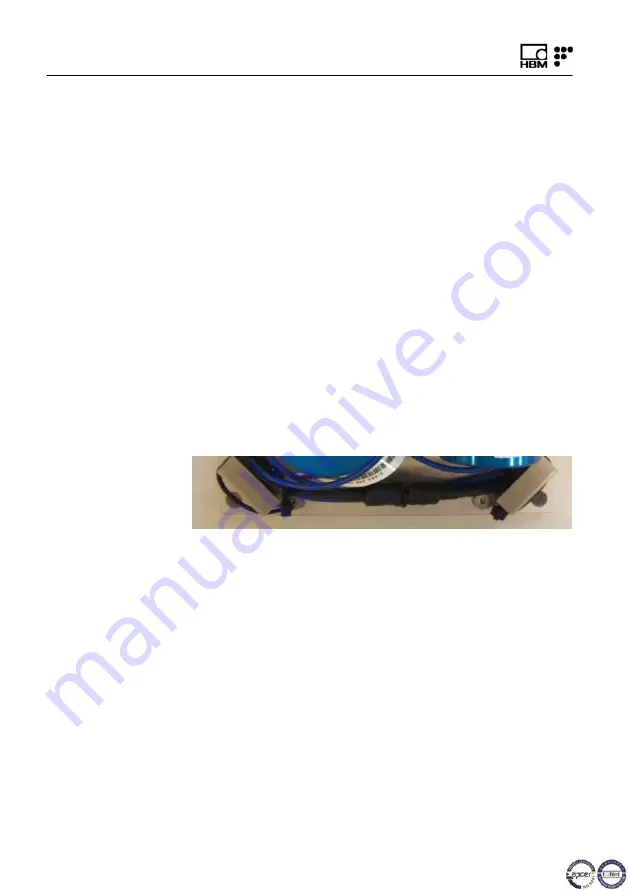
Sensor Installation
20
A4265-2.3
HBM: public
FS65
2.2.3
Fixing the Assembly
The Bi or Triaxial assembly is now ready to be fixed to
the structure. The mounting base has 4 M6 holes for that
purpose. Four M6x20 screws are provided, but these can
be or not be suited for fixing the base to the structure.
The fixing method should be carefully defined.
2.2.4
Protecting the Sensors
Although the accelerometer is IP68 rated, the performed
connections on the assembly are not. This means that
for outdoor usage of the assembly arranged as above
should have the connectors protected against moisture
and dust. HBM FiberSensing suggests the use of a vul
canizing tape around the connectors and adapter
(
).
Fig. 2.23
For mechanical protection and external cover of the Bi or
Triaxial Assembly, HBM FiberSensing has a specially
designed cover.
It is prepared to be screwed to the surface with 8 M6x20
screws and has two holes for cable exiting.