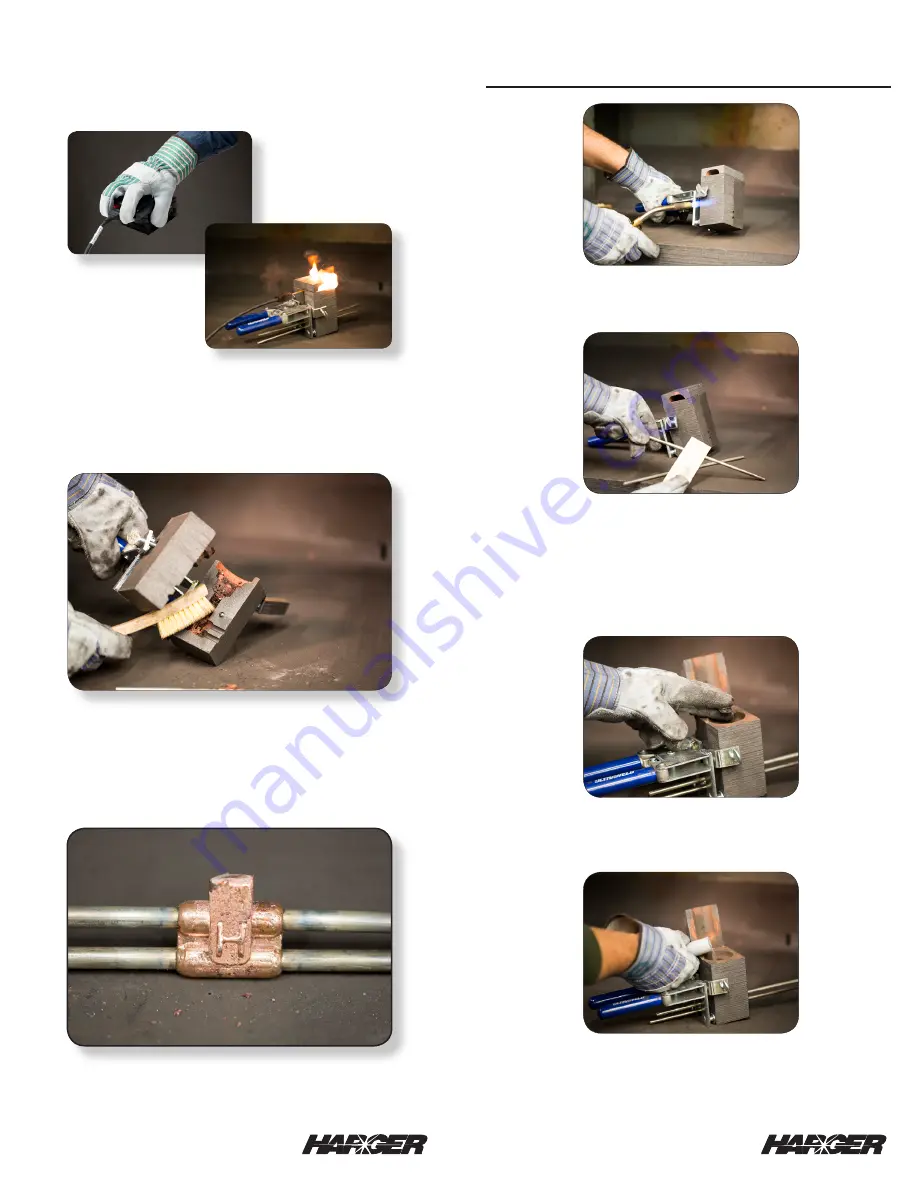
®
www.harger.com
®
www.harger.com
®
www.harger.com
5
step
4
Push and hold both igniter buttons at the same time.
step
5
Open mold and remove connection, remove
slag and clean mold before making the next
connection.
A Completed UltraShot
®
connection
®
www.harger.com
6
Making a NUWTube
Connection
(pour-in steps)
Step 1:
Torch dry the mold before
making the first connection.
Step 2:
Clean and dry conductors, insert
conductor into mold, close
handle clamp and lock mold.
Step 4:
Remove Clear plastic cap from
NUWTube, pour weld metal into
mold.
Step 3:
Insert disk into mold.