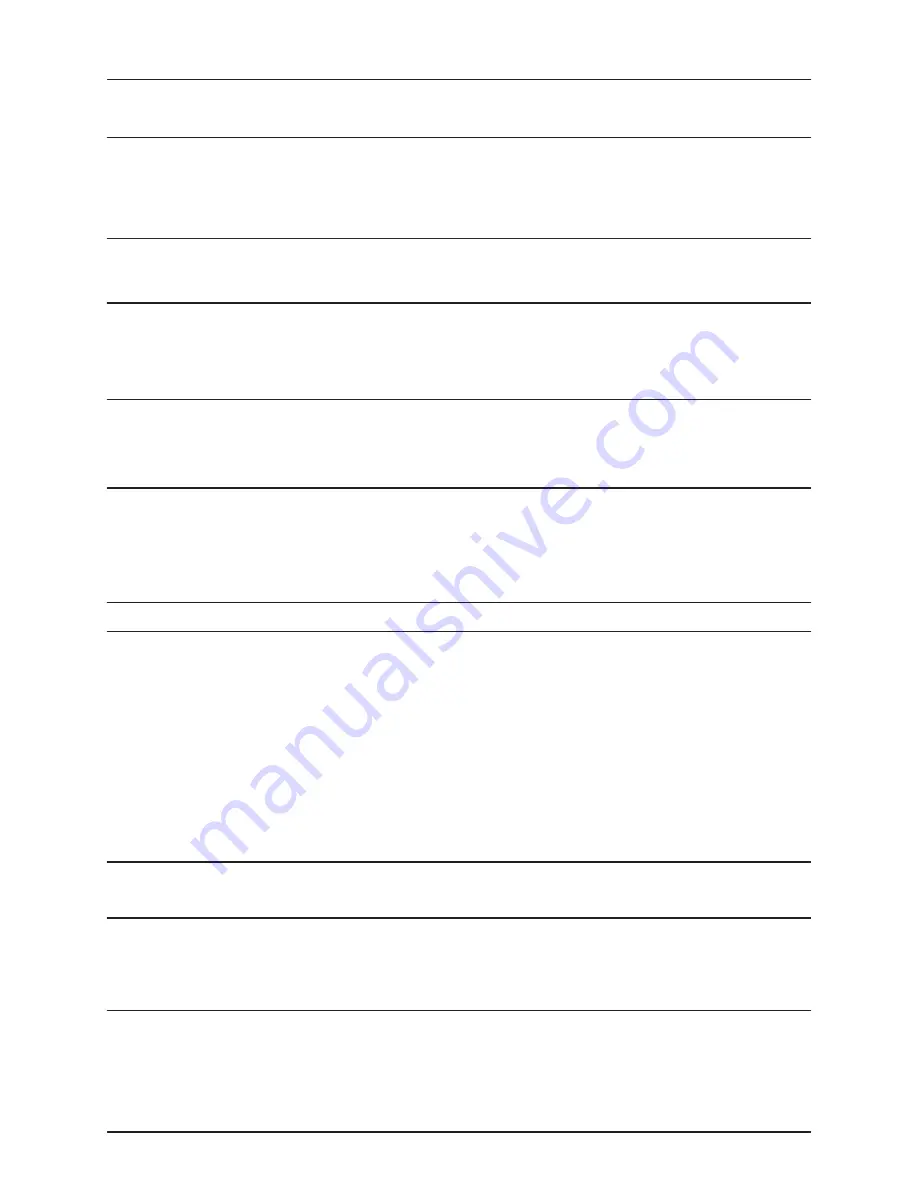
7 - Fault finding
7.2
Liquid system
Hydraulic system - HY model.
FAULT
PROBABLE CAUSE
CONTROL/REMEDY
No spray from boom when turned on.
Air leak on suction line.
Check if suction filter O-ring is sealing.
Check suction tube and fittings.
Check tightness of pump diaphragm and valve covers.
Suction/pressure filters clogged.
Clean filters.
Check for obstruction near tank sump elbow fitting.
Lack of pressure.
Incorrect assembly.
Check for obstruction near tank sump elbow fitting.
Pump valves blocked or worn.
Check for obstructions and wear.
Defective pressure gauge.
Check for dirt at inlet of gauge.
Pressure dropping.
Filters clogging.
Clean all filters. Fill with cleaner water. If using
powders, make sure agitation is on.
Nozzles worn.
Check flow rate and replace nozzles if it exceeds 10%.
Tank is air tight.
Check vent in tank lid is clear.
Sucking air towards end of tank load.
Lower pump r.p.m.
Pressure increasing.
Pressure filters beginning to clog.
Clean all filters.
Make sure bottom valve on CycloneFilter is not left in
closed position (marked with 1 dot) after flushing
boom. Operating position (marked with 2 dots) keeps
CycloneFilter clean.
Formation of foam.
Air is being sucked into system.
Check tightness/gaskets/O-rings of all fittings on
suction side.
Excessive liquid agitation.
Reduce pump r.p.m.
Check safety valve is tight.
Ensure returns inside tank are present.
Use foam damping additive.
Liquid leaks from bottom of pump.
Damaged diaphragm.
Replace. See changing of valves and diaphragms.
Operating unit not functioning.
Blown fuse(s).
Check mechanical function of microswitches. Use
cleaning/lubricating agent if the switch does not
operate freely.
Check motor. 450-500 milli-Amperes max. Change
motor, if over.
Wrong polarity.
Brown - pos. (+). Blue - neg. (-).
Valves not closing properly.
Check valve seals for obstructions.
Check microswitch plate position. Loosen screws
holding plate 1/2 turn.
No power.
Wrong polarity. Check that brown is pos. (+), Blue is
neg. (-).
Check print plate for dry solders or loose connections.
Check fuse holder are tight around fuse.
FAULT
PROBABLE CAUSE
CONTROL/REMEDY
Boom slow/erratic.
Air in system.
Loosen ram connection and activate hydraulics until
oil flow has no air in it (not whitish).
Insufficient hydraulic pressure.
Check output pressure of tractor hydraulics. Minimum
for sprayer is 2000 psi (130 bar).
Insufficient amount of oil in tractor reservoir.
Check and top if needed.
Ram not functioning.
Restrictor blocked.
Secure boom. Dismantle and clean. Change hydraulic
oil & filter.
Summary of Contents for RANGER 2000
Page 1: ...RANGER 2000 Instruction book 67022403 Version 1 00 US 02 2011...
Page 2: ......
Page 4: ......
Page 10: ...1 Welcome 1 2...
Page 48: ...6 Maintenance 6 2 Trailer lubrication oiling plan...
Page 64: ...6 Maintenance 6 18...
Page 78: ...8 Technical specifications 8 10 Charts Boom hydraulics HY Boom hydraulics HZ...
Page 81: ......