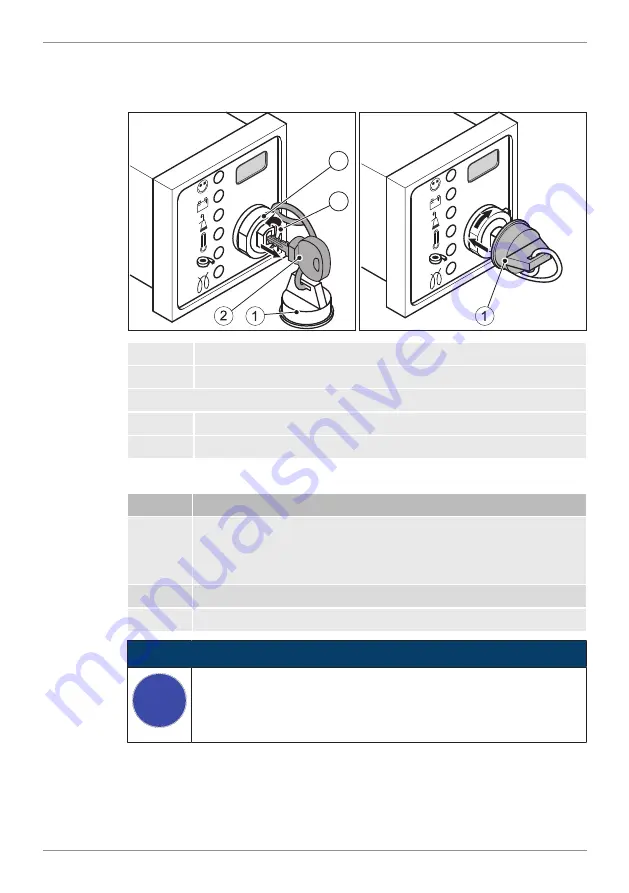
Operation and use
2-4L41C, 2-4M41(Z), 4L42C, 4M42
54
HATZ
Manual
7.6.2
Switching off the engine (electrical)
Overview — HATZ instrument boxes
0
I
1
Protective cap
2
Starting key
Ignition lock
0
Off
I
Operation
Procedure
Step
Activity
1
Turn the starting key (2) to position "0".
The engine switches off.
All indicator lamps go out.
2
Remove the starting key.
3
Seal the ignition lock with the protective cap (1).
NOTICE
i
Danger of exhaustive battery discharge.
▪
When the machine is switched off, always turn the starting
key to position "0" or else the battery may become fully dis-
charged.
Summary of Contents for 2-4L41C
Page 2: ......