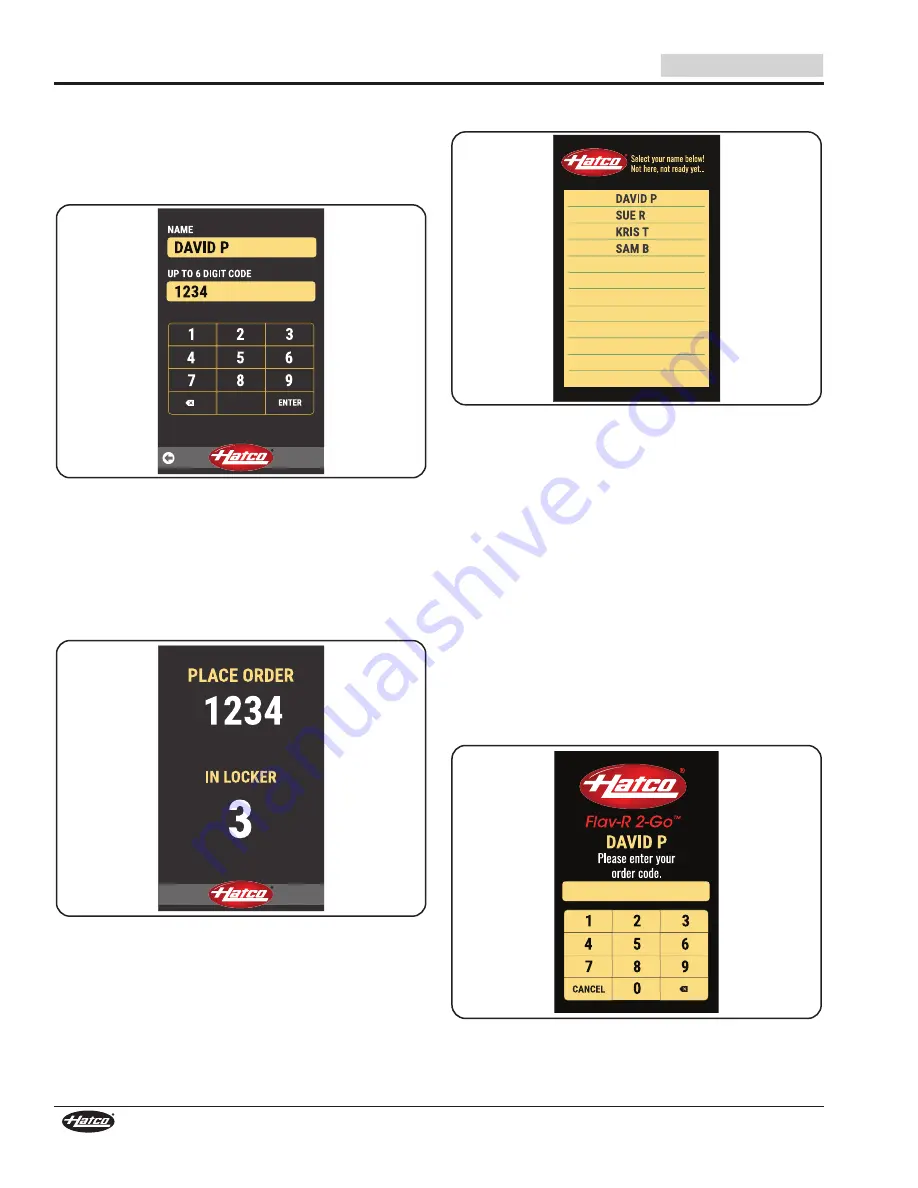
12
Form No. F2GM-0620
English
OPERATION
4. Type the order code and touch ENTER.
• The order code can be up to 6 digits.
• The name will appear on the customer-side screen to
identify their order.
• The order code will be used by the customer to unlock
their locker(s).
0
Enter Code Screen
NOTE: If the order code is currently in use, the unit will not
accept it. The unit will notify the operator to “Please
enter a new order code.”
5. When the Place Order screen is displayed, place the food
order into the locker(s) shown on screen.
• The timer will begin to count up on the Select Lockers
screen. The maximum order time is factory set to 45
minutes.
Place Order Screen
NOTE: Refer to the “Overtime Order” procedure for more
information about orders that stay in a locker past the
maximum order time.
Picking up an Order (Customer Side)
Use the following procedure to unlock and remove food from a
locker on the customer side. A general outline of this procedure
should be provided to the customer.
1. On the Orders Ready screen, touch the name the order
was placed under.
• If the customer’s name is not shown on the list, their
order is not ready.
Orders Ready Screen
2. Enter the order code.
• If the order code is entered correctly, the screen will
notify the customer to: “Please remove your items from
your lighted locker!”
- The LED lights for the corresponding locker will flash
three times, then stay illuminated while the locker
remains unlocked.
- The locker(s) will remain unlocked for 20 seconds.
NOTE: If the customer does not remove the food order within
20 seconds, the customer’s name will disappear from
the list, and an operator will need to remove the order
manually. For single-sided models, refer to the “Open a
Locker Manually” procedure in this section.
• If the order code is entered correctly, but the maximum
order time has been exceeded, the screen will notify the
customer to “Please see staff to reorder!”
• If the order code is entered incorrectly, the screen will
notify the customer to “Please try again!” After the second
incorrect attempt, the customer can select to TRY AGAIN.
Enter Order Code
3. Open locker(s) with flashing lights and remove food.
• The locker(s) will remain unlocked for 20 seconds. The
LED lights will flash white light three times and stay
illuminated while the locker is unlocked.