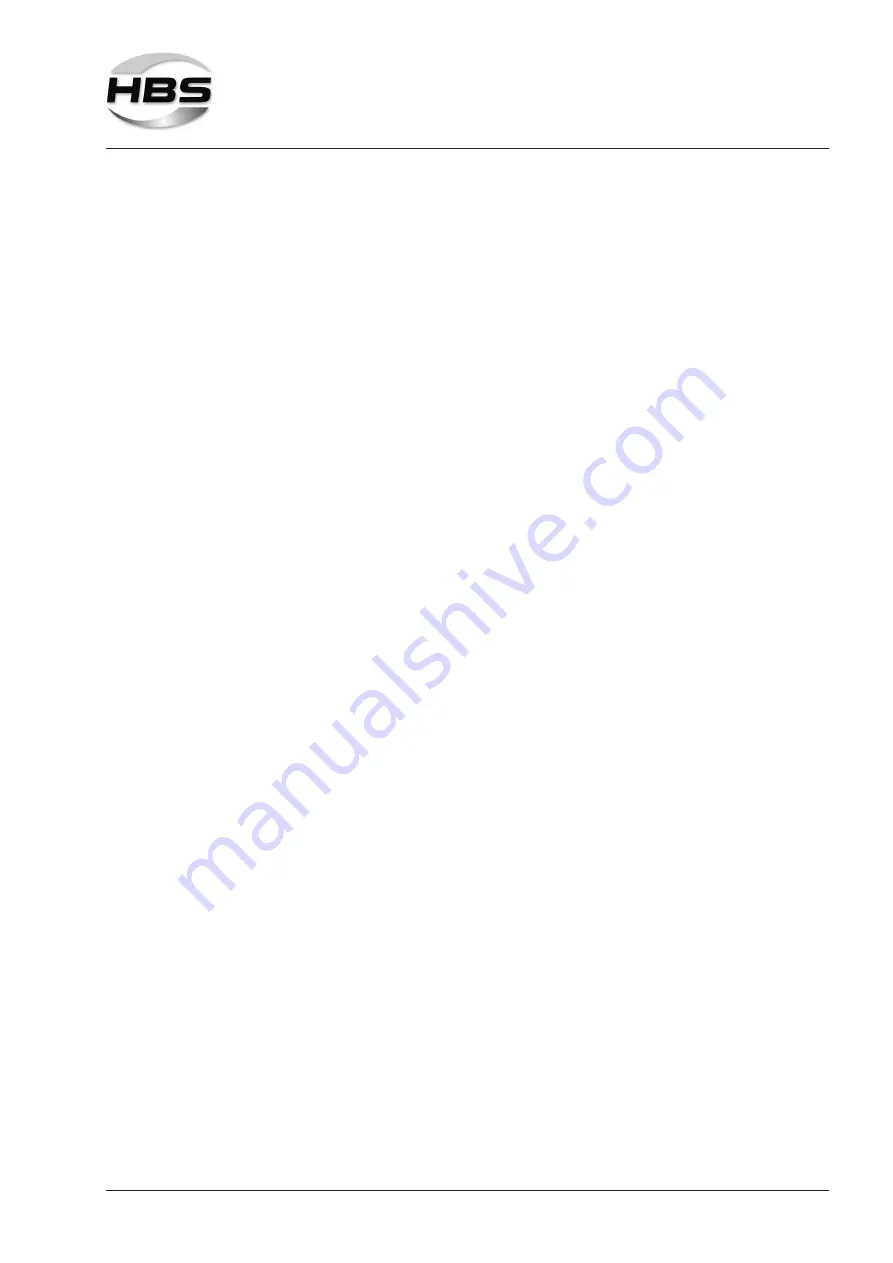
19
©HBS Bolzenschweiss-Systeme GmbH & Co. KG
All rights reserved – Reprinting, in whole or in part, only with the approval of the manufacturer
8 Components of the Stud Welding Unit
The mains alternating voltage is converted to direct voltage in the
charging de-
vice (1)
. Charging of the
welding capacitors (3)
is performed with the charging
device and is fully adjustable. The welding capacitors store the energy required for
the welding process. The quantity of energy is defined by the operator via the char
-
ging voltage.
The
welding thyristor (4)
releases the charging voltage.
The charging process and the welding process are controlled by the
control sys-
tem (2)
.
The negative pole of the capacitor is connected to the welding gun. The positive
pole is usually connected to the workpiece via vice grips.
The type plate is located on the backside of the stud welding unit.
Type plate
The type plate contains the following information:
– Manufacturer
– Type
– Order No./Serial No.
– Primary voltage
– Fuse
– Power consumption
– Cooling class
– IP code
– Date
Summary of Contents for 92-10-0502
Page 53: ......