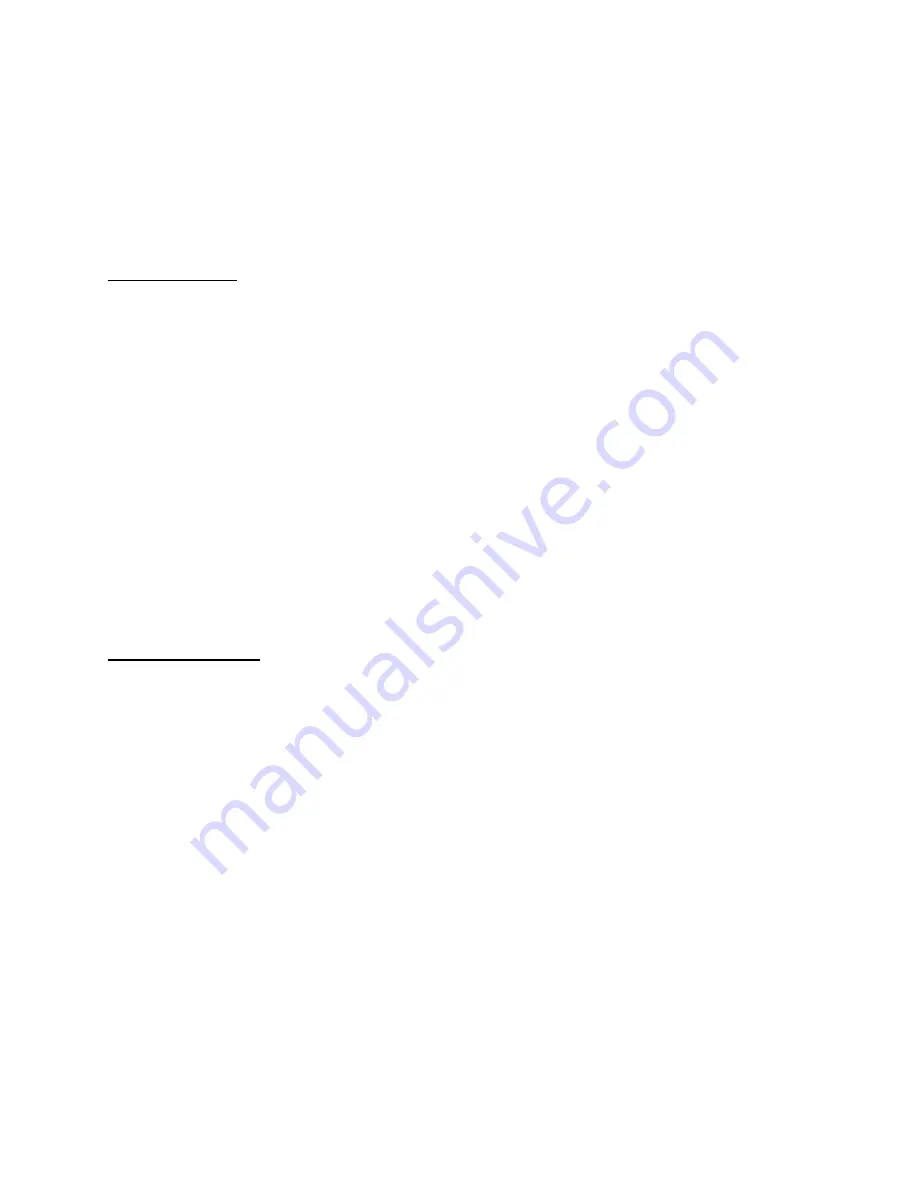
Page 10
NMC-9
13. Insert the pilot and flame detection system (if used) into the appropriate ports on the
mounting plate. The use of a Hauck blast type gas pilot (either spark or manually ignited) is
recommended.
Ensure that the pilot is placed in the port specifically designated for it.
The ports on all burners are normally equipped with a slip-fit cap and a setscrew. If the
furnace back pressure exceeds 1" wc, threaded ports are mandatory on all burners. For
proper installation, consult the instructions which accompany the pilot and detection system
chosen.
G. OPERATION
Once installed, the burner is ready for operation. The NMC burner is designed to operate with
the air, oil and gas pressure best suited to the application. Capacity and excess air tables are
given in Sections C of these instructions.
It is recommended that the burner be ignited under low fire conditions. When the burner is
operating, the pilot can be shutoff since the burner is designed to maintain ignition of the fuel-air
mixture.
The NMC mounting plate is provided with a port for monitoring the pilot and main flame, using a
UV scanner or other suitable device. If the pilot and secondary air are to be in line, a 45° No. 1
spark ignited gas pilot must be used with NMC210-230 model to avoid interference. (Alternately,
if a 9 o’clock secondary air position is required and it is desired to use the standard No. 1 pilot,
the mounting plate may be rotated so as to position the pilot at either the 12 o’clock or 3 o’clock
position).
Burners intended for preheated air operation are identified by the letter "H" immediately
preceeding the Model Number figures. Preheated air up to 800°F maximum may be utilized.
Atomizing air is maintained at ambient conditions during preheated air operation.
H. MAINTENANCE
The NMC Series burner has no moving parts requiring any lubrication. However, periodic
cleaning may be required to remove dirt and soot build-up inside the burner air passages
caused by a dirty air supply or soot blow back from the furnace during periods of shut down.
To maintain peak performance, oil valves and atomizers should also be periodically cleaned of
varnish and any soot deposits. To remove the oil valve/atomizer assembly, accomplish the
following:
A. Disconnect the oil line at the control valve inlet (if required).
B. Remove all of the screws on the atomizer backplate.
C. Extract the entire oil assembly.
D. Clean off all of the particles and residue using kerosene and a soft-wire brush.
E. Reinsert the assembly into the atomizer body.
F. Ensure that the backplate gasket is in good condition and properly seated in
place.
G. Replace all of the screws on the atomizer backplate.
H. Reconnect the oil line at the control valve (if required).
I. Burners equipped with self-cleaning "S" valves should have the valve handles
turned through the "clean" zone to remove any dirt in the metering mechanism.
The valve should then be reset to its previous setting.
Periodically check the refractory tile for coke build-up or other damage.
Summary of Contents for NMC200 Series
Page 3: ...Page 3 NMC 9 C CAPACITIES ...
Page 4: ...Page 4 NMC 9 D DIMENSIONS Figure 1 Dimensions NMC 210 NMC 240 Y2466 NOT TO SCALE ...
Page 5: ...Page 5 NMC 9 Figure 2 Metric Dimensions NMC 210 NMC 240 Y2466 METRIC NOT TO SCALE ...
Page 6: ...Page 6 NMC 9 Figure 3 Dimensions NMC 260 Y2467 NOT TO SCALE ...
Page 7: ...Page 7 NMC 9 Figure 4 Metric Dimensions NMC 260 Y2467 METRIC NOT TO SCALE ...