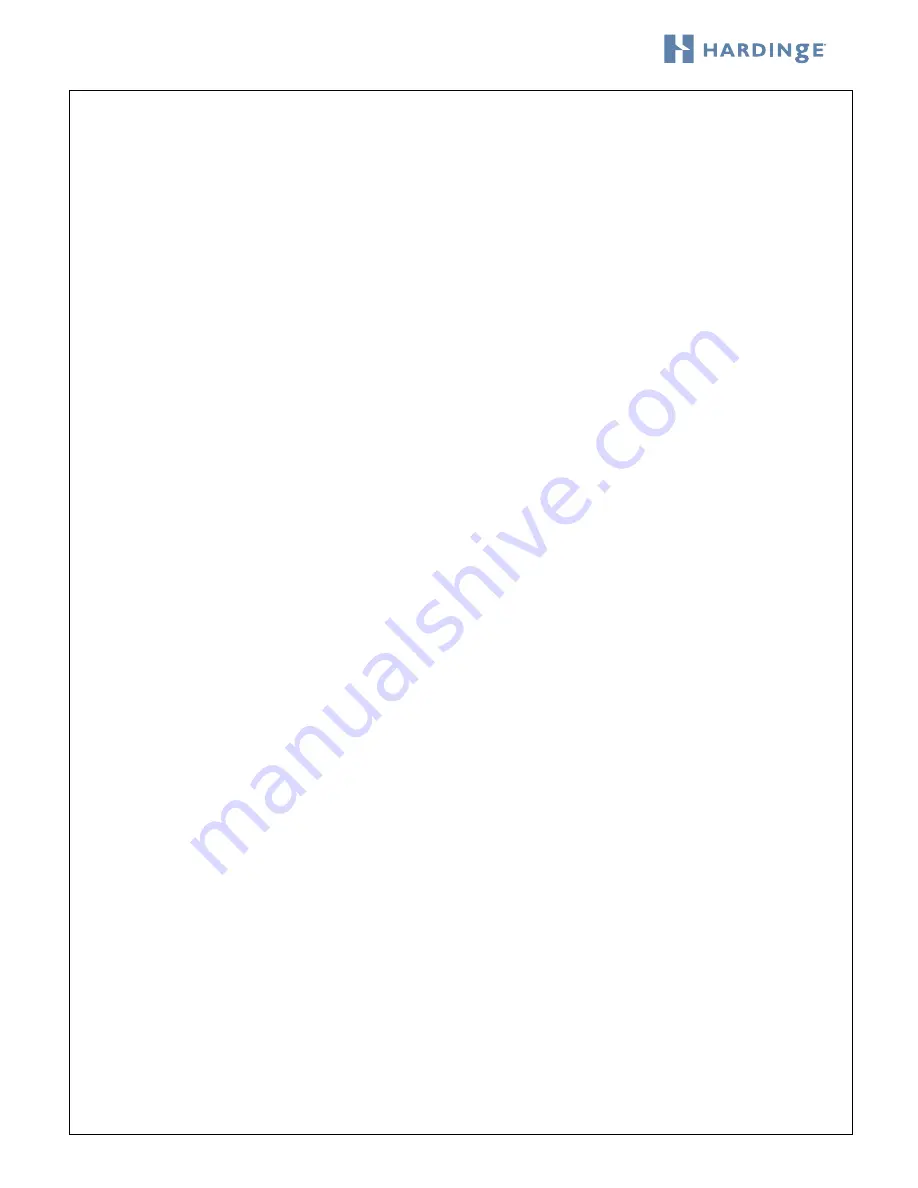
2
65mm FlexC
™
Collet System Style DL
Instructions B-152C
Hardinge Inc. One Hardinge Drive, Elmira, New York U.S.A.
1
4902-
1
507 800.843.8801 (Canada 800.468.5946) www.shophardinge.com
Par
t No
. BC -0009500-0152
General Safety Information
Before installing the Hardinge
®
FlexC
™
Collet System on your machine tool, thoroughly read this manual and understand
the information. If you are uncertain about any of the information, see your immediate supervisor. Also make certain that
you understand the information in your machine tool operator’s, programmer’s and maintenance manuals.
NOTICE
Damage resulting from misuse, negligence or accidents
is not covered by the Hardinge FlexC warranty.
Information in this document is subject to change without notice.
In no event will Hardinge Inc. be responsible for indirect or consequential damage
resulting from the use or application of the product, or any of the information in this document.
This product is only to be used by trained machinists skilled
in the use and operation of collet systems and collet chucks on metal cutting machines.
Safety Requirements to the Turning Machine:
Check to see that the workpiece is properly gripped and seated in the collet head before beginning the machining cycle.
Do not unclamp the workpiece until the machining cycle has come to a complete stop.
Observe all safety precautions indicated in the machine manual when operating the machine including the use of guards
and keeping the door closed during machining.
Do not exceed the maximum operating force and rpm for the Hardinge FlexC Collet Systems indicated below:
Maximum operating force: 10,100 lb (45KN)
Maximum RPM: 6,000
Product Description and Use:
The Hardinge FlexC style DL Collet System consists of a spindle mount assembly. Vulcanized collet heads and wrenches are
purchased separately. The style DL Dead-length
®
Collet System can be used as a thru-hole for bar work or with a work
stop for chucking. The clamping heads consist of hardened steel segments that are joined together by a vulcanization pro-
cess. Their outstanding characteristics include parallel workpiece clamping, superb accuracy with a minimum of deformation
of the work piece, and quick-change capability. If the Hardinge FlexC style DL Collet System is used as a dead-length system
the work stop is inserted into the workstop adapter with the part stop wrench included. When part length control is not
required the work stop can be removed.
The Hardinge FlexC style DL 65mm Collet Systems use a push-to-close design with an axially-fixed collet head. They are
ideally suited for sub-spindles to maintain length control during secondary operations. The push-to-close design also avoids
axial stress between the spindles. The collet head is fixed in the spindle mount, while the drawbar moves forward and
closes the collet head.