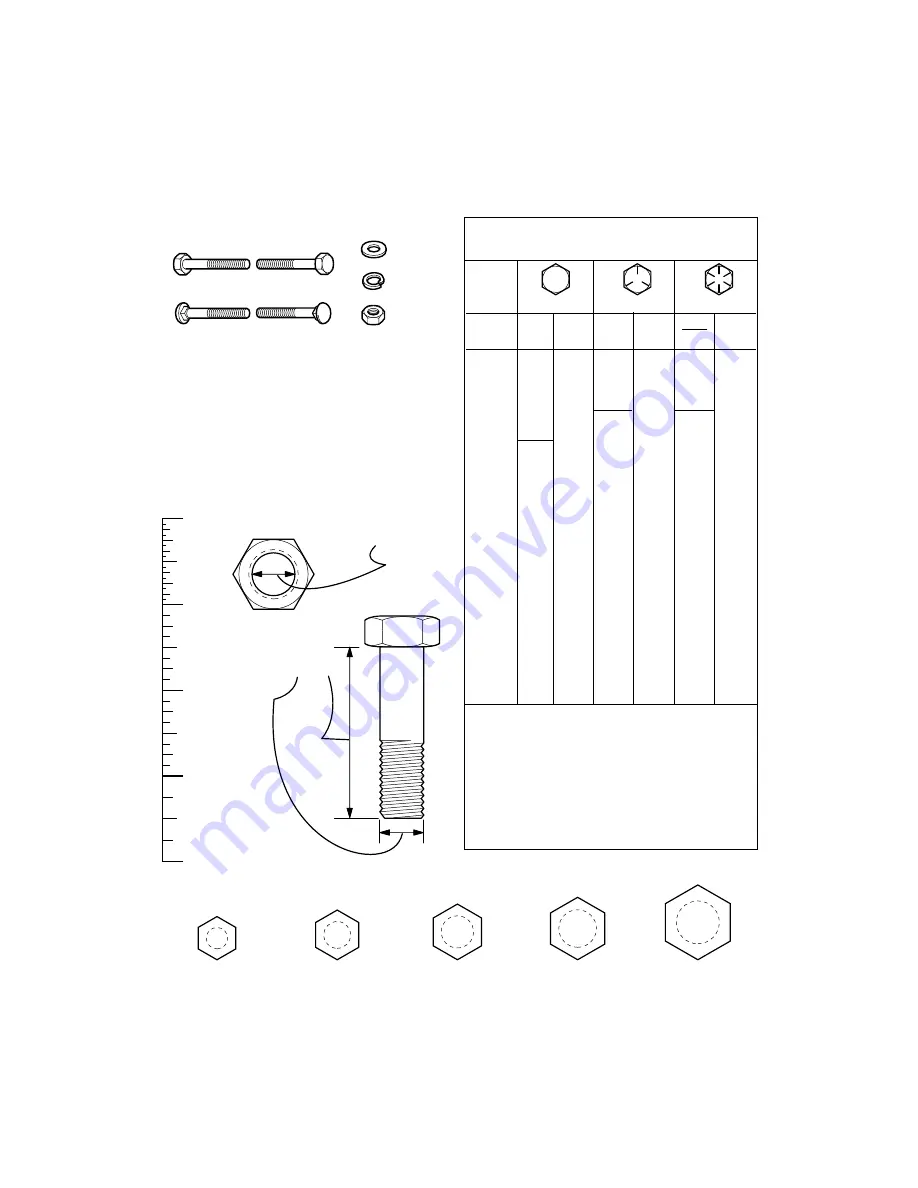
Torque Specification Chart
FOR STANDARD MACHINE HARDWARE (Tolerance ± 20%)
Hardware
Grade
SAE Grade 2
SAE Grade 5
SAE Grade 8
Size Of
in/lbs
in/lbs
in/lbs
Hardware
ft/lbs
Nm.
ft/lbs
Nm.
ft/lbs
Nm.
8-32
19
2.1
30
3.4
41
4.6
8-36
20
2.3
31
3.5
43
4.9
10-24
27
3.1
43
4.9
60
6.8
10-32
31
3.5
49
5.5
68
7.7
1/4-20
66
7.6
8
10.9
12
16.3
1/4-28
76
8.6
10
13.6
14
19.0
5/16-18
11
15.0
17
23.1
25
34.0
5/16-24
12
16.3
19
25.8
27
34.0
3/8-16
20
27.2
30
40.8
45
61.2
3/8-24
23
31.3
35
47.6
50
68.0
7/16-14
30
40.8
50
68.0
70
95.2
7/16-20
35
47.6
55
74.8
80
108.8
1/2-13
50
68.0
75
102.0
110
149.6
1/2-20
55
74.8
90
122.4
120
163.2
9/16-12
65
88.4
110
149.6
150
204.0
9/16-18
75
102.0
120
163.2
170
231.2
5/8-11
90
122.4
150
204.0
220
299.2
5/8-18
100
136
180
244.8
240
326.4
3/4-10
160
217.6
260
353.6
386
525.0
3/4-16
180
244.8
300
408.0
420
571.2
7/8-9
140
190.4
400
544.0
600
816.0
7/8-14
155
210.8
440
598.4
660
897.6
1-8
220
299.2
580
788.8
900
1,244.0
1-12
240
326.4
640
870.4
1,000
1,360.0
Hex Head Capscrew
Hex Nut
Lockwasher
Washer
Carriage Bolt
NOTES
1. These torque values are to be used for all hardware
excluding: locknuts, self-tapping screws, thread forming
screws, sheet metal screws and socket head setscrews.
2. Recommended seating torque values for locknuts:
a. for prevailing torque locknuts - use 65% of grade 5
torques.
b. for flange whizlock nuts and screws - use 135% of
grade 5 torques.
3. Unless otherwise noted on assembly drawings, all torque
values must meet this specification.
Hardware Identification & Torque Specifications
Common Hardware Types
Screw, 1/2 x 2
Body
Diameter
Body
Length
Inside
Diameter
Nut, 1/2”
No
Marks
3/8” Bolt or Nut
Wrench—9/16”
3/8
5/16” Bolt or Nut
Wrench—1/2”
5/16
1/4” Bolt or Nut
Wrench—7/16”
1/4
1/2” Bolt or Nut
Wrench—3/4”
1/2
DIA.
7/16
DIA.
7/16” Bolt or Nut
Wrench (Bolt)—5/8”
Wrench (Nut)—11/16”
Wrench & Fastener Size Guide
Standard Hardware Sizing
When a washer or nut is identified as
1/2”
, this is the
Nominal size, meaning the inside diameter is 1/2 inch; if a
second number is present it represent the
threads per inch
When bolt or capscrew is identified as
1/2 - 16 x 2”
, this
means the
Nominal size, or body diameter is 1/2 inch; the
second number represents the
threads per inch (16 in this
example, and the final number is the
body length of the
bolt or screw (in this example 2 inches long).
The guides and ruler furnished below are designed to
help you select the appropriate hardware and tools.
0
1/4
3/4
1/2
1
1/4
3/4
1/2
2
1/4
3/4
1/2
3
1/4
3/4
1/2
4
P
PTS - 6