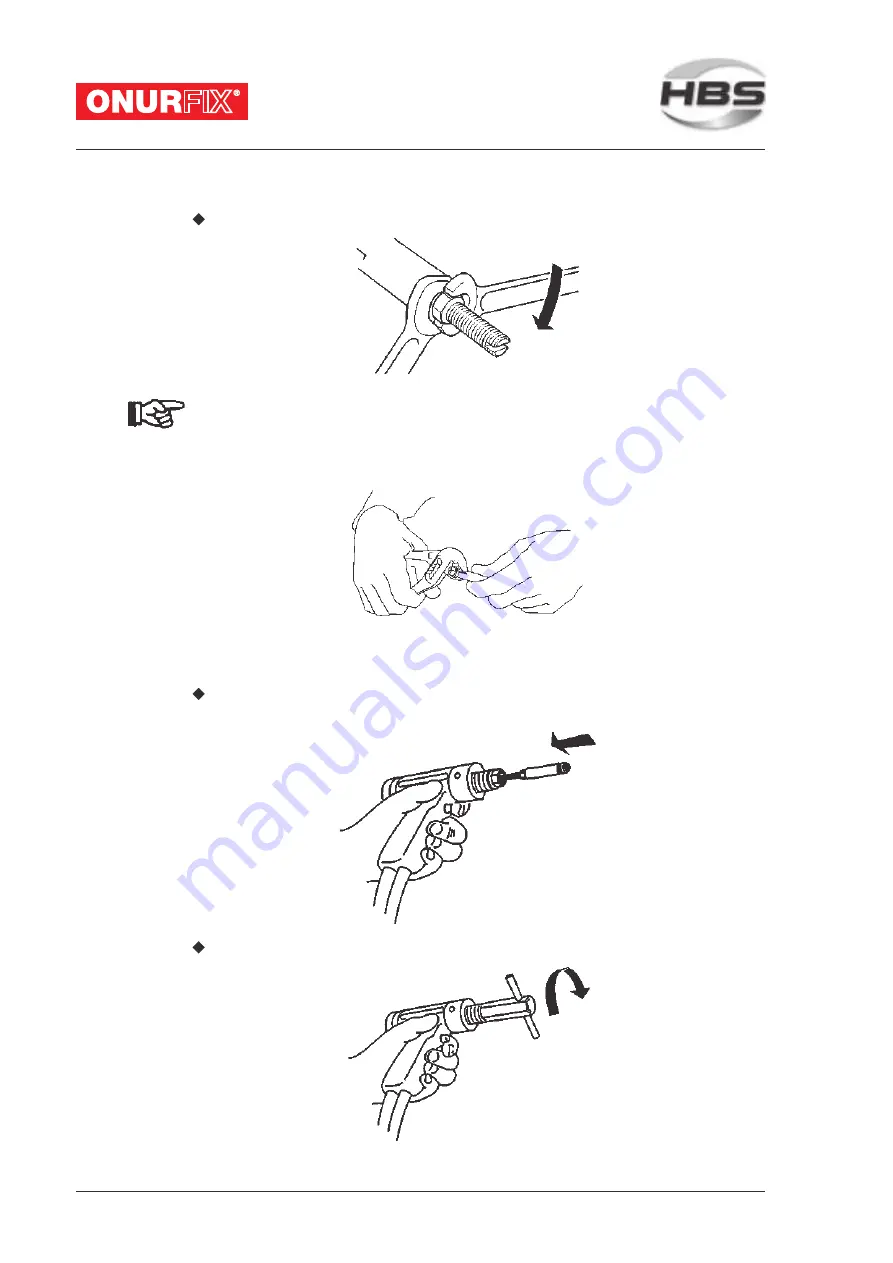
20
C 08 Order No. BA 92-20-256 Issue 01.03.08
Retighten the retaining nut.
Retighten regularly and carefully the chuck at the four
segments (see figure below, at the visible end of the chuck)
using pliers to ensure a proper current transition. This will
prevent early wear through spark erosion.
4.3
Installation of Chuck
Put the chuck with loose retaining nut up to the stop into the piston of the
welding gun.
Tighten the retaining nut with the socket wrench SW 17.