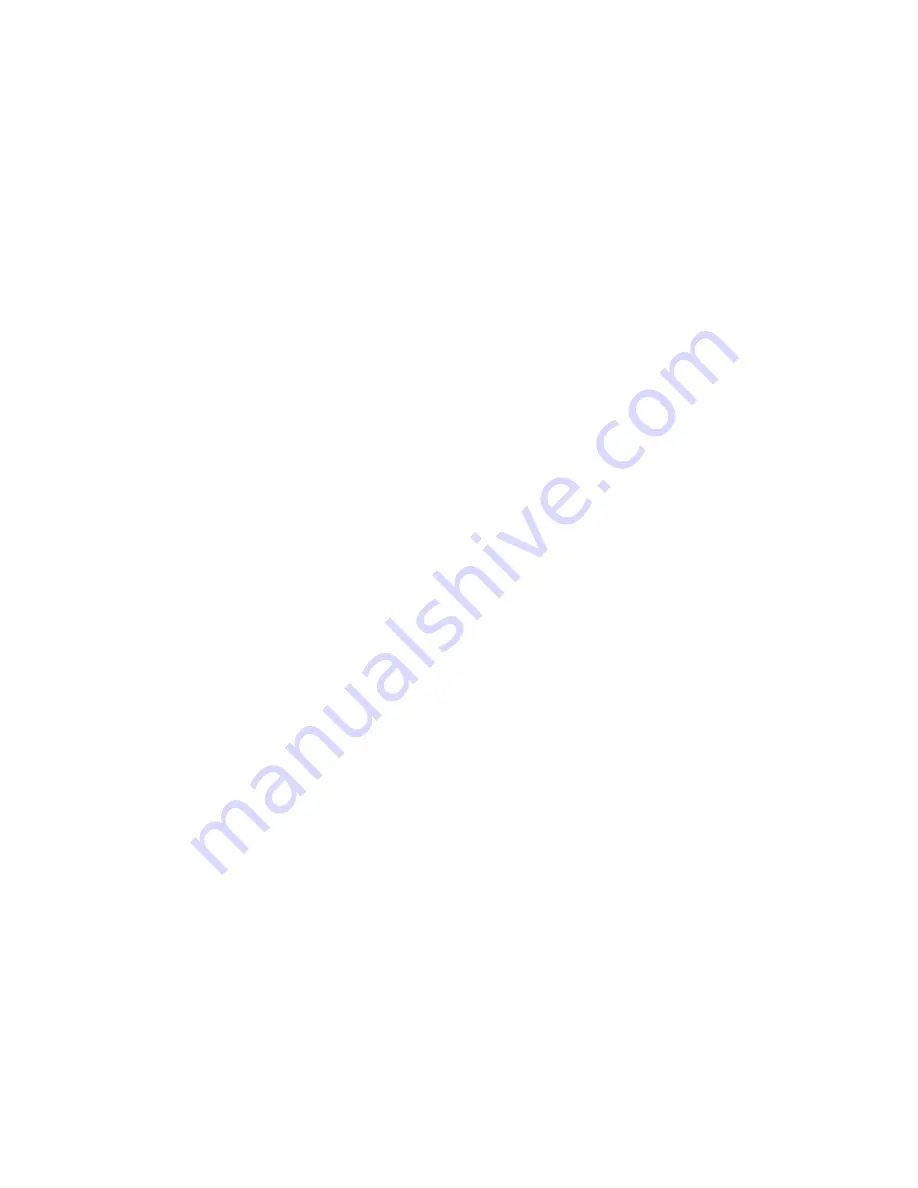
7
CAMFIRE Heater Specifications
MODEL CV125CG MOD D
Input Heat Rating
BTU/Hour
90,000
– 120,000
Output Ratings
Clean-Air Output, BTU/Hour
60,000 - 70,000
Volume, CFM (Approximate)
600
Other Ratings
Current, Running
4.0 Amps
Voltage
120 VAC
Frequency
60 Hz
Air Pump Pressure
5.0 PSI
Fuel Nozzle
Meter Size
0.65 GPH
Spray Angle
80 Degrees
Fuel
Kerosene, DF1, DF2, Fuel Oil, JP8 Only
Tank Capacity
12.0 Gal (45.5 Litres)
Duct
(Refer to Venting Instructions)
Dimensions
W16” L48” H23”
40 x 122 x 58 cm
Weight
(Without Fuel)
74 lbs (33 Kg)
Summary of Contents for Camfire CV125CG
Page 3: ...4 ...
Page 24: ...25 Figure 6 Test Probe ...
Page 30: ...31 SECTION 6 Illustrated Parts List ...
Page 31: ...32 HEATER ASSEMBLY ...
Page 33: ...34 HEATER INTERNAL EXPLODED VIEW ...
Page 35: ...36 MOTOR AND PUMP ASSEMBLY ...
Page 37: ...38 BURNER HEAD ASSEMBLY ...
Page 39: ...40 WHEEL KIT ...