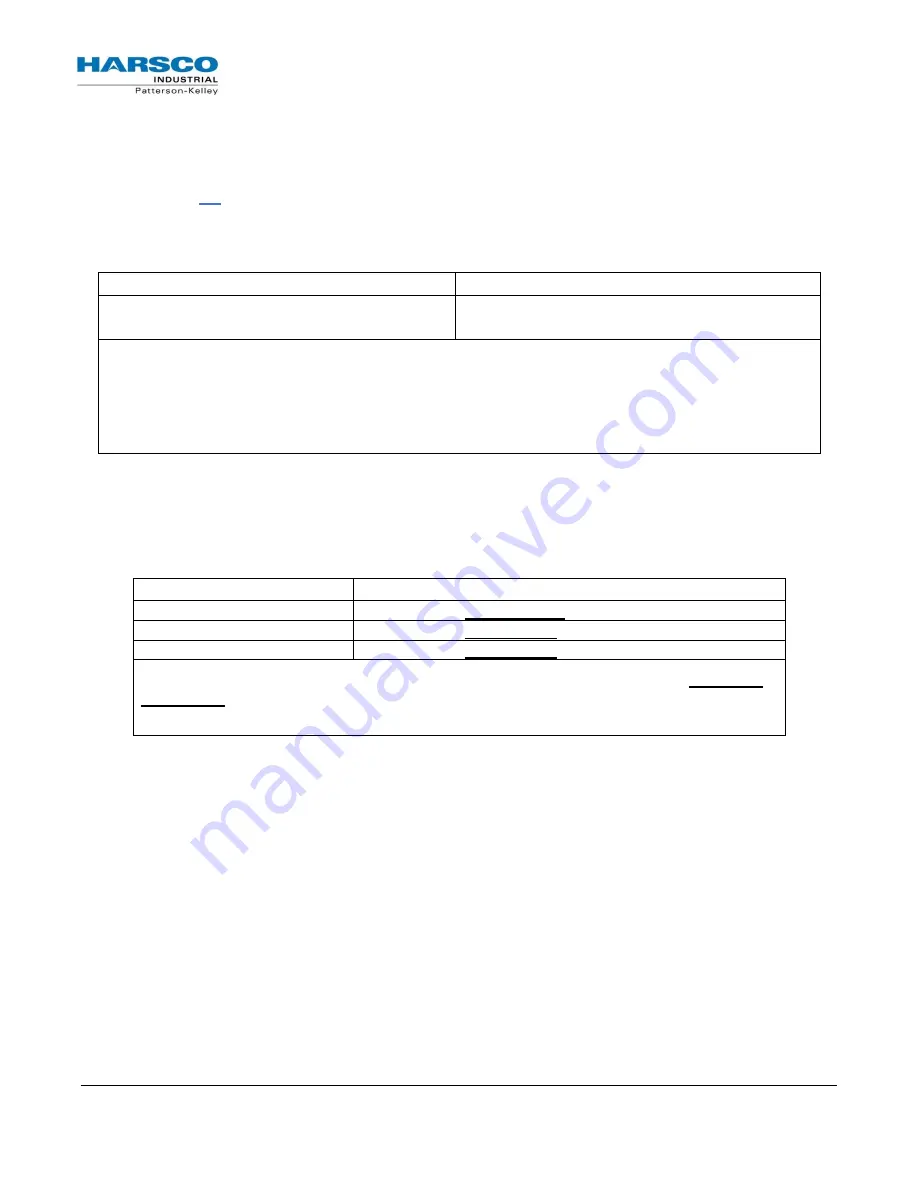
P-K SONIC
®
Gas Fired Boiler
Technical Service 1.877.728.5351
Revised: June 2, 2017
Released: June 2, 2017
HARSCO Industrial, Patterson-Kelley 2017
All Rights Reserved.
1004905978 P-K SONIC NURO Installation and
Owners Manual (Rev F Jun-2017).docx
Page 102
Appendix E
– Installation and Quick Reference
Fuel/Gas Supply
Refer to
for information on proper sizing of the gas supply piping. Undersized gas piping
with too much pressure drop will negatively impact the boiler’s performance.
Install a lock-up type gas regulator to supply an appropriate gas pressure as described below:
Natural Gas
Propane Gas
Minimum Inlet Pressure = 4
.0”
W.C
.
Maximum Inlet Pressure = 14.0”
W.C.
Minimum Inlet Pressure = 7
.0”
W.C.
Maximum Inlet Pressure = 14.0”
W.C.
NOTE:
Harsco Industrial, Patterson-Kelley recommends installing an individual lock-up type gas
regulator in the gas supply piping to each boiler. For installations where one master lock-up type
gas pressure regulator will service multiple boilers, Patterson-Kelley recommends contacting the
local regulator representative for application assistance specifying the appropriate lock-up type
regulator and gas pipe sizing.
Electrical/Power Supply
Carefully inspect the boiler’s nameplate labels which describe the power supply requirements.
Provide an appropriate power feed to the boiler with overcurrent protection:
Boiler Model
Power Supply Requirements
SC-1500 / SC-2000 (240V)
208-240VAC,
single phase
, 60Hz sized for 15 Amps.
SC-3000 / SC-4000 (240V)
208-240VAC,
three phase
, 60Hz sized for 20 Amps.
SC-3000 / SC-4000 (480V)
460-480VAC,
three phase
, 60Hz sized for 20 Amps.
NOTE:
The SC-3000 & SC-4000
MUST
be ordered to the correct voltage!
IT IS NOT
POSSIBLE
to convert an SC-3000 or SC-4000 between the 240V and 480V
configurations in the field.
Prior to startup, carefully check all electrical connections for tightness as connections can come
lose during shipping.
Exhaust Venting
The
P-K SONIC
boilers are dual-certified as Category II & Category IV appliances, capable of
operating with slightly negative to slightly positive exhaust pressure. It is critical to ensure the
flue venting material is suitable for use with the boiler.
For Category II installations, ensure the flue venting system is designed to maintain a slightly
negative exhaust pressure
between -
0.01” W.C. and -0.05” W.C.
For Direct Vent / Sealed Combustion Category IV installations, ensure the flue venting system is
designed to maintain a slightly positive exhaust pressure
b0.01” and +0.22” W.C.
For Exhaust Only Category IV installations, ensure the flue venting system is designed to
maintain a slightly positive exhaust pressure
b0.01” and +0.4” W.C.