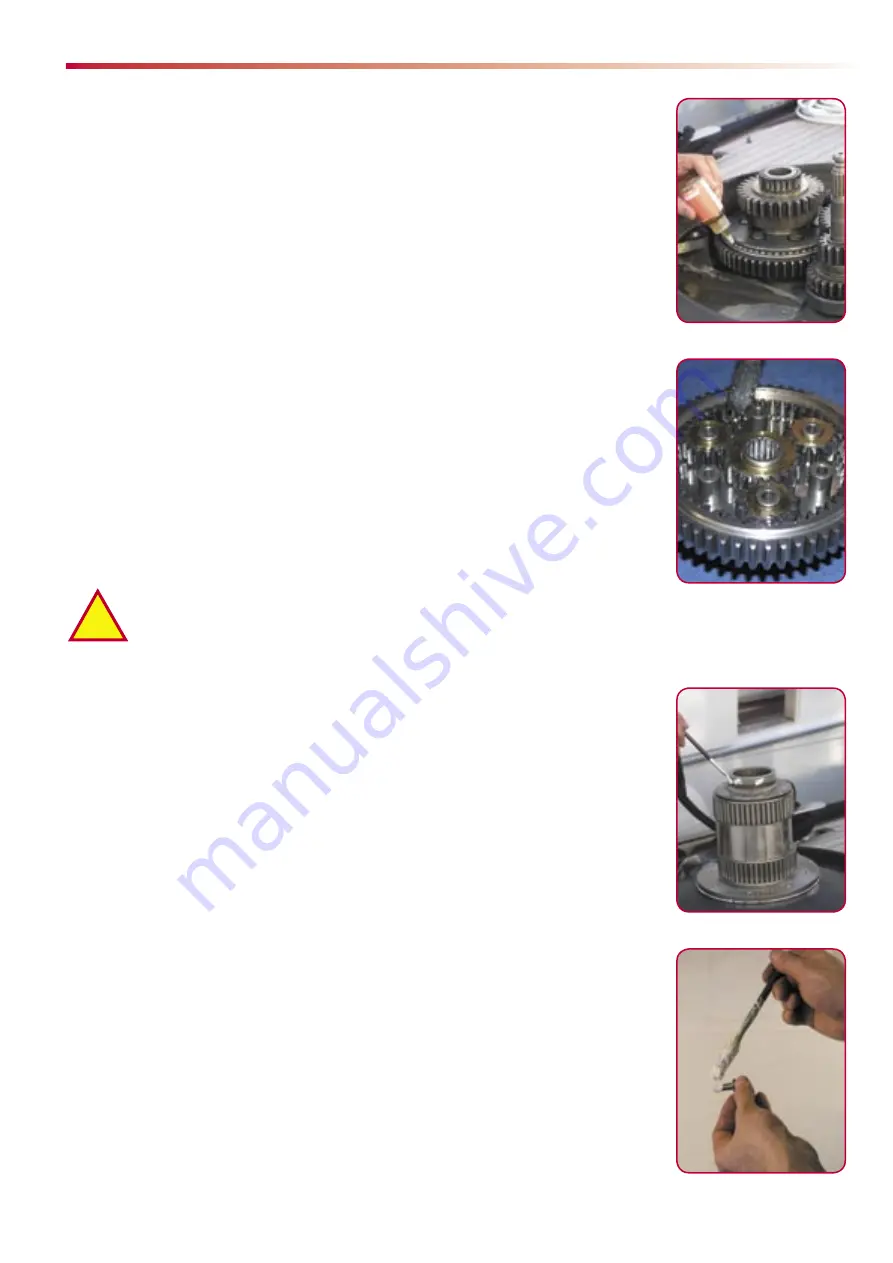
B1140 Winch
42
Maintenance
Maintenance products
OIL HARKEN BK 4521.
Apply the oil to the parts indicated, taking care to lubricate the surfaces completely.
Rotate or slide the oiled parts to distribute the product in a uniform way. Remember to oil
the pawls and not to use grease on them.
SYNTHETIC GREASE HARKEN BK 4513.
Apply a film of grease with a brush to all the parts indicated, and make sure that the film is
visible. Take special care when greasing the teeth of the ring gears, the gears and the roller
bearings. It is important to keep the teeth of the ring gears of our winches greased to increase
their efficiency and life.
Fig. 36
Fig. 37
WARNING!:
Parts, and especially the gears of the winch that are not sufficiently greased will undergo
irreversible wear that is not covered by the warranty.
!
ANTI CORROSIVE LUBRICANTS (i.e. DURALAC or TEFGEL).
Apply sacrificial anodes or anti corrosive lubricants to prevent electrolytic corrosion between
different metals in contact with one another. Apply the anti corrosive lubricant with a brush
on clean surfaces.
Fig. 38
ANTI SEIZING (i.e. SAF-T-EZE Anti –Seize or LANOCOTE).
This product is used to prevent problems of seizing caused by oxidation. We recommend using
this or similar products on stainless steel screws where the use of Loctite is not specifically
requested. Apply the anti-seize with a brush.
Fig. 39
Summary of Contents for B 1140 LH RACING
Page 1: ...WINCH MANUAL B1140 WINCH MANUAL...
Page 7: ...B1140 Winch 7 Technical information and characteristics Exploded view Fig 3...
Page 8: ...B1140 Winch 8 Technical information and characteristics Exploded view Fig 4...
Page 15: ...B1140 Winch 15 Fig 9 Technical information and characteristics Exploded view...
Page 16: ...B1140 Winch 16 Fig 10 Technical information and characteristics Exploded view...
Page 44: ...B1140 Winch 44 Maintenance Esploded view Fig 41...